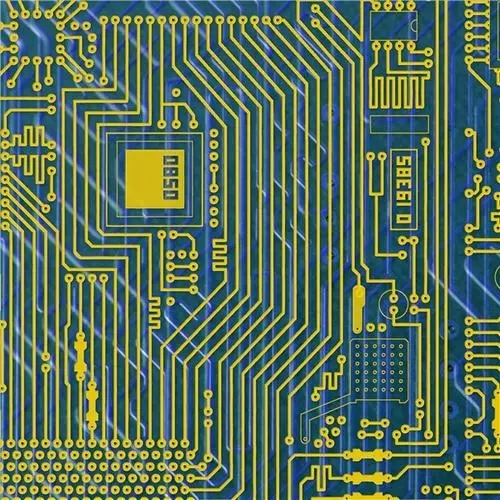
SMT processing welding spot quality and appearance inspection
With the progress of technology, some electronIC products, such as mobile phones and tablets, are becoming light, small and portable. The electronIC components used in SMT processing are also becoming smaller and smaller. A large number of resistance and capacitance components of 0402 have been replaced by 0201. How to ensure the quality of solder joints has become an important topic of high-precision placement. As a bridge of welding, the quality and reliability of solder joints determine the quality of electronic products. In other words, in the production process, the quality of SMT is finally expressed as the quality of solder joints.
At present, in the electronic industry, although the research of lead-free solder has made great progress, it has begun to be popularized and applied worldwide, and environmental protection issues have also attracted extensive attention. The soft soldering technology using Sn Pb solder alloy is still the main connection technology of electronic circuits.
A good solder joint should have no mechanical and electrical failure during the service life of the equipment. Its appearance is as follows:
(1) A complete, smooth, shiny surface;
(2) The proper amount of solder and solder completely cover the welding position of the pad and lead, and the component height is moderate;
(3) Good wettability; The edge of the welding point should be thin, and the wetting angle between the solder and the pad surface should be below 300, and the maximum should not exceed 600
SMT processing appearance inspection content:
(1) Whether the components are missing;
(2) Whether the components are pasted incorrectly;
(3) Whether there is short circuit;
(4) Whether there is faulty welding; The causes of faulty soldering are relatively complex.
1、 Judgment of faulty welding
1. Use special equipment for online tester for inspection.
2. Visual or AOI inspection. When it is found that there is too little solder at the solder joint and the solder is not well soaked, or there is a broken seam in the middle of the solder joint, or the solder surface is convex spherical, or the solder and SMD are not compatible, attention should be paid to it. Even minor phenomena can cause hidden dangers, and it should be immediately judged whether there is a problem of batch solder failure. The judgment method is: check whether there are problems with solder joints at the same position on many PCBs. For example, the problem is only on individual PCBs, which may be caused by solder paste scraping, pin deformation, etc. For example, there are problems at the same position on many PCBs, which may be caused by poor components or problems with pads.
2、 Causes and Solutions of False Welding
1. The pad design is defective. The existence of through-hole in the pad is a major defect in PCB design. If it is not enough, do not use it. The through-hole will cause solder loss and lead to insufficient solder; The pad spacing and area also need standard matching, otherwise the design should be corrected as soon as possible.
2. PCBA board is oxidized, that is, the welding pad is black and not bright. In case of oxidation, the oxide layer can be removed with an eraser to make it shine again. PCB board is affected with moisture, if suspected, it can be dried in the drying oven. PCB board is polluted by oil stain, sweat stain, etc., and then it should be cleaned with absolute ethanol.
3. For PCB printed with solder paste, the solder paste is scraped and rubbed, which reduces the amount of solder paste on the related pad and makes the solder insufficient. It shall be supplemented in time. The filling method can be used with a dispenser or a bamboo stick.
4. SMD (surface mounted components) has poor quality, expired, oxidized and deformed, resulting in faulty soldering. This is a common reason.
(1) Oxidized components are dark and not bright. The melting point of the oxide rises. At this time, it can be welded with 300 degree ferrochrome and rosin type flux, but it is difficult to melt with 200 degree SMT reflow and less corrosive non cleaning solder paste. Therefore, oxidized SMD should not be welded in reflow welding furnace. When buying components, be sure to check whether there is oxidation, and use them in time after purchase. Similarly, oxidized solder paste cannot be used.
(2) The surface mounted components of multiple legs are small and easy to deform under the action of external forces. Once deformed, false welding or lack of welding will certainly occur. Therefore, careful inspection and timely repair shall be carried out before and after welding.