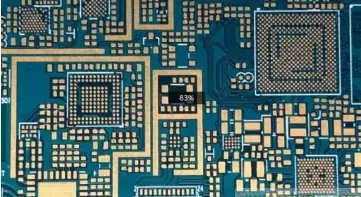
Solution to the bad phenomenon of PCBA processing and welding
In the welding process of PCBA processing, due to poor operation of workers or poor solder selection. As a result, the welding effect cannot meet the expectation. What are the bad phenomena of PCBA processing and welding? What faults will be caused by poor soldering? The following describes the defective solder joints and their causes.
In the welding process of PCBA processing, due to poor operation of workers or poor solder selection. As a result, the welding effect cannot meet the expectation. What are the bad phenomena of PCBA processing and welding? What faults will be caused by poor soldering? The following describes the defective solder joints and their causes.
(1) Solder pad peeling: It is mainly because the solder pad is peeLED off from the printed circuit board after being subjected to high temperature, and the defective solder joint is very easy to cause the fault of component open circuit.
(2) Solder distribution asymmetry: mainly due to poor quality of flux or solder, or insuffICient heating. The strength of the poor solder joint is not enough, and it is very easy to cause the fault of open circuit of components under the action of external force.
(3) Whitening of solder joints: uneven and dull. Generally, it is caused by too high temperature of electric soldering iron or too long heating time. The strength of the poor solder joint is not enough, and it is very easy to cause the fault of open circuit of components under the action of external force.
(4) Sharpening: The main reason is that the electric soldering iron is withdrawn in the wrong direction, or the flux is sublimated due to excessive temperature. This poor solder joint will cause short circuit between components and wires.
(5) Cold welding: the surface of the welding spot is in the shape of tofu dregs. It is mainly because the temperature of the electric soldering iron is not enough, or the weldment shakes before the solder solidifies. The poor solder joint has low strength and weak conductivity, and it is very easy to cause the component open circuit fault under the action of external force.
(6) There are cavities in the solder joint: the main reason is that the lead wire is poorly soaked, or the gap between the lead wire and the jack is too large. The poor solder joint can be connected temporarily, but the components are prone to open circuit failure after a long time.
What are the undesirable phenomena of PCBA processing and welding? Cause analysis
(7) Excessive solder: mainly caused by untimely removal of welding wire.
(8) Too little solder: it is mainly caused by the premature removal of the welding wire. The poor solder joint is not strong enough, and its conductivity is weak. It is easy to cause the open circuit fault of components under the action of external forces.
(9) Loose lead and movable weldment: it is mainly caused by the lead moving before the solder solidifies, or the lead flux is not well soaked. The poor solder joint is very easy to cause the component not to be conductive.
(10) Welding spot mixed with rosin slag: mainly due to excessive flux or insufficient heating. The poor solder joint has low strength and unstable conductivity.
(11) False soldering: the main reason is that the surface of the weldment is not clean, or the flux is poor, or the heating is insufficient. The strength of the bad solder joint is not high, which will make the continuity of the components unstable.
(12) Holes on the surface of the solder joint: mainly due to the excessive gap between the lead and the jack. The strength of the bad solder joint is not high, and the solder joint is easy to be corroded.
In PCBA processing, poor welding materials, selection of welding temperature and length of welding time can affect the final quality of welding.