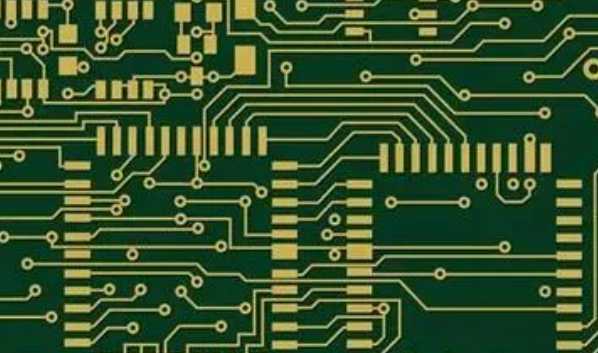
Another important consideration when designing rigid-flexible PCB is hole size and ring. The hole size must be considered, as smaller holes are not sufficient to accommodate dowel pins during assembly. Thus, the optimal hole size for rigid-flexible combined PCBS is 0.040 inches, while the optimal hole size for annular rings is 0.015 inches.
Weld resistance gap
The solder stop gap is the space between the copper trace and the solder stop. This space is important to ensure sufficient space for solder flow during rigid-flexible PCB assembly and to prevent short circuits between wires.
The width of the solder stop gap depends on the width of the wire, the thickness of the solder stop layer and the thickness of the copper. The clearance should be at least 0.007 "for narrow routes and at least 0.010" for wide routes.
Screen clearance
The silkscreen gap is simply the small amount of space between the edge of the printing surface and the beginning of the design. This gap ensures that the design will be printed in the correct position on the flexible circuit, no matter how thin or fine the circuit is. In most cases, a screen clearance of 0.010 inches is sufficient to ensure accurate printing.
Management heat dissipation problem
Thermal management is a key consideration in the design of any electronic device, but it is particularly important in the case of flexible and rigid-flexible PCBS. When designing flexible or rigid-flexible PCBS, many factors must be considered, including the thermal characteristics of the material used, the effect of thermal expansion on the board, and whether adequate cooling is required.
With a few simple design considerations, you can help ensure that your rigid-flexible combined PCB does not overheat and cause damage to sensitive components.
Heat through hole
One way to help manage heat buildup on a rigid-flexible PCB is to use a hot through hole. The through-hole is the small hole that connects the different layers of the PCB together. You can help dissipate heat away from key components by placing heat sink holes in strategic locations.
Lightweight material
Another way to manage heat buildup in rigid-flexible PCBS is to use lightweight materials as the substrate. The lighter substrate has less mass, which means it heats up more slowly than the heavier substrate.
radiator
A third way to manage the heat build-up of rigid flexural PCB is to use a radiator. The radiator is a piece of metal that helps to dissipate heat from the PCB. By attaching the radiator to your PCB, you can help keep key components cool.
Thermal tape
The fourth way to manage the heat buildup of rigid-flexible PCB is to use thermal tape. Thermal tape is a special type of tape designed to dissipate heat. These Taopes ensure that the element is kept cool after being placed between the PCB layers.
Last word
To ensure that your rigid-flexible PCB design is manufacturable, it is important to consider DFM and design rules early in the process. By working with a qualified rigid binding PCB manufacturer, you can avoid common problems and get your product to market quickly and efficiently.
Rigid flexible PCB designs can be created using different materials, including FR4 glass epoxy laminate, thermoplastic polyimide (TPU), and FR4 glass epoxy laminate with TPU. The material you choose will depend on your application requirements, but it is vital to ensure that your design is mechanically strong enough to withstand any forces applied during use. To ensure the mechanical stability of your design, you should consider adding overlay material to the top of the copper stitch and solder stop treatment to the top of all exposed copper areas.
Coverlay is a laminated film that is applied to the copper surface of a rigid flexible PCB and then covered with a solder stop layer. This creates an extra layer of protection around the components on top of the flexible PCB. It can also help reduce EMI (electromagnetic interference) by preventing any component from being exposed to air.
The rigid flexible pcb assembly process for applying overlays involves adding solder paste to all pads, placing them in a vacuum chamber, removing excess paste and applying a thin layer of adhesive to each pad. The film is then laminated onto each pad using heat and pressure. The result is an extra layer of protection around the board components while keeping them accessible.
The last word
Although the industry is rapidly evolving from a paper-based design approach to one that relies more heavily on computer aided tools, there are still many nuances to consider when designing rigid flexible PCBS. Fortunately, the benefits of the new PCB technology far outweigh any potential caveats. With some expertise and advanced technical knowledge from Taofang Electronics, you can rest assured that your design will look great.