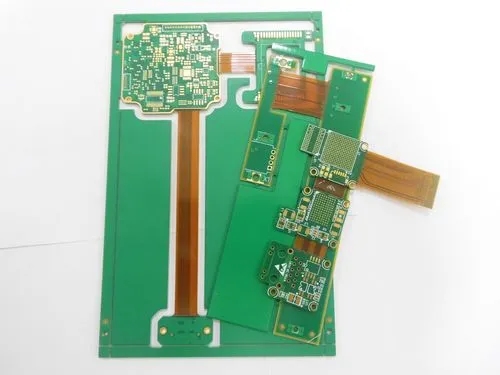
Cause Analysis of Oil Spot Defects on the Surface of Copper Clad Laminates
The oily stain on the surface of CCL is an important defect on the surface of CCL, which is one of the important hidden dangers affecting the use quality of PCB customers. Based on the understanding of the oily stain defect on the surface of CCL, this paper discusses the formation of this defect from the formation mechanism and process, and discusses the solution.
1 Preface
Copper clad laminate (CCL) is composed of base plate, copper foil and adhesive, and the base plate is an insulating laminate composed of polymer synthetic resin and reinforcement materials; The surface of the substrate is covered with a layer of pure copper foil with high conductivity and good weldability. Copper clad laminate is one of the basic materials of printed circuit board. The quality of CCL has a significant impact on the use of printed boards. The performance requirements of printed boards on CCL mainly come from the processing performance requirements of printed circuit boards, the performance requirements of component installation, and the performance requirements of complete product operation. It can be said that the performance of CCL has a very important impact on PCB. The properties of CCL include apparent quality, heat resistance, warping, thermal conductivity, environmental characteristics, etc. The most basic is the apparent quality of CCL. The apparent quality will affect the qualification rate, open circuit, short circuit, etc. of printed boards. For example, the adhesive trace on the surface of copper clad laminate will affect the endless etching and short circuit of printed boards; The concave point will affect the open circuit of the printed board.
Recently, we found a rare defect on the surface of the copper clad plate, which shows a dotted impression on the surface of the copper clad plate. The existence of this defect will not only increase the extra labor required by the production personnel to eliminate this defect, but also affect the use quality of the printed board. The existence of this defect is a very interesting thing. Here, the formation mechanism and process of this defect are discussed.
Discussion on the Formation of Surface Defects of CCL
2.1 What is the defect
The surface of the copper clad plate is suspected of oil spot defect, which is very rare at ordinary times. This defect exists on the copper foil surface of the copper clad plate. This defect appears as a suspected oil spot on the copper foil surface by visual inspection. This defect is observed with a 10x magnifying glass. The defect is irregular, similar to the mark of a watermark. The color of this mark is different from that of the copper foil.
According to the observation of the character of the defect, it is initially suspected that it is an oil spot, but it is really not very clear what the oil spot is. Therefore, some experiments are designed to confirm this defective material. We use adhesive tape to fix the various areas distributed by the copper clad laminate with oil absorbing face paper, and let it stand for 15 minutes to collect the substances suspected of oil spots. After standing for 15 minutes, the same substance as the defect suspected of oil stain on the surface of the CCL can be collected on the oil absorbing paper, as shown in the following figure. The collected suspected oil spot substances are tested for elements. Because it is difficult to test, the suspected oil spot substances cannot be identified in this way.
We can basically confirm that the substance suspected of oil spot is indeed an oil spot, and this oil spot is the heat transfer oil used for heating the laminating machine, only by analyzing the properties with the maintenance personnel and checking the production site.
2.2 Test process
Heat transfer oil is a kind of special oil with good thermal stability for indirect heat transfer. It has the advantages of uniform heating, accurate temperature regulation and control, and good heat transfer effect. The heat transfer oil we use is mainly used to transfer heat for the laminator and heat the copper clad plate. It is only used for the laminator. Why it is transferred to the surface of the copper clad plate to form defects is really a very doubtful problem.
The copper clad plate shall be distributed after being laminated. The oil spot defects on the surface of the CCL can be found after the distribution of the CCL, that is, when the plate is placed in the distribution hall for a period of time, a small amount of oil spot defects can be seen on the surface of the CCL. We can know where the oil spots will appear by placing oil absorbent paper in the distribution lobby and near the press. The test found that oil spots can be collected near the distribution hall and the laminator.
Through analysis, oil spots causing oil spot defects on the surface of CCL can be found near the laminator and in the distribution hall, indicating that oil spots will appear in the whole area. After analyzing the air flow of the laminator and the distribution hall, it is found that the air flow in the whole area of the laminator and the distribution hall actually forms a simple return area, as shown in the figure below. This may explain why oil spots occur in these areas.
Static electricity is everywhere, and there will be some static electricity more or less on our production site. Why does the oil spot fall on the surface of CCL? Whether it is related to static electricity. Here, we design some experiments to analyze this problem.
Near the laminator, we placed two pieces of copper foils, and placed insulating materials under the copper foils. Through friction, the copper foils were charged with static electricity of about+0.05 kV and+0.33 kV, respectively, and kept still for 15 minutes. The experimental results show that the number of oil spots adsorbed by copper foil with static electricity of about+0.33 kV is a little more than that of copper foil with static electricity of+0.05 kV. This test shows that static electricity has certain influence on oil point.
2.3 Discussion on defect formation mechanism and process
The oil spot defect on the surface of CCL is actually a defect formed by the adhesion of the heat transfer oil of the laminator to the surface of CCL. How the heat transfer oil adheres to the surface of the copper clad laminate, through the previous experiments, a preliminary conclusion is formed for discussion.
Generally, the spray atomization process of liquid mist can be divided into three stages: the first stage is that the liquid flows in the nozzle; Second, the liquid column splits into droplets after being ejected; The third stage is the further fragmentation of fog droplets in the gas [1]. The volume of heat transfer oil expands significantly after being heated. When the heat transfer oil pipeline of the laminating machine leaks slightly, the heat transfer oil expands due to the effect of temperature, causing the heat transfer oil to leak out from the leakage port. This slow leaking process can be likened to a process of nozzle spraying. That is, after the heat transfer oil seeps out of the leakage port, it forms an atomized state. The physical essence of liquid atomization is: under the effect of external energy, the fuel oil is first expanded into a very thin liquid film or a very thin jet, and then the liquid film or jet is destabilized by various disturbances, or due to the action of power in motion, and then broken into filaments and large droplets, and finally into small droplets [2]. The small oil droplets formed by atomization will penetrate into all corners of the laminator and distribution area under the effect of the return air flow in the laminator and distribution area. As the atomized oil mist will carry some charges on the surface, the atomized oil mist will be viscous on the surface of the CCL through the effect of free fall and anisotropic absorption, thus forming oil spot defects on the surface of the CCL. We can describe the formation mechanism and process of oil spot defects on the surface of CCL through a model diagram.
Reasoning from the formation mechanism and formation process of the oil spot defect on the surface of the copper clad laminate, we searched for the source of the oil mist formed by the heat transfer oil, and found that hot oil seeped from the connection part between the top of the hot oil valve body of the laminating machine and the electric control head. The heating effect of the valve body was that the hot oil seeped into the surrounding environment in the form of gas, resulting in the generation of oil mist. By replacing the components of the leakage part, the formation of oil mist can be eliminated, and the occurrence of oil spot defects on the surface of CCL can be solved.
3 Conclusion
The surface oil spot defect of copper clad laminate is a rare defect. This paper studies the formation mechanism and process of oil spot defect on the surface of copper clad laminate through the atomization of heat transfer oil, airflow direction and electrostatic effect. It provides a good way to solve the apparent oil spot defects of copper clad laminate and composite materials.