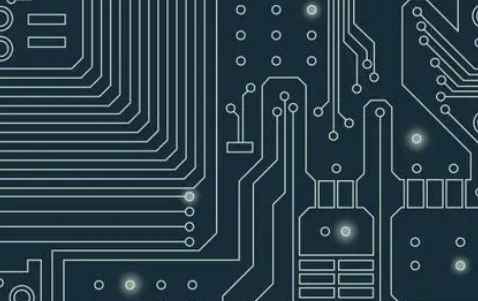
Rigid and flexible printed circuit boards (PCBS) are becoming increasingly popular in various industries, from consumer electronics to aerospace and defense. While flexible PCBS have been around for years, adding rigid components to the mix opens up a whole new world of design possibilities.
However, designing and manufacturing rigid-flexible PCBS is not without challenges. In this blog post, we will look at some of the key design and manufacturing considerations for rigid-flexible PCBS, including:
Design for Manufacturability (DFM)
Ensure compliance with design rules
Management heat dissipation problem
We will also provide tips on overcoming some of the challenges associated with rigid-flexible PCB design and manufacturing.
Design of Rigid Flexible PCB for Manufacturability (DFM)
One of the most important considerations when designing rigid-flexible PCB is manufacturability. Due to the unique structure of the rigid and flexible PCB, several challenges had to be considered during the design process.
Some of the key challenges associated with the manufacturability of rigidly flexible bonded PCBS include:
Ensure proper registration between rigid and flexible layers
Avoid gaps in solder joints
Minimizing warping and bending
Let's take a closer look at each of these challenges.
Ensure proper registration between rigid and flexible layers
One of the most important aspects of rigid-flexible PCB design is to ensure the correct registration between rigid and flexible layers. This can be a challenge because the two layers need to be perfectly aligned to avoid problems during assembly.
The most popular way to ensure proper registration between rigid and flexible layers is to use alignment holes. Alignment holes are small openings on the PCB that allow alignment pins to be inserted during assembly. This ensures that the rigid and flexible layers are properly aligned before welding.
Another way to ensure proper registration is to use benchmarks. The benchmark is a small circular feature usually placed in the corner of the PCB. They can be used for alignment during assembly, but also for calibration during automatic optical inspection (AOI).
Avoid gaps in solder joints
Another challenge associated with rigid-flexible PCB design is avoiding holes in the solder joints. This can be a problem when using lead-free solders, as they tend to have lower melting temperatures and tend to form voids more easily.
There are several different ways to avoid holes in the solder joint. The most common method is to use staggered holes. Staggered through holes are small holes offset from each other. This helps distribute heat evenly and prevents voids from forming in the solder joint.
In addition, a copper column can be used to avoid holes in the solder joint. Copper posts are small copper posts placed around the perimeter of the PCB. They help to conduct heat away from the solder joint and prevent voids from forming.
Use rigid-flexible PCB to minimize warping and bending
Another challenge when designing rigid-flexible PCBS is to minimize warping and bending. With larger boards, this can be a problem because they are more likely to warp during assembly.
There is more than one way to minimize warping and bending. The most commonly used, however, are stiffeners. Stiffeners are small pieces of material placed on the bottom of the PCB. They help support the board and prevent it from warping during assembly.
Another way to reduce warping and bending is to use copper filler. Copper fill is a technique that involves filling unused areas of a PCB with copper. This helps increase the board's stiffness and prevents it from warping during assembly.
Ensure that rigid and flexible PCB design rules are met
Another important consideration when designing a rigid-flexible PCB is to ensure compliance with design rules. This is important because rigid-flexible PCBS have different design rules than traditional PCBS.
Some key considerations when designing a rigid-flexible PCB include:
Cable width and spacing
Aperture and ring
Solder resistance clearance Z
Silk screen clearance
Let's discuss these considerations in detail:
Cable width and spacing
One of the key considerations in designing rigid-flexible PCB is the width and spacing of the wires. This is important because the wiring needs to withstand the mechanical stress of bending during assembly. The recommended cable width of rigid-flexible PCB is 6 mil. The recommended distance between cables is 10 mil.
Aperture and ring