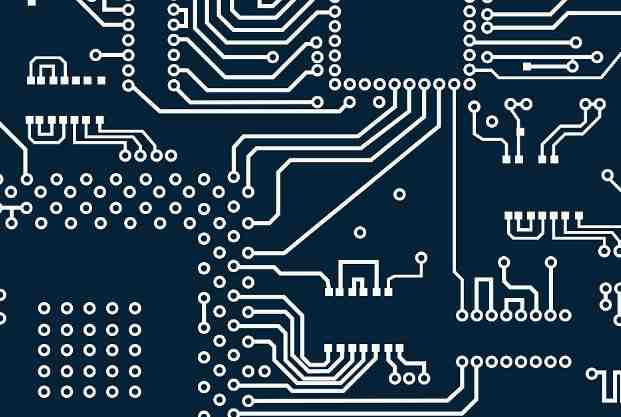
When printing, a 60-degree metal scraper made of stainless steel is usually used. The printing pressure control is in the range of 3.5KG-10KG. Too much pressure and too little pressure are bad for printing. The printing speed is controlled between 10MM/ sec-25mm /SEC, and the smaller the pin spacing of the components, the slower the printing speed. The release speed after printing is generally set between 1MM/SEC, if it is a u BGA or CSP device, the release speed should be slower about 0.5MM/SEC. In addition, in the printing welding should pay attention to the control of the operating environment. The working field temperature is controlled at about 250C, and the temperature is controlled at about 55%RH. The printed PCB should be reflow welded within half an hour to prevent the solder paste from being exposed in the air for too long and affecting the quality.
Placement Of SMT Processing Devices
The accurate placement of BGA largely depends on the accuracy of the mounter and the recognition capability of the image recognition system. As far as the various brands of multifunctional mounters on the market are concerned, the mounter that can place BGA has an accuracy of about 0.001MM, so there will be no problem in the accuracy of the mounter. As long as the BGA device is recognized by the image, it can be accurately placed on the printed circuit board.
However, sometimes the BGA identified by the image is not a 100% good ball device, and it is possible that one ball is slightly smaller in the Z direction than other balls. In order to ensure the good welding, we can usually subtract 1-2MM from the thickness of the BGA device, and at the same time close the vacuum system with the extension for about 400 milliseconds, so that the BGA device can fully contact the welding ball with the solder paste when placed. In this way, the phenomenon of empty welding of one of the BGA pins can be reduced.
However, for uBGA and CSP devices, we do not recommend using the described method to prevent the occurrence of poor welding phenomena.
Reflow Welding
Reflow welding is the most difficult step to control during BGA assembly. Therefore, to obtain a better return air line is the key to obtain good BGA welding.
★ Preheating Stage
During this period of time, the PCB is uniformly heated and the flux is stimulated. Generally, the heating speed should not be too fast to prevent the arc of the line from being heated too fast and resulting in large deformation. We try to control the temperature rise below 30C/SEC, and the ideal temperature rise rate is 20C/SEC. Keep the time between 60 and 90 seconds.
★ Infiltration Stage
At this stage, the flux begins to evaporate. The temperature should be maintained between 1500C-1800C for 60-120 seconds so that the flux can fully play its role. The rate of warming is generally 0.3-0.50C/SEC.
★ Reflux Stage
The temperature at this stage has exceeded the melting point temperature of the solder paste, the solder paste melts into a liquid, and the component pin is tin. The time when the temperature is above 1830C in this stage should be controlled between 60-90 seconds. If the time is too little or too long will cause welding quality problems. Among them, the temperature in the range of 210-2200C time control is quite critical, generally controlled in 10-20 seconds is the best.
★ Cooling Stage
At this stage, the solder paste begins to solidify, and the components are fixed on the circuit board. Similarly, the speed of cooling can not be too fast, generally controlled below 40C/SEC, and the ideal cooling speed is 30C/SEC. Because too fast cooling speed will cause cold deformation of the circuit board, it will cause quality problems of BGA welding, especially the virtual welding of the BGA outer ring pin.
When measuring the temperature curve of reflow welding, the measuring point of the BGA component should be between the BGA pin and the circuit board. BGA should try not to use high temperature tape, but use high temperature solder welding and thermocouple phase fixation to ensure that more accurate curve data can be obtained.
The basis of efficient and low-cost assembly production is to select the appropriate assembly method according to the specific requirements of the assembly product and the conditions of the assembly equipment, and it is also the main content of the SMT processing process design. The so-called surface assembly technology refers to the assembly technology of electronic parts with certain functions by placing sheet-like structure components or miniaturized components suitable for surface assembly on the surface of the printed board in accordance with the requirements of the circuit and assembling them with welding processes such as reflow welding or wave soldering.
What Are The Assembly Methods Of SMT Chip Processing?
On traditional THT printed circuit boards, the components and solder joints are located on two sides of the board, while on SMT printed circuit boards, the solder joints and components are on the same side of the board. Therefore, on the SMT printed circuit board, the through hole is only used to connect the wires on both sides of the circuit board, the number of holes is much less, and the diameter of the holes is much smaller, so that the assembly density of the circuit board can be greatly improved. The following is an introduction to the assembly method of SMT patch processing technology organized by Changkeshun SMT patch processing factory.
SMT Single-Side Mixed Assembly Method
The first type is single-sided hybrid assembly, that is, SMC/SMD and through-hole cartridge components (17HC) are distributed on different sides of the PCB mixed, but the welding surface is only single-sided. This type of assembly method adopts single-sided PCB and wave soldering (now generally adopts double wave soldering) process, and there are two specific assembly methods.
First paste method.
The first assembly method is called the first pasting method, that is, the SMC/SMD is first pasted on the B side of the PCB (welded surface), and then the THC is inserted on the A side.
Post-paste method.
The second assembly method is called the post-paste method, which is to insert THC on the A-side of the PCB first, and then mount SMD on the B-side.
SMT double-sided hybrid assembly method
The second type is double-sided hybrid assembly, SMC/SMD and T.C can be mixed on the same side of the PCB, at the same time, SMC/SMD can also be distributed in. Both sides of the PCB. Double-sided hybrid assembly with double-sided PCB, double wave soldering or reflow welding. In this type of assembly method, there is also the difference between first paste or later paste SMC/SMD, generally according to the type of SMC/SMD and the size of the PCB reasonable choice, usually using the first paste method more. Two assembly methods are commonly used for this type of assembly.
SMC/SMD and 'FHC' are on the same side, SMC/SMD and THC are on the same side. One side of the PCB.
SMC/SMD and iFHC have different side ways, placing surface assembly integrated chip (SMIC) and THC on side A of the PCB, and SMC and small profile transistor (SOT) on side B.
This type of assembly method is due to the placement of SMC/SMD on one or both sides of the PCB, and the insertion of lead components that are difficult to surface assembly, so the assembly density is quite high.
The assembly method of SMT patch processing and its process flow mainly depend on the type of surface assembly component (SMA), the type of components used and the conditions of the assembly equipment. In general, SMA can be divided into three types of single-side mixed, double-side mixed and full-surface assembly, a total of 6 assembly methods. Different types of SMA have different assembly methods, and the same type of SMA can also have different assembly methods.