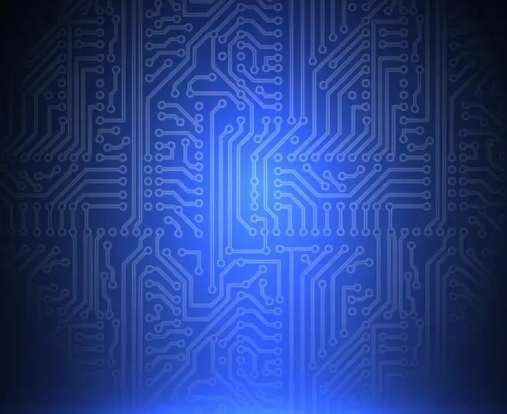
PCB line open, short circuit is the PCB manufacturers almost every day will encounter the problem, has been plagued by production, quality management personnel, it caused by insufficient shipment and replenishment, delivery delays, customer complaints are more difficult to solve the problem. Kingford has accumulated some experience in the improvement of PCB opening and short circuit problems, and now forms a text to summarize, for the PCB manufacturing discussion of peers, and looks forward to the management of production and quality of peers can be used as a reference.
The Reasons For The Above Phenomenon And The Methods For Improvement Are Listed As Follows
First, open circuit caused by exposing the substrate.
1. There are scratches before the copper clad plate enters the warehouse.
2. The copper clad plate is scratched during the opening process.
3. The copper clad plate is scratched by the drill during drilling.
4. The copper clad plate is scratched during the transfer process.
5. When stacking plates after copper sinking, the surface copper foil is damaged due to improper operation.
6. The copper foil on the surface of the production plate is scratched when it passes the horizontal machine.
Improvement method:
1. The copper clad plate in the warehouse before IQC must be random inspection, check whether the surface of the board scratches the substrate phenomenon, if there should be timely contact with the supplier, according to the actual situation, make appropriate treatment.
2. The copper clad plate is scratched during the opening process, the main reason is that there are hard objects on the surface of the opening machine, and the friction between the copper clad plate and the objects causes the copper foil scratch to form the phenomenon of exposing the substrate, so the table must be carefully cleaned before the opening of the material to ensure that the table is smooth and there is no hard objects.
3. The copper clad plate is scratched by the drill when drilling, the main reason is that the spindle clip is worn, or the debris in the clip is not clean, the PCB proofing grasp the drill is not strong, the drill does not go to the top, the length of the drill is slightly longer than the set, the height of the drilling is not enough, the drill tip scratches the copper foil to form the phenomenon of exposure to the substrate when the machine tool moves.
a. The clip can be replaced by the number of times recorded by the knife or according to the wear degree of the clip.
b. Clean the clip regularly according to the operating rules to ensure that there is no debris in the clip.
4. The Plate is Scratched During the Transfer Process:
a. The handling personnel lift the amount of the board at one time is too much, the weight is too large, the board is not lifted during handling, but dragged along the trend, resulting in friction between the board Angle and the board surface and scratch the board surface;
b. When the board is put down, it is not put neatly, and it is forced to push the board in order to re-arrange it, causing friction between the board and the board to scratch the surface of the board.
5. After copper sinking, the whole board after electroplating when stacking the board due to improper operation was scratched:
When storing the board after copper deposition and full board electroplating, because the board is stacked together, when there is a certain amount, the weight is not small, and then put down, the board Angle is downward and there is a gravitational acceleration, forming a strong impact impact on the board surface, causing the board surface to scratch the substrate.
6. The production board is scratched in the horizontal machine:
a. The baffle plate of the grinding machine sometimes contacts the surface of the plate, the edge of the baffle is generally uneven and the advantages are raised, and the surface of the plate is scratched when the board is passed;
b. Stainless steel drive shaft, due to damage into a pointed object, when the plate scratches the copper surface and exposed the base material.
There are several ways to eliminate crosstalk in PCB design:
1. The size of both kinds of crosstalk increases with the increase of load impedance, so the signal line that is sensitive to interference caused by crosstalk should be properly terminated.
2. As far as possible to increase the distance between the signal lines, can effectively reduce the tolerance of crosstalk. Ground management, spacing between the wiring (e.g. isolating the active signal line from the ground, especially between the signal line and the ground where the state has changed) and reducing lead inductance.
3. The insertion of a ground wire between the adjacent signal lines can also effectively reduce the capacitive crosstalk, this ground wire needs to be connected to the formation every 1/4 wavelength.
4. For inductive crosstalk, the loop area should be minimized, and if allowed, the loop should be eliminated.
5. Avoid signal sharing loop.
6. Focus on signal integrity: the designer should realize the end connection in the welding process to solve the signal integrity. Designers using this approach can focus on masking the microstrip length of the copper foil in order to obtain good performance for signal integrity. For systems that use dense connectors in the communication structure, the designer can use a PCB as the termination.
Fourth, electromagnetic interference
With the increase of speed, EMI will become more and more serious, and in many aspects (such as electromagnetic interference at the interconnect), high-speed devices are particularly sensitive to this, it will receive high-speed false signals, and low-speed devices will ignore such false signals.
There are several ways to eliminate electromagnetic interference in PCB design:
1. Reduce the loop: Each loop is equivalent to an antenna, so we need to minimize the number of loops, the area of the loop and the antenna effect of the loop. Ensure that the signal has only one loop path at any two points, avoid artificial loops, and try to use the power layer.
2. Filtering: on the power line and on the signal line can be taken to reduce EMI filtering, there are three methods: decoupling capacitor, EMI filter, magnetic components.
3. Shield. Due to the problem of space and the discussion of the shield of many articles, no more specific introduction.
4. Try to reduce the speed of high-frequency devices.
5. Increase the dielectric constant of the PCB board, which can prevent the high-frequency part such as the transmission line near the board from radiating outward; Increasing the thickness of the PCB board and minimizing the thickness of the microstrip line can prevent the leakage of the electromagnetic line and also prevent radiation
Discussing this, we can summarize that in high-frequency PCB design, we should follow the following principles:
1. Power and ground unity, stability.
2. Carefully considered wiring and appropriate termination can eliminate reflection.
3. Carefully considered wiring and appropriate termination can reduce capacitive and inductive crosstalk.
4. Need to suppress noise to meet EMC requirements.