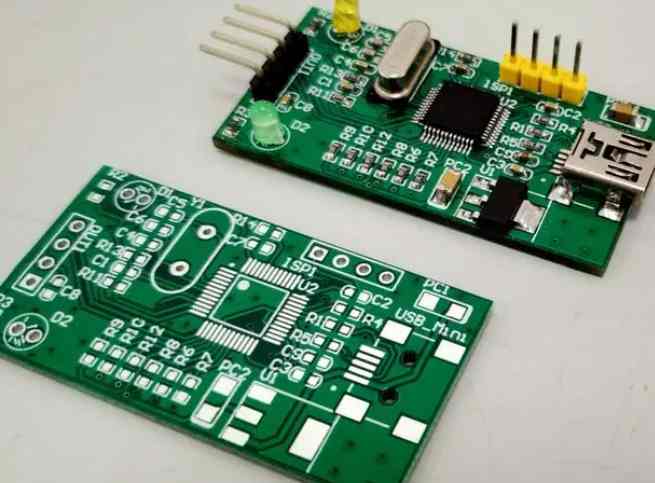
I. Definition of SMT OEM
SMT foundry refers to the process of manufacturing printed circuits (PCB) on PCB boards, replacing traditional manual welding with a high degree of automation. SMT outsourcing involves placing PCB components on the PCB board, usually using a pick and place machine or sync placement. It attaches components to the circuit board and, according to customer requirements, performs thermal curing, which is the process of attaching components to the circuit board, which ultimately inspects and completes the entire manufacturing process.
Two, SMT OEM advantages and disadvantages
1. Advantages: SMT OEM can improve productivity, automate welding process, reduce manual operation and improve production efficiency; SMT foundry can make components on PCB board have smaller size, can achieve smaller volume and lower weight; The SMT OEM manufacturing process can better control the matching and quality of PCB board components, to ensure the high quality, stability and reliability of output products.
2. Disadvantages: SMT OEM equipment is relatively expensive and the initial investment is large; SMT OEM needs to invest a lot of time, expense and manpower to complete, which will cause great cost pressure. SMT OEM process is prone to component installation dislocation, filling funnel, and easy to be affected by external interference, such as temperature and humidity changes, will affect the installation and fixing of components.
Third, SMT OEM process
1. Receiving goods: Collect PCB boards and components provided by customers, confirm process documents, and conduct preliminary inspection.
2. Pre-treatment: layout PCB board, cleaning PCB board, cleaning pad, pre-polishing treatment, and pre-welding treatment.
3. SMT placement: Use automatic placement machine to mount components on PCB board, and carry out hot curing according to customer requirements.
4. Test: After SMT mounting, test is needed to confirm whether the installation position of components is correct and whether the PCB board works normally.
5, cleaning: remove the dust and residue on the board, to ensure the quality of mounting components.
6. Packaging: The PCB board completed by SMT OEM will be packaged and ready for delivery.
4. Technical difficulties in SMT OEM process
1. In SMT OEM process, the installation accuracy of component patches is the key to quality control. The installation position of components and the distance between them and PCB board must be controlled to ensure the accurate installation of components.
2. The installation of components is a slow process. Due to the lack of flexibility in the process, it is a technical difficulty to improve the efficiency in the SMT OEM process.
3. Due to the complexity of the mechanical structure and manufacturing process of the SMT machine, high precision is required in the SMT OEM process, so how to ensure the efficiency and accuracy of the SMT machine is a technical difficulty.
4, SMT OEM process needs to use a lot of auxiliary materials, such as tape, hot melt adhesive, adhesive, and the type and quality of these auxiliary materials will also affect the effect of SMT OEM, so how to choose the appropriate auxiliary materials is also a technical difficulty.
V. Quality control of SMT OEM
1. SMT OEM shall be conducted in strict accordance with process documents provided by customers and operating procedures to ensure process control accuracy.
2. Maintain and repair the patch machine regularly to ensure the normal operation and accuracy of the patch machine.
3. Check the installation quality of PCB board regularly to ensure the installation accuracy of components.
4. Check the auxiliary materials used regularly to ensure the quality and compliance with the requirements.
5. Strictly carry out cleaning operations to avoid residual dust on PCB board and ensure product quality.
Vi. Customer service for SMT OEM
1. Provide professional technical consulting services to ensure that customers' requirements can be met.
2. Provide effective quotation service to ensure the maximum benefit of customers' investment.
3. Provide fast delivery service to ensure the timely arrival of customers' products.
4. Provide efficient after-sales service to ensure the smooth use of customers' products.
5. Provide regular quality reports to ensure the quality of customers' products.
2. What is the process of SMT? What are the advantages?
I. Features of SMT patch
1.SMT is characterized by small size, light weight, small area, high durability and strong flexibility, which can meet users' requirements for small structure, space saving, cost reduction, energy saving and emission reduction.
2.SMT has high reliability, which can ensure that the connection between components is firm and reliable, and will not be affected by external extrusion or impact, and will not be affected by the change of ambient temperature, so as to effectively reduce the disconnection between components.
3.SMT is finished by automatic SMT machine, and high-speed SMT can be realized, which can meet the requirements of fast products.
2. SMT patch process
1. Cleaning treatment: The SMT patch process shall be cleaned first to remove dirt and debris on the PCB surface, so as to ensure that there is no pollution on the PCB surface, so as not to affect the quality of the SMT patch.
2. Pre-welding inspection: Before SMT placement, pre-welding inspection should be carried out to check whether the parts on PCB board are installed in accordance with the position required in the drawings and whether there are inserting errors, so as to avoid problems in the subsequent placement.
3. Patch: The next step is the critical patch step, which completes the patch work by attaching the components to the PCB board through the automatic patch machine.
4. Welding: After the patch is completed, it is the welding step to weld the components through hot air welding, so as to ensure the strong connection between the components.
5. Testing: The last step is testing. After testing, if there is no problem, the product can be assembled and packaged.
Three, the advantages of SMT patch
1.SMT patches can save space, reduce costs, save energy and reduce emissions, improve efficiency and reduce ineffective labor, which are the advantages of SMT patches.
2.SMT SMT adopts automatic equipment, which can greatly improve production efficiency, save labor cost, reduce production cost, and greatly improve production quality.
3.SMT adopts automatic SMT machine, which can realize high-speed SMT and meet the requirements of fast products, thus greatly improving the competitiveness of enterprises.
4. SMT has high reliability, which can ensure that the connection between components is firm and reliable, and will not be affected by external extrusion or impact, and will not be affected by the change of ambient temperature, so as to effectively reduce the disconnection between components.