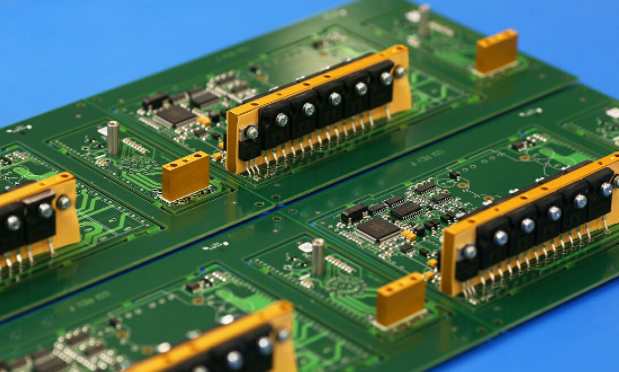
First, SMT proofing technology
SMT proofing technology is a kind of modern electronic manufacturing technology, it refers to the small components and PCB board connection of a fast and precise process, its main characteristics are fast working speed, high precision, low cost, high reliability. The principle of SMT proofing technology is through a special equipment, small components are placed on the PCB board, and then the components into the PCB board, to achieve the connection between components and PCB board.
Two, SMT proofing process
The SMT proofing process mainly includes the following steps: 1. Place the components and PCB board on the SMT mounter; 2, through the placement machine configuration component parameters; 3. The components are heated and fused by the patch machine; 4. After installation, check the installation quality of components; 5. Connect the component with PCB board, and test the PCB board.
3. Advantages of SMT proofing
The advantages of SMT proofing technology are mainly reflected in the following aspects: 1. Reduce the time of the entire production process: SMT proofing technology is highly efficient, which can significantly shorten the production time compared with traditional welding technology; 2. 2, smaller component volume: SMT proofing technology can use smaller components, so as to achieve a smaller volume; 3, higher reliability: SMT proofing technology can better ensure the reliability of components, and can work under lower voltage; 4. Lower cost: SMT proofing technology can use less manpower and material resources, thus reducing production costs.
Four, SMT proofing shortcomings
SMT proofing technology also has some shortcomings, mainly reflected in the following points: 1. Complex equipment: SMT proofing technology requires the use of specialized equipment, and the operation of these equipment is complex, requiring the corresponding technical knowledge; 2. Prone to errors: SMT proofing technology is prone to installation errors, which may cause product quality problems if not corrected in time; 3. High environmental requirements: SMT proofing technology needs to control environmental temperature, humidity, pollution and other factors to ensure quality.
V. Application of SMT proofing
SMT proofing technology has been widely used in the manufacture of electronic products, such as mobile phones, computers, TV sets, etc. In addition, SMT proofing technology can also be used in the manufacturing of household appliances, automotive electronics, medical equipment and other products.
Vi. Development trend of SMT proofing technology
The development trend of SMT proofing technology in the future mainly includes the following points: 1. Smaller component size: More small components will be applied to SMT proofing technology to meet the growing miniaturization demand; 2. 2. Faster technology: constantly improve technology to improve work efficiency; 3, more automation: more application of automation technology, reduce the participation of personnel, improve production efficiency; 4, better reliability: precise control of component installation position, to ensure the reliability of components.
2. What are the technological processes of SMT processing? What processing equipment is available?
First, SMT processing principle:
SMT processing refers to the process of fixing components on the circuit board using electronic assembly technology. It refers to the non-contact fusion welding method, the parts of the welding, pins, chips, etc., installed on the PCB board. The principle is the use of electric heating principle, so that the solder melt into liquid, with metal plate to melt solder, in order to achieve the purpose of fixing components.
Ii. Advantages of SMT processing:
SMT processing technology has good reliability, its technology has good precision, fusion welding contact area is large, fusion welding structure is firm, stable, good heat conduction performance, eliminate high temperature welding thermal damage to components, simple operation, fast cycle, high process efficiency, can efficiently complete batch production, greatly improve the production efficiency, this is its advantage.
Iii. SMT processing process:
SMT process mainly includes board washing, PCB positioning, patch, baking, testing, positioning, printing, gluing, welding, cleaning, testing and so on. Board washing: board washing process is to clean the oil, avalanche glue, residue and so on on the PCB board to ensure the installation quality of components; PCB positioning: Place the PCB board on the positioner of the patch machine to determine its position; Patch: The SMD component is attached to the PCB board, so that it is connected with the PCB board; Baking: Place the replaced PCB board in the baking oven to ensure the contact area and fusion welding effect between components and PCB board; Detection: Check whether the contact area between components and PCB board is normal to ensure the installation quality of components; Positioning: positioning components on PCB board; Printing: apply the printed circuit to the PCB board; Gluing: apply the adhesive to the PCB board; Welding: welding the components to the PCB board; Cleaning: to clean up the residual solder and baking to ensure the normal operation of the circuit; Test: Test whether the components on the PCB board can work normally.
Four, SMT processing quality control:
SMT quality control is to ensure that the quality of products meets the specified standards through various testing techniques in the production process. It mainly includes component detection, welding quality detection, PCB board detection, process parameter detection, assembly quality detection, etc. Component detection: detect the appearance of components, check whether there is pollution, damage, to ensure the quality of components; Welding quality inspection: confirm the quality of welding, check the welding temperature, time, glue amount, etc., to ensure the quality of welding; PCB board inspection: check the surface of the PCB board, check whether there is pollution, damage, to ensure the quality of the PCB board; Process parameter detection: check whether the process parameters meet the standard to ensure the reliability of the process; Assembly quality inspection: Confirm the assembly quality, check whether the assembly meets the requirements, to ensure product quality.
V. SMT processing equipment:
SMT processing equipment mainly includes PCB board washing machine, patch machine, baking machine, testing instrument, positioning machine, printing machine, glue machine, welding machine, cleaning machine, tester and so on. PCB board washing machine: used to clean PCB board, to remove the pollution on PCB board, residue, etc., to ensure the quality of PCB board installation; SMT machine: used to attach SMD components to PCB board, so that the components and PCB board connected; Baking machine: used to place the replaced PCB board in the baking oven to ensure the contact area and fusion welding effect between components and PCB board; Testing instrument: used to test whether the contact area between components and PCB board is normal, so as to ensure the installation quality of components; Positioner: used for positioning components on PCB board; Printing press: used to paint printing circuit onto PCB board; Glue coating machine: used to apply adhesive to PCB board; Welding machine: used to weld components to PCB board; Cleaning machine: used to clean up the residual solder and baking, to ensure the normal operation of the circuit; Tester: Used to test whether the components on the PCB board can work normally.
Vi. SMT processing Safety:
SMT process safety refers to ensuring the safety of employees and equipment in the SMT process to avoid danger or accidental injury. Mainly include operator safety, equipment safety, environmental safety, component safety, etc. Operator safety: To ensure the safety of operators, safety protection measures should be established to avoid accidents; Equipment safety: To ensure the safety of equipment, equipment should be checked regularly to ensure the normal operation of equipment; Environmental safety: To ensure the safety of the working environment, the working environment should be checked regularly.