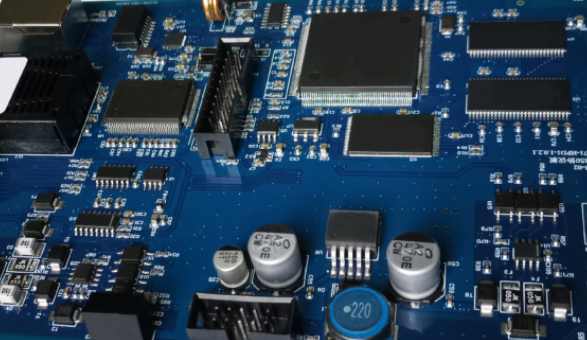
First, the principle of patch proofing
Patch proofing refers to the chip is fixed on the printed circuit board using welding technology, welding the foot on the chip and circuit board line, connect the line, complete the circuit connection, so as to achieve the purpose of proofing a technology. The principle of patch proofing is very simple. First, the chip is removed from the package, and then the chip is fixed on the printed circuit board. Then, the feet on the chip and the circuit board are connected by welding technology.
Patch proofing
Two, patch proofing materials
The required materials for patch proofing are printed circuit boards, chips, solder and welding equipment. The printed circuit board is used to mount the chip, which is the core component of the control circuit, and the solder and welding equipment are the tools used to connect the foot of the chip to the circuit board wiring.
Three, the steps of patch proofing
1. Positioning step: Take the chip out of the package, fix it on the printed circuit board, and connect the foot of the chip to the circuit board.
2. Welding steps: Use welding equipment to connect the foot of the chip to the circuit board. After welding, use a detector to test the sample to ensure the correctness of the patch proofing.
3. Cleaning steps: Clean the finished patch proofing with an automatic cleaning machine to ensure the cleanliness of its surface and remove the welding residue.
Iv. Precautions for patch proofing
1. Position the circuit board accurately to ensure that the chip foot and circuit board line can be effectively connected.
2. Welding should be skilled, and to ensure that the welding connection is firm and clean.
3. Clean the patch proofing thoroughly to ensure its surface cleanliness, otherwise it may affect the quality of the patch proofing.
Five, the advantages of patch proofing
1. The quality of the patch proofing is reliable, which can ensure the effective connection between the chip foot and the circuit board and ensure the normal operation of the circuit.
2. Patch proofing can meet the requirements of various specifications, such as different chip packaging, chip parameters, so as to better meet the needs of customers.
3. Patch proofing can effectively improve production efficiency, reduce production costs and improve the competitiveness of enterprises.
Six, the application of patch proofing
Patch proofing technology is widely used in the production of various electronic products, such as household appliances, automotive electronics, computer peripheral products, mobile phones and so on. Because of the reliable quality of the patch proofing, can effectively reduce the production cost, so it is widely used in the production of various electronic products.
2. How to control the quality management of SMT OEM
I. SMT OEM demand management
SMT OEM demand management is an important part in the SMT OEM service process. From requirement collection, assessment to requirement confirmation, careful screening and detailed analysis are required to ensure that customer requirements are met. In the process of demand management, it is necessary to grasp the actual needs of customers, deeply understand the needs of customers, timely communication and negotiation, timely capture the needs of customers to ensure the accuracy and integrity of the needs, and jointly determine the details of the needs with customers, so as to better meet the needs of customers.
Two, SMT OEM technology
SMT OEM technology is the key of SMT OEM service and the key to guarantee the effect of SMT OEM. SMT foundry technology requires high precision, high speed, high efficiency, high reliability as the principle, through the correct process flow, efficient production process, to ensure and improve the quality of SMT foundry. SMT foundry technology requires a high level of equipment, process, technology and management.
Third, SMT OEM quality control
SMT OEM quality control is the core of SMT OEM service and the key to guarantee the quality of SMT OEM. SMT OEM quality control needs to be managed from product design, material technology, process flow, production process, assembly process, detection and other aspects to ensure the quality of SMT OEM. Through perfect quality control process, timely find and solve quality problems, to ensure the stability and reliability of SMT OEM quality.
Iv. SMT OEM process research and development
SMT OEM process research and development is the key to improve the quality of SMT OEM, but also an important means to promote the progress of SMT OEM. Requirements based on customer demand, high precision, high speed, high efficiency, high reliability as the principle, continuous improvement and perfection of SMT OEM process, improve the quality and efficiency of SMT OEM, to meet customer needs.
V. SMT OEM service tracking
SMT OEM service tracking is an important part of SMT OEM service and the key to guarantee the quality of service. SMT OEM service tracking requires timely discovery and solution of customers' problems in SMT OEM service, and timely feedback of customers to ensure customer satisfaction.
Vi. SMT OEM financial management
SMT OEM financial management is the key to ensure SMT OEM service quality and an important means to ensure service efficiency. SMT OEM financial management requires full analysis of the revenue and expenditure of SMT OEM services to ensure financial stability, and timely adjustment of financial strategies to ensure the quality and efficiency of SMT OEM services.