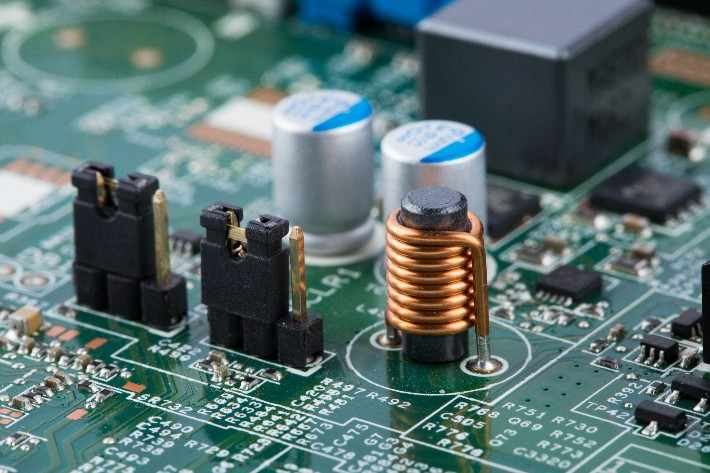
LTCC substrate circuit overview
Low temperature co-fired ceramics (LTCC) is a multi-layer ceramic manufacturing technology that integrates interconnection, componentless and encapsulation. With the continuous progress of technology, the appearance of electronic products can become smaller and thinner, but more powerful. Take the wireless industry of mobile phones, for example. The size of mobile phones has shrunk. Early mobile phones started as simple audio data transmission functions, and now they have evolved into handheld network computers. If some passive components can be integrated into the substrate, it will not only benefit the miniaturization of the system, increase the assembly density of the circuit, but also improve the reliability of the system. The current integrated packaging technology mainly includes thin film technology, silicon chip semiconductor technology, multilayer circuit board technology and LTCC technology. LTCC technology is a low-cost packaged solution with a short development cycle. Low temperature co-fired ceramic technology can meet the needs of light, thin, short and small. But the low temperature co-fired ceramic substrate has the characteristics of high hardness and fragile. Therefore, when the cutting machine cuts the hard substrate, there will be greater friction between the substrate and the cutting blade, and the stress generated by friction will be transferred to the cutting blade.
2. LTCC substrate processing technology
The manufacturing process of LTCC substrate mainly includes mixing, casting, punching, filling, screen printing, laminating, isostatic pressing, and glue discharge and sintering, etc. The main processes of each process are briefly introduced below.
Mixing and casting: Organic matter (consisting mainly of a polymer binder and a plasticizer dissolved in solution) and inorganic matter (consisting of ceramic and glass) are mixed in proportion, homogenized by ball milling, then poured on a moving carrier (usually polyester film), passed through a drying zone, all solvents removed, and cast to the desired thickness by controlling blade clearance. The general thickness tolerance for this process is ±6%.
Punching: Using mechanical punching, drilling or laser drilling technology to form through holes. A through hole is a small hole (usually 0.1-0.2mm in diameter) punched out of a raw tile for interconnecting circuits between different layers. At this stage also punching die holes, to help stack when aligned; Alignment holes are used for automatic alignment of printed conductors and media.
Printing: Printing and drying of conductor paste using standard thick film printing techniques. The through-hole filling and conductor pattern are dried in the box or chain furnace according to the relevant process temperature and time. All resistors, capacitors and inductors are printed and dried at this stage as required.
Through hole filling: Using traditional thick film screen printing or stencil extrusion, special conductor paste with high solid particle content is filled through holes.
Expelling and sintering: The area between 200 and 500°C is called the organic expelling zone (it is recommended that the area be insulated in layers for at least 60 minutes). The layers are then co-fired to a peak temperature (usually 850°C) for 5-15 minutes. Typical stripping and firing curves for metallization take 2-10h. The fired parts are prepared by a firing process, such as printing conductors and precision resistors on the top surface, and then fired in the air. If Cu is used for metallization, it must be sintered in an N2 chain furnace.
Inspection: The line is then laser damped (if required), tested, sliced and inspected, brazed leads or heat sinks are available in the LTCC package (if required).
3. LTCC substrate circuit processing cases
(1) LTCC substrate microporous formation technology
The formation of microholes is a very key technology in the high density interconnection of low-temperature co-fired ceramic multilayer substrate, because the size of aperture and position accuracy will directly affect the wiring density and substrate quality. To achieve ultra-high density, the through-hole aperture should be less than 100μm. LTCC raw porcelain belt microhole production methods are: mechanical punching and laser punching.
Mechanical punching
Nc punch is a better way to punch porcelain belt, especially for shaping products, punching has more advantages. Thousands of holes can be washed out at a time with a punch mold, with a minimum diameter of 50μm. Fast punching speed, high precision, suitable for mass production. A punch of the same size as the microhole and a die are required for making microholes on raw ceramic strips. The opening of the die is generally 12.5μm larger than the diameter of the punch die.
The key technical points of making microholes are installation and operation of micropunch. When the diameter of the punch is less than 100μm, the installation and operation of the punch becomes more difficult due to the loss of robustness. Most stamping defects do not form during stamping, but are caused by improper operation. Therefore, special tools are required to install the micro punch, and the impact and damage of the punch must be avoided during installation and operation. Align the punch and die. To make mechanical punching produce high quality through holes, largely depends on the alignment between the punch and the die. If the two devices are not aligned, the quality of the through hole will decrease, the die will be damaged, and the punch may break. Ensure the quality of the microholes, including the shape, size and internal penetration of the microholes.
The diameter and spacing of microholes formed by mechanical punching are better. The top edge is smooth, but the bottom edge is rough and the inner wall is flat. The top and bottom openings are close in size. The microhole sizes produced for LTCC ceramic strips of different thicknesses are also consistent, i.e. the ratio of the thickness of the ceramic strip to the size of the through hole does not affect the quality of the through hole. Using mechanical punching, 50, 75, and 100 μm microholes were formed on LTCC strips of 50 to 254 μm thickness, indicating that the opening diameters of the front and back LTCC strips of different sizes were within the allowable measurement error range, but the opening deviations were greater on the back of the ceramic strip. The change of the opening of the die after punching was examined under the microscope. The size of the opening was increased compared with that of the original opening, which was caused by the wear of the opening of the die. The analysis data of different microholes show that the size of the punch determines the size of the front opening of the through hole, while the diameter of the back opening is affected by the size of the die opening.
Therefore, when the die opening exceeds a certain value due to wear, the opening on the back of the micro hole will greatly increase, and the die should be replaced at this time. Another factor affecting the quality of the micropass hole is the residue in the through hole, which is a small piece of LTCC ceramic tape that remains at the through-hole opening and is not completely removed when punching. These residues are found primarily on the back of the LTCC ribbon layer, attached to the through-hole edge, and are typically 10-25μm in size. The number of holes containing residues decreases with the increase of the size of the holes, and the content of residues is independent of the thickness of the ceramic strip.
(2) Microporous injection method
Microinjection usually works best, but requires specialized equipment. In a microporous injection system, the main factors that affect the quality of the through-hole filling are injection pressure, injection time, filling paste viscosity, and alignment between the LTCC ceramic strip and the through-hole filling mask. Once the parameters applicable to the entire manufacturing process are determined, thousands of through holes can be filled in the LTCC raw porcelain strip layer in a matter of seconds. Note the underfilling, overfilling, and underfilling of microporous metallization.
75μm microporous filled with silver paste. The through hole filled with stock has the required size and satisfactory filling quality. An overfilling defect on the back of the LTCC porcelain tape, caused by the use of an unsuitable porous liner paper between the vacuum chuck and the LTCC porcelain tape. When the through-hole is filled and there is a misalignment between the mask and the LTCC ceramic strip, the front of the LTCC raw porcelain strip in contact with the mask will have an overfill defect. Top through holes 75μm apart. The hole spacing was shortened as a result of overfilling. If overfilling occurs between the through-holes, the spacing of the holes must be increased to avoid a short circuit caused by the extra stock that is overfilled, but this reduces the internal interconnection density.
(3)LTCC substrate stripping and sintering
The technical points of sintering are to control the shrinkage rate of sintering and the overall change of the substrate, to control the shrinkage properties of the two materials, to avoid the production of micro and macro defects, and to achieve the oxidation resistance of conductor materials and the removal of adhesives in the process of desintering. The sintering shrinkage rate of ordinary LTCC substrate is mainly achieved by controlling the particle size of powder, the ratio of casting binder, the pressure of hot laminated sheet, the sintering curve and so on. But the general LTCC co-firing system shrinkage along the X-Y direction is still 12-16%. Materials with zero shrinkage in the X-Y direction can be obtained by means of non-pressure sintering or pressure - assisted sintering.
The process to achieve zero shrinkage is as follows: self-constrained sintering, the substrate in the free co-firing process shows its own characteristics to inhibit the plane direction shrinkage, this method does not need to add new equipment, but the material system is unique, can not meet the requirements of manufacturing products with different properties. The shrinkage in the X-Y plane is suppressed by pressure assisted sintering in the z-axis direction. In non-pressure-assisted sintering, interlayers (such as alumina, which is not sintered at LTCC sintering temperatures) are added between the laminated materials to limit movement in the X and Y axes. After firing, the upper and lower clamped alumina layers are ground away. In the composite plate joint burning method, the green body is glued to the metal plate (such as molybdenum or tungsten with high mechanical strength) for sintering, and the binding effect of the metal sheet is used to reduce the shrinkage of the green body in the X-Y direction. Ceramic sheet and green sheet laminated sintering process, ceramic sheet as a part of the substrate, after firing need not be removed, there is no residual inhibition concern.
(4)LTCC circuit board large area ground brazing
LTCC roadbed plate large area grounding brazing process design, improve LTCC roadbed plate large area grounding brazing process of brazing rate and reliability. The (Ni+M) composite metal film is installed on the LTCC subgrade plate ground. According to the comparison of test, the welding resistance (> 600s) is significantly better than conventional metallized bonded strata (conventional requirements > 50s); A convex point is preset at one end of the ground of the LTCC electric subgrade plate. Through the comparative analysis of X-ray scanning images, the design of adding convex points can improve the brazing rate of large area ground brazing. The results show that the new brazing process design can guarantee the reliability and consistency of brazing for large area grounding of LTCC subgrade plate.
(5) LTCC circuit detection
LTCC components must be tested in many aspects after being drained, sintered and welded to ensure the reliability of their performance. These tests include aspects such as appearance, size, strength, electrical performance and so on.