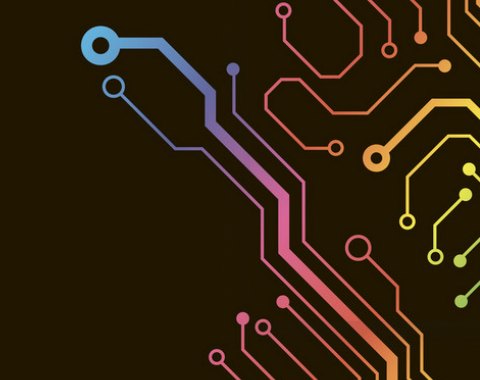
A special copper clad plate is used, and the surface of the copper platinum layer is pre-coated with a layer of sensitive material, so it is called "pre-coated sensitive copper plate", also known as "sensitive plate". The production method is as follows:
Print the circuit diagram 1:1 on a relatively transparent (thin), at least one side is relatively smooth and flat paper, and the mirror should be printed on the flat side.
Then the paper smooth surface close to the photosensitive circuit board (with glass clamping), put in the sun irradiation 2-8 minutes, the length of time is related to the strength of the sun, cloudy days can be irradiated for about 20 minutes. Note: The above is the reference time of the transparent film, and the time of the white paper is extended according to the transmittance of the paper. This process must not move the relative position of the paper and the circuit board, and should be tight.
The board is then developed under a developing solution (washing away unwanted photoreceptors), which prevents the copper from reacting with the next step of ferric chloride. This process usually takes 1-3 minutes. The time is inversely proportional to the degree of exposure, if the exposure is excessive, the development time will be very short, if the exposure is insufficient, the development time will be very long, even more than 10 minutes, in addition, it is also related to the concentration of the development water. However, it is strongly recommended that the exposure should not be excessive, and that the development time should be longer, so that there will be no mistakes and 100% success can be guaranteed.
Finally, after ferric chloride corrosion, it generally takes about 10-60 minutes.
Since the above process is directly determined by the light of the copper skin, the accuracy can be very high. Therefore, skilled operators can generally make high-precision circuit boards within 30 minutes, and thermal transfer paper can also be printed for exposure, without the need for heating transfer process. The effect is better, and the price should be much more expensive, but it is generally acceptable.
① The production of a single panel: PCB drawings drawn by the computer, using inkjet paper to print out 1:1 black and white 720dpi drawings (component surface), if you use a laser printer output drawings can also be. Take a photosensitive board the size of the drawing and tear off the protective film. Use a glass plate or a plastic transparent plate to press the drawing with a photosensitive PCB board and expose it in the sun for 5-10 minutes. With the accompanying developer 1:20 water distribution for development, when the exposure part (unnecessary copper coating) is completely exposed, wash with water, you can use ferric chloride for corrosion. After skilled operation, can produce an accuracy of 0.1mm!
The production of double-sided circuit board: the steps refer to a single panel, and the double-sided board is mainly positioned on both sides to be accurate. Two sides can be exposed separately, but the time should be the same, one side should be protected with black paper when exposed.
Heat Transfer Method:
Hardware:
1: A printout device for producing high-precision plastic toner solder resistance layer, such as a laser printer or a copier (copiers need to have a copy of the original, the original can be printed using an inkjet printer).
2: A working iron.
3: A smooth backing paper for self-adhesive stickers.
4: A certain amount of ferric chloride etching liquid, according to the size of the board. In addition, it is better to have a digital thermometer with a range of 0 to 200 degrees, and high-end digital multimeters can also be included.
Software: low version of PROTEL, such as PROTEL2.5 Chinese version of PROTEL high version, such as PROTEL99SE Chinese version or even just a drawing program that comes with WIN in short, it is a software that can draw pictures.
The first step: Use a software that can generate images to generate some image files, such as organizing SCH with a low version of PROTEL, using the network table to generate the corresponding PCB diagram, or directly drawing PCB with Power PCB (if you do not know PROTEL, PowerPCB, or even WINDOWS paintbrush program), ready for printing.
Step 2: Print the PCB to the heat transfer paper (JS said that the heat transfer paper is the yellow backing of the self-adhesive paper!) .
Step 3: Lay the printed PCB transfer paper on the copper-clad plate and prepare for transfer.
Step 4: Heat with an electric iron (to be very hot) and press the black plastic powder on the transfer paper onto the copper-clad plate to form a high-precision anti-corrosion layer.
Step 5: The effect of the electric iron after the successful transfer! If you do it often and become skilled, it is easy to succeed.
Step 6: Prepare the ferric chloride solution for corrosion.
Step 7: The effect is not bad! Be careful not to corrode too much, corrosion end, ready for welding.
Step 8: Clean out the pad part and use the rest for solder resistance.
Step 9: Install the required components and weld them.
Note:
1: Do not make the iron too hot or too cool, the best temperature is between 140 and 170, within this temperature range, the transfer characteristics of plastic toner is the best.
2: To wait until the temperature is lower and then remove the transfer paper, slowly uncover, and find that the part that is not transferred is good, please cover it again, and heat and pressure again for heat transfer.
3: Some really problematic parts (such as broken wires) please use oil-based carbon pens or nail polish, paint and other remedies, but this is not a lot of cases.