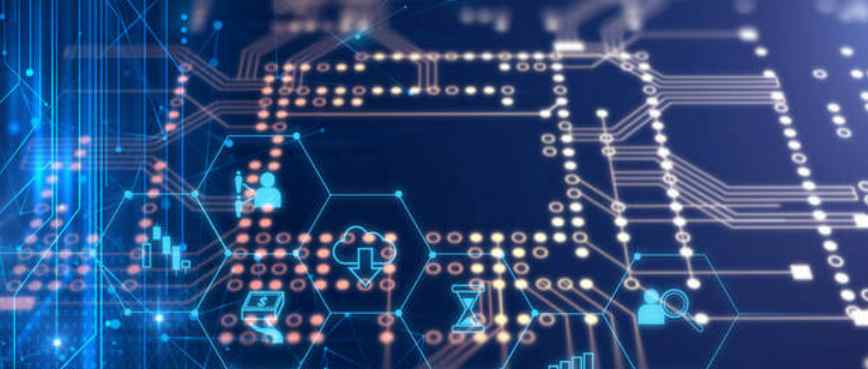
As we all know, circuit board cleaning technology plays a very important role in PCB copying board. Because to ensure that the circuit board itself cleaning in order to accurately scan the generated file diagram, circuit board cleaning technology has become an important "technical work". At present, the new generation of circuit board cleaning technology has the following four methods.
First, PCB board water cleaning technology
Water cleaning technology is the development direction of future cleaning technology. It is necessary to establish pure water source and discharge water treatment workshop. It takes water as the cleaning medium, adding surfactants, additives, corrosion inhibitors, chelating agents and so on to form a series of water-based cleaning agents. It can remove water-based solvents and non-polar pollutants. The characteristics of its cleaning process are:
(1) Safe, non-combustible, non-explosive, basically non-toxic;
(2) The formula of cleaning agent has large freedom, easy to clean polar and non-polar pollutants, and a wide range of cleaning;
(3) Multiple cleaning mechanism. Water is a polar solvent with strong polarity. In addition to dissolution, it also has the functions of saponification, emulsification, substitution and dispersion. Using ultrasound is much more effective than using organic solvents;
(4) As a natural solvent, the price is relatively low, wide range of sources.
The disadvantages of water cleaning are:
(1) In areas with scarce water resources, this cleaning method needs to consume a large amount of water resources and is limited by local natural conditions;
(2) Some parts can not be cleaned with water, metal parts are easy to rust;
(3) the surface tension is large, small gaps are difficult to clean, and the residual surfactant is difficult to remove completely;
(4) It is difficult to dry and consumes a lot of energy;
(5) The equipment cost is high, the need of wastewater treatment equipment, equipment covers a large area.
Two, PCB copy board semi-water cleaning technology
Semi-water cleaning mainly uses organic solvents and deionized water, plus a certain amount of active agents and additives. This cleaning method is between solvent cleaning and water cleaning. These cleaning agents are organic and flammable solvents with high flash points and low toxicity. They are safe to use, but they must be rinsed with water and then dried. Some cleaners add 5%~20% water and less surfactants, which can reduce flammability and make rinsing easier. The characteristics of semi-water cleaning process are:
(1) The cleaning ability is relatively strong, can remove polar pollutants and non-polar pollutants at the same time, the cleaning ability is durable;
(2) Use two types of cleaning and rinsing. For different properties of the medium, generally rinse with purified water;
(3) After rinsing should be dried.
The disadvantage of this technology is that the treatment of waste liquid and wastewater is a relatively complex problem that has not been completely solved.
Three, PCB copy board free cleaning technology
Use clean free flux or clean free solder paste during welding. After completion of welding directly into the next process, no cleaning. No-cleaning technology is the most commonly used alternative technology at present, especially the mobile communication products basically use no-cleaning to replace ODS. Clean free flux can be roughly divided into three categories:
(1) Rosin flux: reflow using inert rosin solder (RMA), can be washable.
(2) Water-soluble flux: clean with water after welding.
(3) Low solid content flux: no need to clean.
No - cleaning technology has the advantages of simplifying process, saving manufacturing cost and reducing pollution. The wide use of no-wash welding technology, no-wash flux and no-wash solder paste is a major feature of the electronics industry in the late 20th century. The ultimate alternative to CFCs is clean free.
Four, PCB copy board solvent cleaning technology
Solvent cleaning mainly uses the solubility of the solvent to remove contaminants. Solvent cleaning, fast volatilization, strong dissolving ability, simple equipment requirements. According to the selected cleaning agent, can be divided into flammable cleaning agent and non-flammable cleaning agent. The former mainly includes organic hydrocarbons and alcohols (such as organic hydrocarbons, alcohols, glycol esters, etc.), while the latter mainly includes chlorinated hydrocarbons and fluorinated hydrocarbons (such as HCFCS and HFCS).
When designing PCB pad in PCB design, it is necessary to design in strict accordance with relevant requirements and standards. Because in SMT patch processing, PCB pad design is very important. Pad design will directly affect the weldability, stability and heat transfer of components, which is related to the quality of patch processing. So what is the design standard of PCB pad?