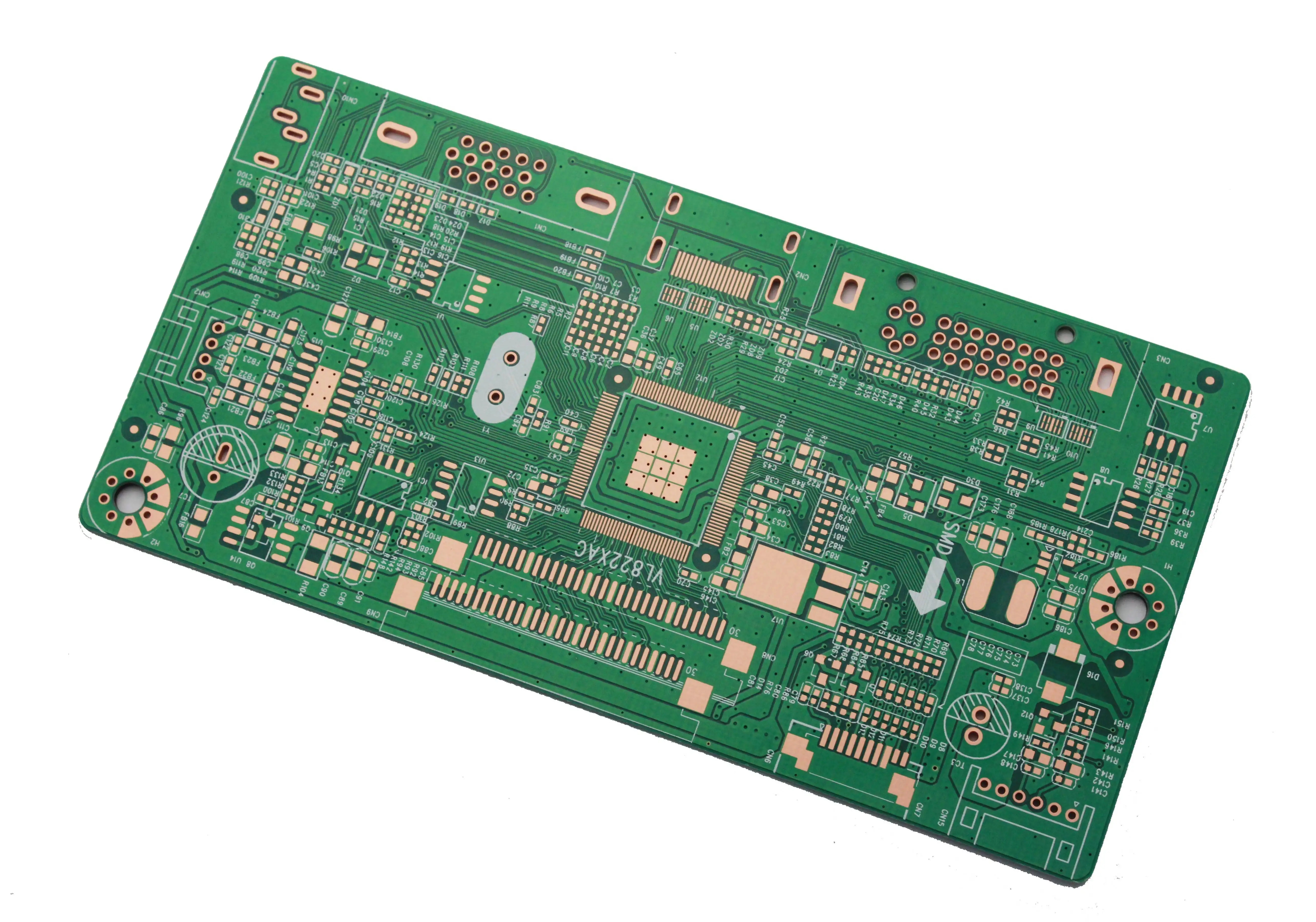
Editing of cooling and fault reduction methods after SMT patch red glue welding
Cooling after welding
A cooling workstation is usually added at the tail of the wave soldering machine. This is to limit the tendency of copper tin intermetallic compounds to form solder joints. Another reason is to accelerate the cooling of components and avoid board displacement when the solder is not completely cured. Quickly cool the assembly to limit the exposure of the sensitive element to high temperatures. However, the harmfulness of corrosive cooling system to the thermal shock of components and solder joints shall be considered. A well controlled "soft and stable" forced gas cooling system shall not damage most components. There are two reasons for using this system: it can quickly process the board without hand clamping, and it can ensure that the temperature of the components is lower than that of the cleaning solution. People are concerned about the latter reason, which may be the cause of foaming of some flux residues. Another phenomenon is that sometimes it reacts with some flux dross, which makes the residue "cannot be cleaned". No formula can meet these requirements in terms of ensuring that the data set in the welding workstation meet the conditions and requirements of all machines, all designs, all materials and process materials. You must understand every step of the process. 4 Conclusion In a word, in order to obtain the best welding quality and meet the needs of users, each process step before and during welding must be controlled, because each step of the entire assembly process of SMT is interrelated and interacted, and any problem in any step will affect the overall reliability and quality. The same is true for welding operations, so all parameters, time/temperature, solder amount, flux composition and transfer speed should be strictly controlled. For the defects produced in welding, the causes shall be found out as early as possible, analyzed, and corresponding measures shall be taken to eliminate various defects affecting quality in the bud. Only in this way can the products produced be guaranteed.
Fault reduction method editing
The manufacturing process, handling, and printed circuit assembly (PCA) testing will subject the package to a lot of mechanical stress, which will lead to failure. As the grid array package becomes larger and larger, it becomes more difficult to set the security level for these steps.
For many years, the use of monotonic bending point test method is a typical feature of packaging, which is described in IPC/JEDEC-9702 "Monotonic Bending Characteristics of Horizontal Interconnection of Boards". This test method describes the fracture strength of horizontal interconnection of printed circuit boards under bending load. However, this test method cannot determine the maximum allowable tension.
For the manufacturing process and assembly process, especially for lead-free PCA, one of the challenges it faces is the inability to directly measure the stress on the solder joints. The most widely used measure to describe the risk of interconnected components is the PCB tension adjacent to the component, which is described in IPC/JEDEC-9704 Guidelines for PCB Strain Testing.
With the expansion of the use of lead-free equipment, the interest of users is growing; Because many users face quality problems.
With the increasing interest of all parties, IPC felt that it was necessary to help other companies develop various test methods to ensure that BGA was not damaged during manufacturing and testing. This work was jointly carried out by IPC 6-10d SMT Attachment Reliability Test Methods Working Group and JEDEC JC-14.1 Packaging Equipment Reliability Test Methods Subcommittee. At present, this work has been completed.
This test method specifies eight contact points arranged in a circular array. The PCA with a BGA in the center of the printed circuit board is placed in such a way that the component is installed on the support pin face down, and the load is applied to the back of the BGA. The strain gauge shall be placed adjacent to the component according to the recommended gauge layout of IPC/JEDEC-9704.
The PCA will be bent to the relevant tension levels, and failure analysis can determine the extent of damage caused by bending to these tension levels. The tension level without damage can be determined by iterative method, which is the tension limit.
PCB manufacturers, PCB designers and PCBA processors will explain the cooling and fault reduction methods after SMT patch red glue welding.