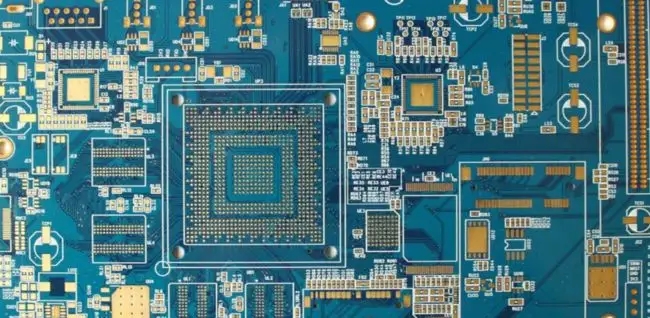
BGA repair method and precautions
In PCBA welding, problems often occur due to BGA welding or SMT chip processing. In particular, BGA problems are the most serious. If problems occur in the welding of a BGA, the whole board will have problems. This time, we will share the BGA repair issues in PCBA welding.
In PCBA welding, problems often occur due to BGA welding or SMT chip processing. In particular, BGA problems are the most serious. If problems occur in the welding of a BGA, the whole board will have problems. This time, we will share the BGA repair issues in PCBA welding.
1、 Front mounting method (ball setting tooling is adopted).
1. Put the cleaned and flat BGA pad upward on the BGA support platform at the bottom of the ball placing tooling.
2. Prepare a small template matching the BGA bonding pad. The opening size of the template should be 0.05~0.1mm larger than the diameter of the welding ball; Install the small template on the frame holding the template above the ball setting tooling, align it with the bonding pad of the BGA device below and fix it.
3. Place the BGA printed with paste flux or solder paste on the BGA support platform at the bottom of the ball placing tooling, with the printing facing up.
4. Move the template to the top of BGA (the position that has been aligned in the front), evenly leave the welding ball on the template, shake the ball setting tooling, so that a welding ball is reserved in each leakage hole on the template surface, and use tweezers to remove the excess welding ball from the template.
5. Remove the formwork
6. Check whether there is a lack of solder balls on each pad of the BGA device. If necessary, use tweezers to make up the solder balls.
BGA repair method and precautions
2、 Solder balls are mounted manually.
1. Place the BGA device printed with paste flux or solder paste on the workbench with the paste flux or solder paste facing upward.
2. Like SMT patch, use tweezers or suction pen to paste the solder balls one by one onto the solder with paste flux printed or welded
3、 A proper amount of solder paste is directly printed to form solder balls through reflow soldering.
1. SMT shall increase the thickness of the formwork and slightly enlarge the opening size of the formwork when processing the formwork.
2. Printing solder paste.
3. Reflow soldering. Due to the effect of surface tension, solder balls are formed after welding.
Among the above four methods of ball placement, the positive placement method (using ball placement tooling) has the best effect; Flip chip method (using ball placing equipment) is used for packaging BGA devices. Due to the poor dimensional accuracy of solder balls purchased from solder paste manufacturers, some solder balls with smaller diameters cannot be activated by paste flux or solder paste; The efficiency of manually mounting solder balls is relatively low: the method of directly printing star solder paste and forming solder balls through reflow soldering is the simplest, but the density of this solder ball is not good and it is easy to produce voids.
4、 Reflow welding
Reflow welding shall be carried out according to the repair process of BGA in the previous section. During welding, the welding ball of BGA device faces upward, and the hot air volume is adjusted to the minimum to prevent the welding ball from blowing and shifting. After reflow welding, the welding ball is fixed on the BGA device. The reflow welding of the ball placement process can also be carried out in the reflow welding furnace. The welding temperature is slightly 5~10 ℃ lower than the reflow welding of the assembly plate. After the ball placement process is completed, the BGA device should be cleaned, and the well should be mounted and welded as soon as possible to prevent the welding ball from oxidation and the device from getting damp.