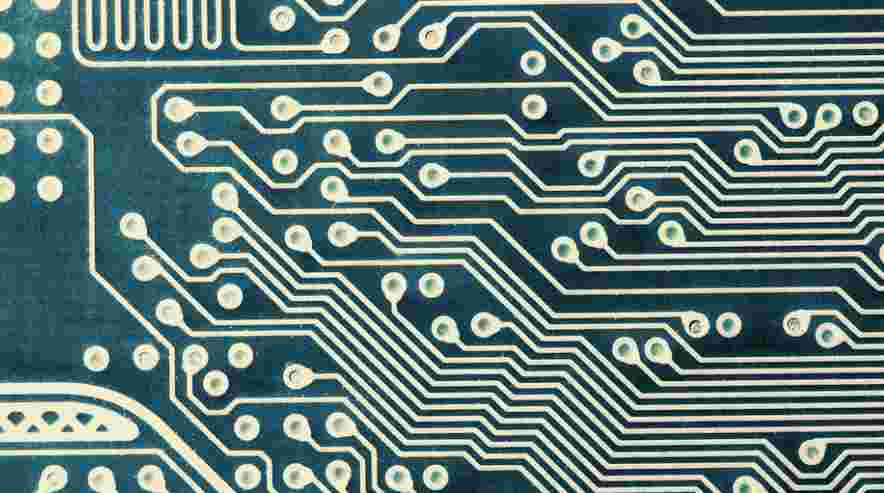
As the name suggests, flexible printed circuit boards are physically flexible. These PCBS are widely used in mechanically sensitive devices because the flexibility allows the board to resist vibration. Flexible PCB is more durable than traditional PCB, but flexible PCB manufacturing process is sensitive and complex.
Due to the light weight of the design, the board can be shaped according to the case, can be packed into a small volume, and the overall size of the final product can be reduced. Flex PCBs eliminate the overuse of wiring harnesses and connectors in PCBS.
Flexible PCB application
Rigid plates add some limitations to product design, as they cannot be installed in limited Spaces. Circuit boards need to be resistant to vibration in products that are frequently subjected to mechanical shock.
Flexible PCBS are more suitable for this situation because they can be bent and wrapped if desired. They can survive harsh temperatures of -200 to 400 degrees Celsius. Compared with traditional circuit boards, these functions make flexible circuit boards more reliable and durable.
Computers and accessories
Flexible PCBS are very powerful in terms of signals and atmospheric conditions. The hard drive in your computer contains Flex PCBS. Because these PCBS provide high data transfer rates on physically small boards. Other electronic devices such as printers, calculators and laptop LCDS are often designed with flexible PCBS for similar reasons.
aircraft
Aircraft's electronic systems are often stuffed with cables and lightweight. A typical Airbus contains nearly 100 kilometers of cable, while a helicopter contains about 12 kilometers of cable. There can be no compromise on the reliability and performance of aircraft systems. Flexible PCBS reduce weight and lift significantly even when subjected to mechanical impact, making them ideal for aircraft.
car
Over time, automotive products have become more compact. Flexible PCBS add compactness to their design, as these PCBS can be placed in a limited space regardless of shape and still work efficiently. Flex PCBS enable designers to produce lightweight products while maintaining product performance.
Flexible PCBS are commonly used in engine management computers, air bag controllers and other electronic components of automotive products. Since cars are often exposed to high temperatures, which are tolerable for flexible PCBS, these boards feature modern automotive products.
Mobile phone
Cell phones are small, but they have a lot of functions. Ever wonder how to design dense circuits in such a compact enclosure? Flexible PCBS can synchronize multiple components with minimal space requirements.
Connecting wiring harnesses or rigid plates used to synchronize components is unfavorable because of the limited size and shape of the phone. Also, phones heat up, and traditional circuit boards can't handle the heat. In addition, the Flex PCBs has added water resistance to its design.
Nowadays, mobile phones, digital books are developing flexible PCBS, which is a major technological breakthrough. Imagine wrapping a phone or bending the pages of a digital book? It's not possible to use rigid PCBS, flexible PCBS are evolving as technology improves, and hopefully in the near future we'll be able to bend phones like pages.
Medical electronics
Medical electronics need to be highly accurate and durable. Wearables currently under development are often developed using Flexible PCBs, whose flexibility makes them suitable for console use.
Today, wearables are used to track physical fitness, and these gadgets are very compact and sophisticated. Flex PCBS can implant sensors into the patient's skin and monitor the results on a smartwatch or phone. This revolution in wearable medical devices is enabled by flexible PCBS.
It is usually necessary to place medical instruments inside the human body, such as pacemakers or pill cameras are often exposed to extreme atmospheric conditions and flexible PCBS are best suited for this situation.
Rigid PCBS are bulky and cannot employ shape changes and low performance at high signal transmission, making them unfavorable for medical electronics.
Recent research on Flex PCBS has allowed scientists to develop Flex PCBS that are better suited for medical devices. These PCBS were developed using organic materials to provide a more suitable quality for prosthetic components. These boards are more flexible than flexible traditional PCBS, which is exciting for the development of high-performance prosthetics.
Industrial applications of Flex-Rigid PCBs
Flexible PCBS can withstand extreme weather conditions and perform well even in harsh environments. RF devices often use Flex PCBS because the robust nature of these PCBS allows signal strength to be unaffected.
Flex PCBS are also used in industrial machines and distribution control systems.
sensor
Flex PCBs revolutionize sensors, modern sensors are built on flexible PCBS, which reduces their size. These sensors can be placed in limited and irregular Spaces and are suitable for design or more compact products.
Most modern military equipment uses Flex PCBS such as radar systems in military vehicles. Control systems in military grade equipment require high signal and conductive path robustness. Because equipment must be used at extreme temperatures, weather conditions are often difficult to withstand rigid PCBS. In addition, military equipment is often affected by vibration and mechanical stress, which can be easily tolerated for flexible PCBS. For these reasons, Flex PCBS are best suited for military equipment.