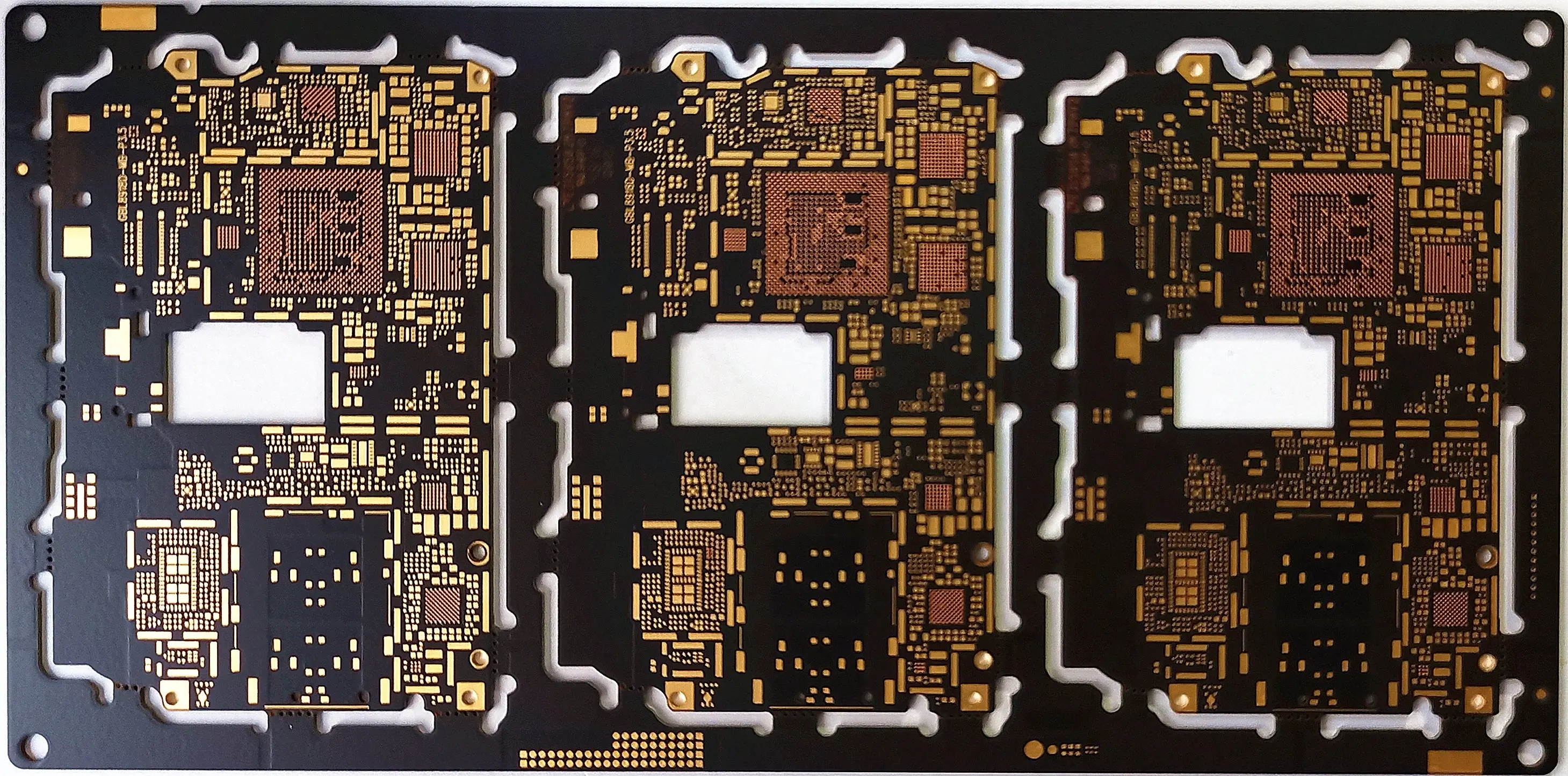
PCB thermal stress test method and how to improve thermal reliability
PCB manufacturers, PCB designers and PCBA manufacturers explain PCB thermal stress test practices and how to improve thermal reliability
How can PCB thermal stress test be done? What are the main conditions and inspection items? What information can be obtained from the test?
The thermal stress test used for PCB mainly includes thermal shock test and thermal cycle test. There are some different statements and definitions of this kind of practice, but the main types are these two. The main purpose of the thermal shock experiment is to simulate the rapid temperature rise and fall during the circuit board assembly, and detect the impact of the rapid temperature change on the stress of the circuit board. Common test methods include: tin floating (floating the circuit board on the tin furnace to simulate the wave soldering condition), hot oil dipping (also simulating the wave soldering condition, but there is no residual tin on the surface, so it is easier to observe and analyze the defects), and tin walking furnace (simulating the SMT assembly and soldering condition).
The main purpose of the thermal cycle experiment is to simulate the changes of the thermal stress that may affect the electronic products in the life cycle of use, but only by means of acceleration. In this way, it can be verified whether the simulated circuit board can meet the long-term reliability requirements of the product, so as to ensure its long-term reliability. This kind of test will be conducted at different levels for products of different levels, and IPC, JDEC and other organizations will define the specifications for this type of test. There are many kinds of test simulation methods, such as pressure cooker test (PCT), thermal cycle test (TCT), high speed stress test (HAST), etc. Because of the many and time-consuming standard test cycles, most product reliability tests are time-consuming. Some manufacturers have begun to develop testing methods with faster simulation speed to adapt to the rapidly changing world of electronic products. At present, typical methods such as high current stress testing (IST) are one of them.
In addition to the common standard specifications, some large manufacturers also adjust the number of test cycles according to the needs of the product. In this regard, both parties should be clear about the law to follow. However, in the early stage of product development, most manufacturers will adopt stricter methods to verify materials and products, and will only begin to relax to the monitoring standards when the monitoring period for mass production is over.
How to Improve the Thermal Reliability of PCB
In many applications, weight and physical size are very important. If the actual power consumption of components is very small, the design safety factor may be too high, so that the circuit board design uses the component power consumption value that is inconsistent with the actual or too conservative as the basis for thermal analysis.
In general, the copper foil distribution on pcb circuit board is very complex, and it is difficult to accurately model. Therefore, it is necessary to simplify the shape of the wiring when modeling. The electronic components on the circuit board of the ANSYS model circuit board that is as close as possible to the actual circuit board can also be simulated by using the simplified modeling, such as MOS tubes, integrated circuit blocks, etc.
thermal analysis
Thermal analysis during chip mounting can help designers to determine the electrical performance of components on pcb circuit boards, and help designers to determine whether components or pcb circuit boards will burn out due to high temperature. Simple thermal analysis is only to calculate the average temperature of the circuit board, and complex thermal analysis is to establish a transient model for electronic devices with multiple circuit boards. The accuracy of thermal analysis depends on the accuracy of component power consumption provided by circuit board designers.
In many applications, weight and physical size are very important. If the actual power consumption of components is very small, the design safety factor may be too high, so that the circuit board design uses the component power consumption value that is inconsistent with the actual or too conservative as the basis for thermal analysis. On the contrary (and more seriously), the design of thermal safety factor is too low, that is, the temperature of components in actual operation is higher than what analysts predicted. Such problems are generally solved by installing heat dissipation devices or fans to cool the circuit board. These external accessories increase the cost and extend the manufacturing time. The addition of fans in the design will also bring instability to the reliability. Therefore, active rather than passive cooling methods (such as natural convection, conduction and radiation cooling) are mainly used for PCB.
Simplified modeling of circuit board
Before modeling, analyze the main heating devices in the circuit board, such as MOS tubes and integrated circuit blocks, which convert most of the lost power into heat when working. Therefore, these devices need to be considered when modeling.
In addition, consider the copper foil on the circuit board substrate as the conductor coating. They not only conduct electricity, but also conduct heat in the design. Their thermal conductivity and heat transfer area are relatively large. The circuit board is an indispensable part of the electronic circuit. Its structure is composed of epoxy resin substrate and copper foil coated as a conductor. The thickness of epoxy resin substrate is 4mm, and the thickness of copper foil is 0.1mm. The thermal conductivity of copper is 400W/(m ℃), while that of epoxy resin is 0.276W/(m ℃). Although the added copper foil is very thin and thin, it has a strong guiding effect on heat, so it cannot be ignored in modeling. PCB manufacturers, PCB designers and PCBA processors will explain PCB thermal stress test practices and how to improve thermal reliability.