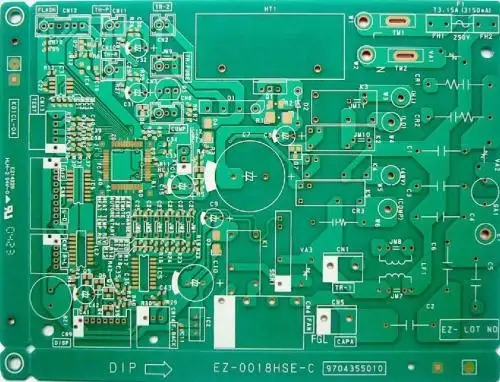
Sorting out common problems in baking package humidity sensitive parts
PCB Problems Packaging Humidity Sensitive Parts Baking Common Problems Sorting
Recently, I encountered many problems, one of which is why some SMD parts need to be baked? What is the humidity sensitivity level (MSL)? I often ask some questions about this and try to answer them as follows:
What is the purpose of part re baking?
Which parts need to be baked again?
How long does it take to bake?
Can the reels be baked in the oven?
Why does a PCB manufacturer claim that its low humidity drying oven can prevent moisture damage of humidity sensitive parts? What is its role?
Can the desiccant be reused?
Can parts be baked repeatedly? The longer you bake, the better? Are there any baking restrictions?
1. What is the purpose of the part re baking?
First of all, we should know which electronic parts will be harmed by moisture? Moisture will oxidize the solder legs of parts, resulting in poor solderability; In addition, if the moisture enters the interior of the package parts, such as IC package parts, when these parts undergo a rapid heating process, such as Reflow, the moisture and water molecules inside the package parts will rapidly expand their volume due to heating. At this time, if the moisture cannot effectively escape from the interior of the package parts, it will be stretched from the interior of the parts due to the expansion of the water molecules, causing delamination, Even explode from the inside of the part to form popcorn.
If the weld leg of the part has been oxidized, the oxidized weld leg can hardly be baked again to make it return to the state before oxidation. It may be reprocessed by electroplating. Therefore, the main purpose of baking is only to remove the moisture inside the packaged parts, so as to avoid the problem of delamination or popcorn when the parts flow through reflow.
2. Which parts need to be baked again?
As mentioned above, the purpose of baking is to remove the moisture inside the part, so as to avoid the problem of delamination or popcorn when the part is reflowed. Therefore, in principle, as long as the encapsulated parts (generally referred to as IC parts) are used, especially the encapsulated parts that need reflow soldering, as long as there is doubt that they are affected with moisture, they should be baked again.
As for hand welded parts or wave soldered packaged parts, if they are affected with moisture, do they also need to be baked? It is not clearly specified in J-STD-033B document. Although the temperature of manual welding and wave soldering is much lower than that of reflow soldering on the part body, if time permits, individuals still suggest that it is appropriate to bake the damped packaged parts according to J-STD-033B. After all, the temperature during the operation is still far higher than the boiling point of water, which may cause parts delamination.
Can I put 3 reels into the oven for baking?
According to the provisions of Section 4.2.1 and 4.2.2 of J-STD-033B, the packaging of general humidity sensitive parts must indicate whether the packaging can withstand the high temperature baking at 125 ℃ or the low temperature packaging at more than 40 ℃. Generally, if there is no mark, it means it can withstand 125 ℃ high temperature baking.
If the packaging material is low temperature packaging, all packaging must be removed during baking, and then replaced with the original packaging after baking. Whether it is high temperature or low temperature packaging, the original paper and plastic containers (such as cardboard, bubble bags, plastic packaging, etc.) must be picked out before baking, and pipe plugs and tray tapes must also be picked out before baking at high temperature (125 ℃).
4. Why does a circuit board manufacturer claim that its low humidity drying oven can prevent moisture damage of humidity sensitive parts? What is its role?
According to the instructions in Section 4.2.1.1 and 4.2.1.2 of J-STD-033B, if the components with humidity sensitivity level (MSL) 2, 2a and 3 are exposed to the workshop for less than 12 hours and placed in an environment ≤ 30 ° C/60% RH, as long as they are placed in a dry package or drying cabinet below 10% RH and exposed to the atmosphere for 5 times, the workshop life of the parts can be recalculated without baking.
In addition, if the exposure time of MSL 4, 5, 5a components in the workshop is less than 8 hours, and they are placed in an environment ≤ 30 ° C/60% RH, as long as they are placed in a dry package or drying cabinet below 5% RH, after 10 times of exposure time to the atmosphere, the floor life of parts can be re counted without baking.
Therefore, only circuit board manufacturers claim that when humidity sensitive parts are not used after being unsealed, they can be placed in an electronic drying cabinet below 5% RH to suspend or recalculate their workshop time. However, the storage space of the drying cabinet is limited after all. It is recommended to open the drying package of the parts before use to ensure that the parts will not be affected by moisture, and the temperature and humidity in the factory workshop should be controlled ≤ 30 ° C/60% RH.
5. Can the desiccant be reused?
According to Section 4.1.2 of J-STD-033B, if the desiccant in the drying package is only exposed to the factory environment below 30 ° C/60% RH for no more than 30 minutes, the original desiccant can be reused. But the precondition is that the desiccant is not damped or damaged.
6. Can parts be baked repeatedly? The longer you bake, the better? Are there any baking restrictions?
According to the description in Section 4.2.7.1 of J-STD-033B, excessive baking of parts may lead to oxidation of parts or formation of intermetallic metal, thus affecting the quality of welding and circuit board assembly. In order to ensure the solderability of parts, it is necessary to control the baking time and temperature of parts. Unless the supplier has special instructions, the cumulative baking time of parts at 90 ℃~120 ℃ shall not exceed 96 hours. If the baking temperature is below 90 ℃, there is no limit on baking time. If the baking temperature needs to be higher than 125 ℃, the supplier must be consulted, otherwise it is not allowed.
In addition, the compound used for IC encapsulated colloid will deteriorate and embrittle after repeatedly passing through high temperature (>Tg (glass transition temperature)), and the high temperature environment will also make the IMC originally formed in the IC accelerate its electron migration speed. When the holes of the IMC increase, the original wire bond will easily fall off, causing quality problems such as open circuit. Therefore, it is debatable whether the longer the baking time is, the better, At least baking at high temperature is not.