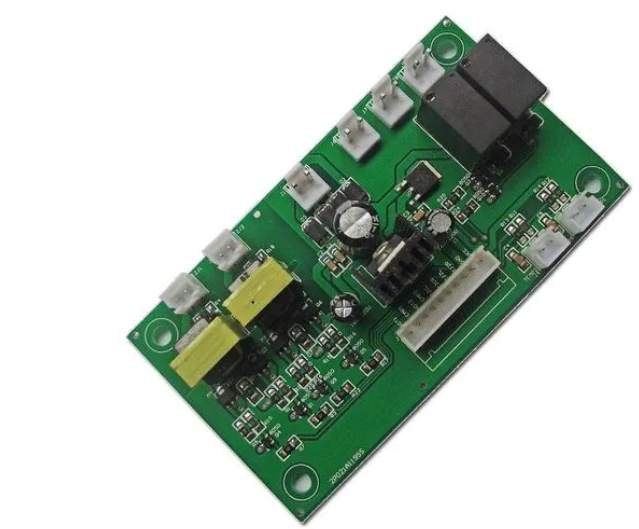
This paper describes the recent challenges facing PCB design engineers, and discusses how to meet these challenges and potential solutions. In addition, taking PCB evaluation package as an example, this paper describes how to solve the evaluation problem of PCB design software. As a developer, the main consideration is how to integrate the latest advanced technology into the product. The following patch manufacturer will explain how to solve the PCB evaluation problem and how to post the related knowledge of PCBA in SMT processing.
1. How to post PCBA for SMT processing
kingford is a PCBA OEM service provider, which can provide one-stop services from PCB board making, component purchasing, SMT processing, DIP processing to test and assembly. SMT processing as an important link of PCBA, the quality of processing directly affects the quality of products. SMT processing includes multiple processes. How to standardize each process to post perfect PCBA? SMT processing manufacturer kingford will explain to you next.
1. The printing of lead-free solder paste. In this operation part, we should note that the steel mesh is aligned with the PCB, and the opening of the steel mesh must be completely coincident with the PCB pad. Normal production can only be started after 3 pieces of trial printing are confirmed to be OK. After printing, each PCB should be self-checked. Printing solder paste is not allowed to appear more tin, less tin, even tin, offset and other undesirable phenomena. Bad printing products should be carefully cleaned. Clean the steel mesh in time. Add tin paste in time to ensure the amount of tin paste rolling on the steel net.
2. The machine we use for the mounting of small materials is CP machine. Able to mount materials quickly. Before starting the machine, you need to make sufficient preparations, such as the placement of materials, the positioning and setting of the machine, when the machine lights up yellow, you should prepare to fill the material for it.
3. The process of mounting large materials is to help PCB add large materials that cannot be mounted on CP machine before, such as crystal vibration. For this part, we use XP machines. It can realize the automatic mounting of large materials. Note that the process is similar to the CP machine.
4. Pre-furnace QC is an essential part of the whole SMT process. This link can ensure that all semi-finished products are completely without problems before passing through the furnace, so it is called pre-furnace QC. A QC is usually used in this position to check the PCB board flowing from the SMT machine. See whether there is a page leakage, bias and other problems. And then to the leakage or deviation of the plate manual correction.
5. Reflow soldering The function of reflow soldering is to melt the solder paste of the layout, so that the material is tightly welded to the layout. The machine required for this process is wave soldering. Wave soldering should pay attention to the matters also have a few points. The first is to adjust the temperature in the furnace, which needs to consider the heat degree of PCB board and the heat resistance degree of materials and other aspects, and then set the best temperature for wave soldering, so that the PCB board after the furnace basically no other problems.
6, after the furnace QC quality is life. After the furnace, there will certainly be some problems, such as air welding, virtual welding, welding and so on. So how do you find these problems? We must also match a QC on this link to detect the problem of the board after the furnace. And then we're doing manual corrections.
7. QA Spot Check When all the automatic mounting process is complete, we have a final step, which is spot check. Random inspection of this step, we can roughly assess the production of our products qualified rate, that is, quality. Of course, random inspection must be carefully done every step, do not miss every detail on the page, so as to ensure the quality of the company's products.
8, storage finally storage. Storage also need to pay attention to, to pack neatly, can not be sloppy. Only in this way can customers have a perfect experience. The above is the processing of a perfect PCBA need to pay attention to the place, if you have PCB products need to do PCBA processing, welcome to consult Shenzhen kingford
2. How to solve the PCB evaluation problem
These advanced technologies can be shown not only in excellent product features, but also in reducing the cost of products. The difficulty lies in how to effectively apply these technologies in products. There are many factors to consider, the timing of a product's launch being one of the most important, and many decisions are constantly updated around the timing of a product's launch. Under this premise, a wide range of factors must be considered, from product function, design implementation, product testing and electromagnetic interference (EMI) compliance are included.
It is possible to reduce design iteration, but this must depend on the completion of the previous work. Most of the time, it's easier to find problems later in the product design process, and more painful to fix them. However, while many people are aware of this rule of thumb, the reality is that many companies are aware of the importance of having a highly integrated design software, but the idea is often limited by a high price tag. This article will explain the challenges of PCB design and what to consider as a PCB designer when evaluating a PCB design tool.