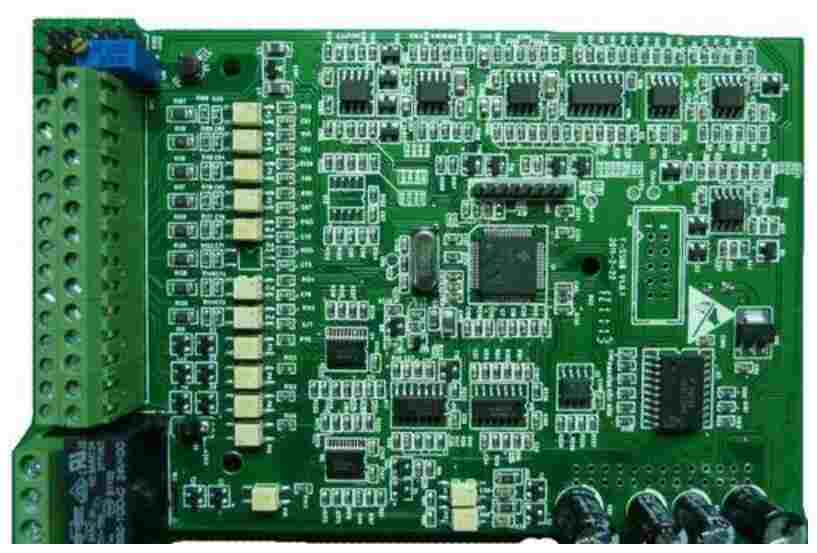
kingford takes you to understand how to improve the quality of smt patch processing. The following patch processing manufacturer Xiaobian will explain how to ensure the quality of SMT patch solder paste and how to improve the quality of smt patch processing.
1. How to improve smt patch processing quality
First: the enterprise to establish a total quality (TQC) organization network, quality feedback timely, accurate selection of the best quality personnel as the quality inspector of the production line, and the administration is still under the quality department management, so as to avoid other factors to the quality of the work of interference.
2: In order to ensure that the inspection and maintenance of accurate products of testing and maintenance equipment is carried out through the necessary equipment and instruments, such as multimeters, anti-static wrists, soldering iron, ICT and so on. Therefore, the quality of the instrument itself will directly affect the quality of production. In accordance with the provisions of timely inspection and measurement, to ensure the reliability of the instrument.
3: It is unrealistic to set the quality process control point to achieve "zero defect" production, but the implementation of "zero defect" production goal in the whole factory can greatly improve the quality awareness of the whole factory staff, and provide continuous power for timely and standardized solution of quality anomalies in production.
4: the quality department shall formulate necessary rules and regulations related to quality and the work responsibility system of the department to restrict the avoidable quality accidents by laws and regulations, reward and punishment are clear, participate in the quality assessment by economic means, and set up monthly quality awards within the enterprise.
2. How to ensure the quality of SMT solder paste
1. Quality problems caused by poor solder printing are as follows:
1, insufficient solder paste (local or even lack of overall lack) will lead to insufficient number of solder joints after soldering component, component 2, offset, component, component, upright. 3, solder paste adhesion will lead to circuit short welding, components offset. 4. The overall offset of solder paste printing: it will lead to poor welding of the whole plate components, such as less tin, open circuit, offset, vertical parts, etc. 5, the solder paste is easy to cause short circuit after welding
Two, the main factors leading to the lack of solder paste:
1. The solder paste was not added in time when the printing press was working. 2. Abnormal quality of solder paste, which is mixed with hard and other foreign bodies. 3. The previously unused solder paste has expired and is used twice. 4, circuit board quality problems, there is an inconspicuous cover on the pad, such as the solder resistance (green oil) printed on the pad. 5, the circuit board in the printing press fixed clamping loose. 6, solder paste printing screen thickness is not uniform. 7, solder paste leakage screen board or circuit board there are pollutants (such as PCB packaging, screen board wiping paper, floating foreign bodies in the air, etc.). 8, solder paste scraper is damaged, the screen is damaged. 9. SMT parameters of solder paste scraper, such as pressure, Angle, speed and demoulding speed, are not set properly. 10. After the solder paste was printed, it was accidentally knocked off because of human factors.
3, the main factors leading to solder paste adhesion:
1, circuit board design defects, welding pad spacing is too small. 2, the mesh plate problem, the hole is not correct. 3, the net board is not wiped clean. 4, the problem of the net plate makes the solder paste fall off badly. 5, solder paste performance is poor, viscosity, collapse is not qualified. 6. The fixed clamping of the circuit board in the printing press is loose. 7. SMT parameters of solder paste scraper, such as pressure, Angle, speed and demoulding speed, are not set properly. 8. After the solder paste is printed, it is squeezed and adhered to because of human factors.
4, the main factors that lead to the overall deviation of solder paste printing:
1. The positioning reference point on the circuit board is not clear. 2, the positioning datum point on the circuit board and the datum point of the network board is not correct. 3. The fixed clamping of the circuit board in the printing press is loose. Position The thimble is not in place. 4. The optical positioning system of the printing press fails. 5, solder paste leakage screen plate opening and PCB design documents do not conform to.
5, the main factors leading to the printing solder paste tip:
1, solder paste viscosity and other performance parameters are problematic. 2. The demoulding parameters of the separation of circuit board and leakage screen board have problems. 3, leakage screen hole hole wall burr.
1. Common quality problems of SMT patches include leakage, side parts, parts, offset, loss, and so on.
7, the main factors leading to patch leakage:
1. feeder rack of components (feeder) is not in place. 2. The element suction nozzle inlet is blocked, the suction nozzle is damaged, and the height of the suction nozzle is incorrect. 3. The true air path of the equipment fails and is blocked. 4, circuit board purchase is poor, deformation. 5. There is no solder paste or too little solder paste on the PCB pad. 6, the quality of components, the thickness of the same variety is inconsistent. 7. The patch caller has errors or omissions, or the component thickness parameter is selected incorrectly when programming. 8, human factors accidentally knocked off.
8, the main factors that lead to SMC resistance patch, side:
1. feeder rack of components (feeder) is abnormal. 2, the height of the mounting head is not right. 3, the height of the mounting head is not right. 4. The charging hole size of component braiding is too large, and the component turns over due to vibration. 5. The direction of the bulk material is reversed when it is put into the braid.
Ix. Main factors leading to the offset of component patches:
1. During the programming of the SMT machine, X-Y axis coordinates of the components are incorrect. 2. The reason for the patch suction nozzle makes the suction unstable.
Ten, the main factors leading to the damage of components and patches:
1, 1 positioning thimble is too high, so that the circuit board is too high, components are squeezed during the installation process. 2. The Z-axis coordinates of the components are incorrect during the programming of the SMT machine. 3. The suction spring of the sticking head is stuck.