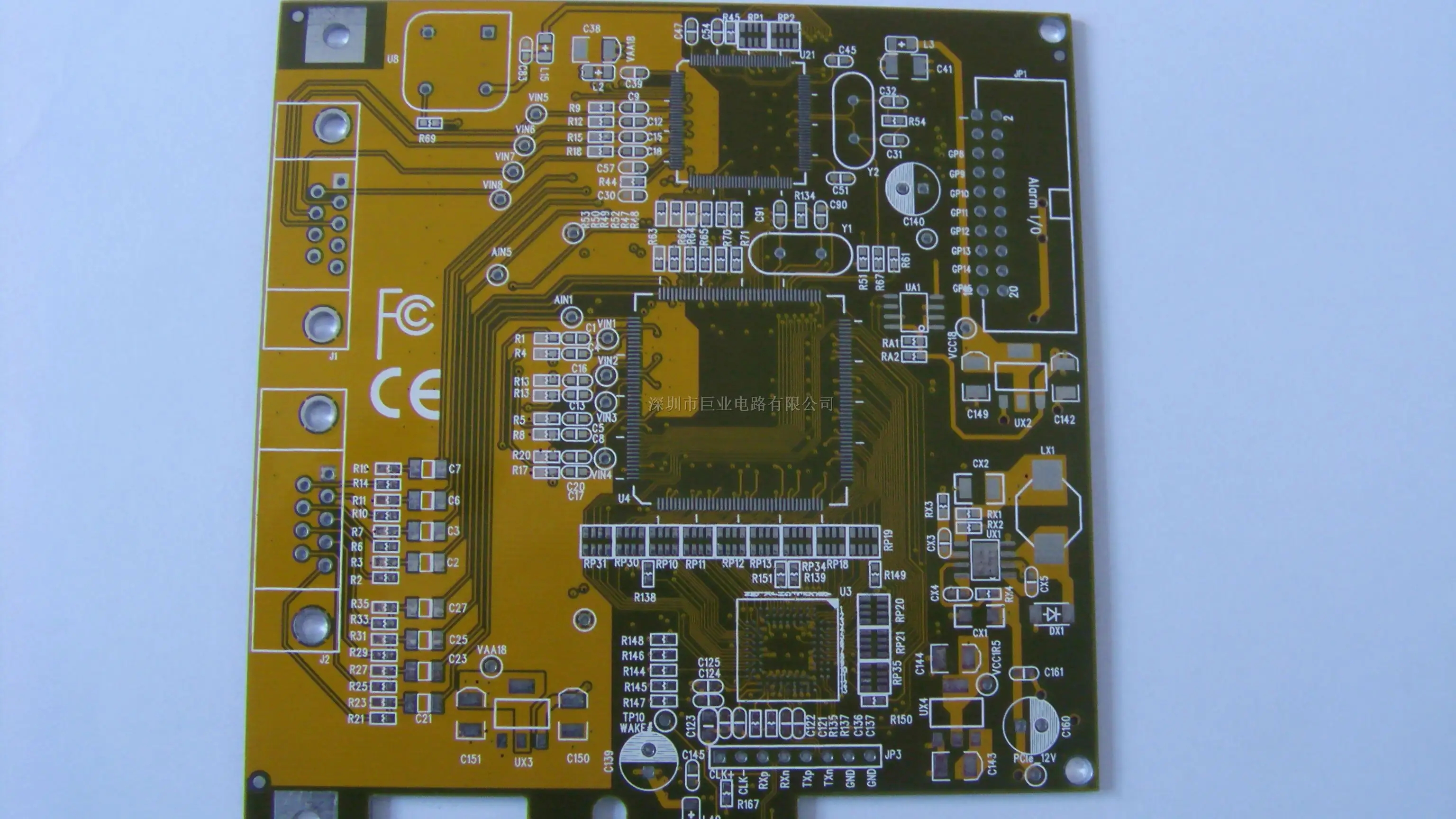
Cause the quality of PCBA welding metal bonding layer
Alloy composition is the key parameter to determine the melting point of solder paste and the quality of solder joint. From the general wetting theory, the ideal brazing temperature of most metals should be 15.5~71 ℃ higher than the melting point (liquidus) temperature. For Sn series alloys, it is recommended to be about 30~40 ℃ above the liquidus.
The quality and thickness of PCBA welding metal bonding layer are related to the following factors.
1、 Alloy composition of solder
Alloy composition is the key parameter to determine the melting point of solder paste and the quality of solder joint. From the general wetting theory, the ideal brazing temperature of most metals should be 15.5~71 ℃ higher than the melting point (liquidus) temperature. For Sn series alloys, it is recommended to be about 30~40 ℃ above the liquidus.
What are the causes of the quality and thickness problems of PCBA welding metal bonding layer
Taking Sn Pb solder alloy as an example, the analysis of alloy composition is the key parameter to determine the melting point and solder joint quality.
(1) The eutectic alloy has the lowest melting point and the lowest welding temperature
In the Sn Pb alloy proportion, the melting point of eutectic alloy is the lowest, the melting point of 63Sn-37Pb eutectic alloy (point B) is 183 ℃, and the PCB welding temperature is also the lowest, about 210~230 ℃, so that components and PCB circuit boards will not be damaged during welding. The liquidus of any other alloy ratio is higher than the eutectic temperature. For example, the liquidus of 40Sn-60Pb (H point) is 232 ℃, and the SMT patch welding temperature is about 260 ~ 270 ℃. Obviously, the welding temperature exceeds the tolerance limit temperature of components and PCB printed boards.
(2) The structure of eutectic alloy is the most compact, which is conducive to improving the strength of solder joints
Eutectic solder is a kind of eutectic alloy, in which the solid phase changes from solid to liquid or from liquid to solid at the same temperature. When the temperature rises to the eutectic point, the solder is in a liquid state. When the temperature drops to the eutectic point, the liquid solder suddenly becomes a solid state. Therefore, the smallest crystalline particles, the densest structure and the highest solder joint strength are formed when the solder joint solidifies. However, if the alloy of other proportions has a long condensation time, the first crystalline particles will grow up, which will affect the strength of the solder joint.
(3) There is no plastic range or viscosity range when eutectic alloy solidifies, which is conducive to the control of welding process
Eutectic alloys will change from solid phase to liquid phase as soon as they reach the eutectic temperature when they are heated up; On the contrary, as long as the temperature of eutectic point is reduced during cooling and solidification, the eutectic alloy will immediately change from liquid phase to solid phase, so there is no plastic range in the melting and solidification process. The solidification temperature range (plastic range) of the alloy has a great influence on the weldability and the quality of the solder joint. Alloys with a wide range of plasticity,
It takes a long time for alloy solidification and solder joint formation. If PCB and components have any vibration (including PCB deformation) during alloy solidification, it will cause "solder joint disturbance", which may lead to solder joint cracking and premature equipment damage.
From the above analysis, it can be concluded that alloy composition is the most critical parameter to determine the melting point and melting point quality of solder paste. Therefore, whether it is traditional Sn Pb solder or lead-free solder, it is required that the alloy composition of solder should reach eutectic or near eutectic as far as possible.
2、 Oxidation degree of alloy surface
The oxide content on the surface of the alloy powder also directly affects the solderability of the solder paste. Because diffusion can only enter on the clean metal surface
that 's ok. Although the flux has the function of cleaning oxides on the metal surface. However, serious oxidation problems cannot be eliminated. It is required that the oxygen content of alloy powder should be less than 0.5%, preferably controlled below the minus sixth power of 80x10.