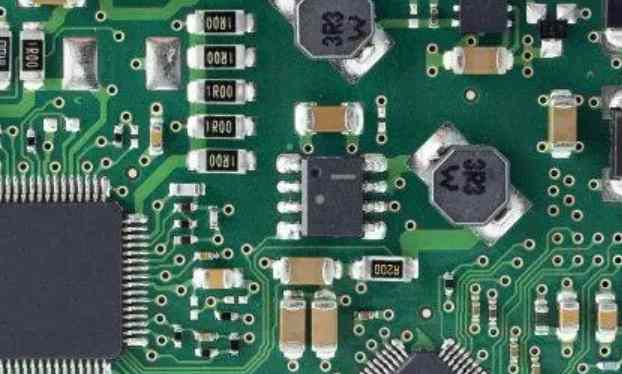
Designing with rigid flexible circuits is different from designing with HDI boards. All engineers know how difficult it is to design and create the perfect rigid flexural PCB design. With limited space, there's a lot to remember. Installing all the components and making sure the board is easy to make is tricky. This guide is designed to pass on some of the best practices developed in our extensive experience designing flexible PCBS. Before designing complex or complex flexible PCBS, engineers must understand the level of performance required and the manufacturing methods available.
Install the rigid flexible PCB into the housing
The design of the shell is crucial to determining the function and feel of the product. As with any product design, it should be created to meet the needs of its intended users. For rigidly flexible combined PCBS, this means designing a shell that meets functional requirements and is suitable for everyday use in the hands of consumers.
One way is to mount the printed circuit board to another surface, such as a plastic casing or a larger rigid material, using an adapter board. Another option is to use a flexible housing that allows you to bend the plastic around the edges of the printed circuit board to fit naturally inside the housing without any special tools or hardware.
The housing must be designed to fit the rigid flexible PCB, cables and other components within it. If any of these components are not considered during the design process, there is a chance that they will not fit well into the final shell. This can lead to assembly and manufacturing problems and poor performance after assembly.
Control and maintain flexible circuit profile tolerances
When creating rigid-flexible PCB designs, it is necessary to control the profile and thickness of the flexible circuit. This requires tolerances for each layer in the design. This ensures that the previous design can be used as a template when creating a new design. The following steps are used to set tolerance parameters:
Step 1: Create an existing rigid-flexible PCB design that you want to use as a template.
Step 2: Open the new design in which you want to add flexible circuits, and first set the parameters of the top copper layer. Next, set parameters for all the other layers except the layer used for pad and through hole.
Step 3: Select all copper layers except those used for pads and holes, right-click one of them, and select Properties from the pop-up menu. The Properties dialog opens, showing all layers except those used for pad and throughhole. Set tolerances for the top copper layers only at this time, as additional layers will be added later after setting parameters for them separately during this process.
Design to maintain the integrity of rigid flexible PCB bending radius
The bending radius is the maximum distance between two planes in a part or assembly that are parallel to each other and separated by a specific radius. Bending radius is critical when designing PCBS because it affects the strength of the board and its ability to withstand stress.
Bending radius optimization
Designers need to keep the bending radius as small as possible while maintaining the electrical properties of rigid and flexible bonded plates. They should also consider the possible need to increase the thickness of a particular layer or reduce the number of layers to maintain adequate stiffness.
Bending insensitive technique
Bending does not affect most electronic components because they are specifically designed for this purpose and have been tested for reliability with slight bending. However, some components may not be able to withstand the extreme stress caused by bending, so designers should consider using "bending insensitive techniques" to prevent the failure of these devices when they bend during manufacturing or after installation to final application.
Understand the long-term reliability of polyimide and polyester materials
Understanding the long-term reliability of polyimide and polyester materials is critical to creating rigid flexible PCB designs. Polyimide and polyester are the two most widely used materials in PCB manufacturing. Both materials have their advantages and disadvantages.
Polyimide is a thermosetting plastic material commonly used in electronics manufacturing. It is known for its excellent thermal stability, low dielectric constant, high breakdown voltage and high dielectric strength. This makes it suitable for creating rigid flexible printed circuit boards.
In contrast, polyester is a heat-resistant polymer with good mechanical properties and dimensional stability. This makes it ideal for creating rigid flexible printed circuit boards with embedded chips or other components that require high performance and durability.
Both polyimide and polyester have excellent long-term reliability when making rigid flexible PCB boards.
Ensure the mechanical strength of rigid flexible PCB components with cladding and solder resistance