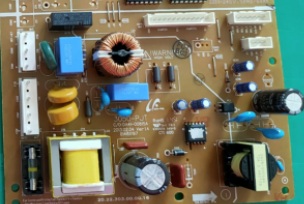
At present, the domestic electronic processing industry is very prosperous. However, serious material consumption and slow processing often occur when PCBA proofing is carried out. These two situations virtually make the cost of developing sample patches become higher. Next, Shenzhen kingford, SMT manufacturer in Shenzhen, will introduce how to avoid serious material consumption and high throwing rate in SMT patch processing.
First, in order to eliminate the high casting rate in the process of PCBA proofing, human factors cannot be ignored naturally. For example, the common operation that leads to high casting rate is that the tearing belt is too long and the pressing material is too much when the operator is installing the material, which results in material modification or loss. The solution is that the operator should reserve two or three empty slots when loading. And ensure that each link operation specifications, it is best to have a unified elastic standard.
Second, in the process of PCBA sampling processing, there was also a situation that there was debris on the table after the installation of feeder, resulting in shaking and unable to get the material. In this case, it is necessary to train the operator to check whether there is debris on the machine table and feeder chassis when installing feeder, and clean the table of the machine timely when pulling. And in order to ensure that the material tray is not installed on the feeder, resulting in chucking or throwing, the operator must install the tray to the feeder when refueling.
Third, in the process of PCBA proofing, the high rate of throwing material may also be caused by putting the reverse board or picking the wrong board and wiping the board. The solution is still to require the operator to complete the work in accordance with the standard operation process, and before the work, the position and direction of the board should be marked in the guide book as well as the daily summary of the matters for attention. In this way, the construction efficiency and accuracy of the operator can be ensured.
The points just mentioned are that when PCBA sampling is carried out, if the high throwing rate caused by human factors is avoided, and because many SMT patch processing is urgent work, these details that need to be prepared in advance should be taken into account as soon as possible, so as to ensure the efficiency of the whole processing process and reduce the waste of resources.
2. What is the high cost in PCBA processing?
In order to understand the high cost of PCBA processing, we need to decompose the whole process of PCBA manufacturing and material contracting. PCBA (PCB Assembly) means PCB assembly, which must include circuit board light plate and component welding (SMT mounting /DIP plug-in post welding). At present, the price of light board in the market is between 350 and 550, and the price of components is basically open and transparent in major shopping malls, which can be compared for reference.
Since the main PCB circuit boards and components are not the possibility of price increases, so the cost is reflected in the link of assembly. The main cost of this link is in the following four aspects:
1, auxiliary materials: tin paste, tin strip, flux, UV glue, furnace fixture
The quality of solder paste and solder strip is the most important auxiliary material in the whole processing link, generally domestic solder paste price in 180~260/ bottle, imported solder paste may be in 320~480/ bottle, then the same welding area, the price of imported solder paste is much higher, but the quality of welding difference is very obvious.
2. smt patch processing
Patch processing according to the number of points and packaging, there will be a certain difference in price. Large quantity and high price is the consensus of the industry, the larger the component package size, the easier to mount, the corresponding bad quality will be reduced, so the price also has greater room for communication.
3, DIP plug-in after welding hours
Plug-in material link because it involves special-shaped parts and material molding, this link needs a lot of manual participation, because there is no production capacity reference of machinery and equipment, this link is the most difficult to control the cost of the link. At the same time, the labor cost is high, and the cost of this link is generally high.
4. Assembly test: test fixture, test equipment and test man-hour
The test fixture currently varies from dozens to hundreds of yuan according to the difficulty of the test, and the test of communication equipment also needs optical fiber, ICT and other test equipment assistance, the corresponding manual and equipment loss need to be taken into account, but not very high, some companies and even the test is free.
Shenzhen kingford SMT processing capacity
1. Maximum board card: 310mm*410mm(SMT);
2. Maximum plate thickness: 3mm;
3. Minimum plate thickness: 0.5mm;
4. Minimum Chip parts: 0201 package or parts above 0.6mm*0.3mm;
5. Maximum weight of mounted parts: 150g;
6. Maximum parts height: 25mm;
7. Maximum parts size: 150mm*150mm;
8. Minimum spacing of pin parts: 0.3mm;
9. Minimum ball parts (BGA) spacing: 0.3mm;
10. Minimum ball parts (BGA) ball diameter: 0.3mm;
11. Maximum parts mounting accuracy (100QFP) : 25um@IPC;
12. Patch capacity: 3-4 million points/day.
Why do you choose Shenzhen kingford to do PCBA proofing?
1. Strength guarantee
▪SMT workshop: We have imported SMT machines and several sets of optical inspection equipment, with a daily output of 4 million. Each process is equipped with QC personnel, who can keep an eye on product quality.
▪DIP production line: We have two wave-soldering machines, among which there are more than 10 old employees who have worked for more than three years. The skilled workers can weld all kinds of plug-in materials.
2. Quality assurance, cost-effective
▪ High-end equipment can stick precision shaped parts, BGA, QFN, 0201 materials. Can also template patch, loose material hand.
▪ Sample and size batch can be produced, proofing from 800 yuan, batch 0.008 yuan/point, no start-up fee.
3. Rich experience in SMT and welding of electronic products, stable delivery
▪ Accumulated SMT SMT processing services for thousands of electronic enterprises, involving many kinds of automotive equipment and industrial control motherboard. The products are often exported to Europe and the United States, and the quality can be affirmed by new and old customers.
▪ On time delivery, normal 3-5 days after complete materials, small batch can also be expedited on the same day shipment.
4. Strong maintenance ability and perfect after-sales service
▪ Experienced maintenance engineers can repair all kinds of patch welding caused by bad products, to ensure the connection rate of each piece of circuit board.
▪ 24-hour customer service staff at any time response, the fastest speed to solve your order problems.