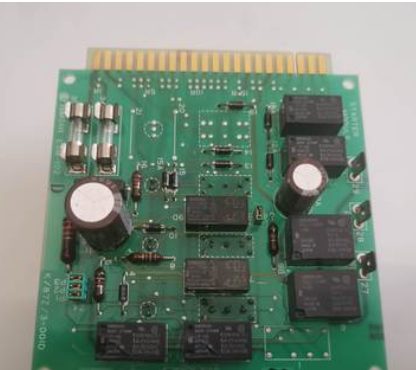
Material loss in SMT patch processing has always been one of the key controls of production management personnel, and it is also a problem that needs continuous improvement. Although the industry has been developed for decades, there are still many aspects that need to be improved and controlled. Especially in today's increasingly fierce competition, the control of material loss is particularly important. Next, Shenzhen PCBA manufacturer - Shenzhen kingford will share with you the common causes and solutions of material loss in SMT patch processing.
First, human factors
1. When installing materials, the tearing belt is too long and the pressing material is too much, resulting in material loss and loss;
Solution: Train the operator to keep two or three slots when loading, press the material to the material window to see the material is OK, so you can check the position of the FEEDER gear and the tension of the coil.
2. After installation of FEEDER, there is debris on the TABLE causing not in place, shaking can not get material;
Solution: Train the operator to check whether there are sundries on the machine TABLE and FEEDER base when installing FEEDER, and clean the machine TABLE when pulling.
3, the material tray is not installed on the FEEDER, resulting in chuck, FEEDERTAPE floating high throwing material;
Solution: Strictly require the operator when refueling must put the tray on the FEEDER.
4, not timely remove the winding tape resulting in tension change, no winding, poor feeding, FEEDERTAPE floating high throwing material;
Solution: The operator must be strictly required to clean the coil when refueling.
5, put back plate, jump wrong plate, wipe plate and other loss;
Solution: Strictly require the operator to operate according to the operation instruction, and mark the position of the assembly board, the direction of entering the board and the precautions in the instruction book.
6. Wrong material position and P/N caused by wrong material;
Solution: Train the operator to check the material P/N and machine alarm display, discharge table station position.
7. Wrong quantity of materials, too much PCBA, missing tray of materials by mistake;
Solution: It is required that all materials and PCBA in and out of the production line must count the quantity and register on duty to check the production quantity and pull quantity.
8. Packaging parameters are not set correctly in the edited program, and the feeding times used are not consistent with the packaging PITCH, resulting in material throwing;
Solution: Modify PACKEDDATA according to material packaging.
9. Incorrect setting of mounting position and station position in the edited program resulted in incorrect materials;
Solution: Check the BOM and drawings when doing the program, and re-check the BOM and drawings when pasting the first inspection board.
10. FEEDER, NOZZLE and material causes in the production process. Nozzle technicians do not follow up the material disposal and nozzle data, resulting in a large amount of material disposal;
Solution: It is required that the line following technician must monitor the running condition of the machine in real time, and the machine alarm must be handled and observed on site. Technicians must sign, confirm and write improvement measures on the hourly throwing report. If the report is not processed within two hours after signature confirmation, the reasons must be analyzed and reported to the assistant engineer for handling.
11. Don't buckle the Feeder cover and feed without checking the Feeder
Solution: Ask operator to follow WI requirements and check FEEDER before and after installation. Technician and management check and confirm.
12, FEEDER easily stacked deformation, FEEDERSTOPPER easily disassembled disorderly;
Solution: All FEEDER must be placed on the FEEDER car, and it is strictly prohibited to stack or unarrange them.
13. Defective FEEDER is not sent for maintenance and reuse in time, resulting in material throwing;
Solution: All bad feeders must be clearly marked and sent to the FEEDER maintenance station for maintenance and correction.
Second, machine factors
1, suction nozzle deformation, blockage, damage, insufficient vacuum pressure, air leakage, resulting in suction can not afford, take material is not correct, identification through and throwing material.
Solution: NOZZLE requires a technician to inspect the device every day, test the center, clean the nozzle and nozzle as planned.
2, the spring tension is not enough, the suction nozzle and the HOLD is not coordinated up and down, resulting in poor material taking;
Solution: Maintain equipment regularly according to plan, check and replace vulnerable parts.
3, HOLD/SHAFT or PISTON deformation, bent suction nozzle, suction nozzle wear becomes short resulting in poor take-up;
Solution: Maintain equipment regularly according to plan, check and replace vulnerable parts.
4, take the material is not in the central position of the material, take the material height is not correct (generally meet the parts after pressing 0.05MM) and caused by offset, take the material is not correct, there is deviation, identification with the corresponding data parameters do not conform to the identification system as invalid material abandoned;
Solution: Maintain the equipment regularly according to plan, check and replace the vulnerable parts, and correct the origin of the machine.
5. The vacuum valve and vacuum filter element are dirty, and the vacuum pipe channel is not smooth if there are foreign bodies blocking it. When sucking, the vacuum is not enough to run at the speed of the equipment, resulting in poor material taking.
Solution: Technicians must clean the nozzle every day and maintain the equipment regularly as planned.
6, the machine positioning is not horizontal vibration, the machine and FEEDER resonance caused by bad material;
Solution: Maintain the equipment regularly according to plan and check the horizontal fixing support nuts of the equipment.
7. Lead screw and bearing wear loose, resulting in vibration and stroke change during operation and poor material taking;
Solution: It is strictly prohibited to blow inside the machine with air gun to prevent dust, debris and components from adhering to the screw. Maintain equipment regularly according to schedule, check and replace vulnerable parts.
8, motor bearing wear, reader and amplifier aging caused by machine origin change, running data is not accurate and poor material;
Solution: Maintain the equipment regularly according to plan, check and replace the vulnerable parts, and correct the origin of the machine.
9, vision, laser lens, suction nozzle reflective paper is not clean, there are debris interference camera identification resulting in poor processing;
Solution: NOZZLE requires a technician to inspect the device every day, test the center, clean the nozzle and nozzle as planned.
10, identification light source selection, lamp aging luminous intensity, gray level is not enough to cause poor treatment;
Solution: Maintain the equipment regularly according to the plan, test the brightness of the camera and the brightness of the lamp, check and replace the vulnerable parts.
11, reflective prism aging carbon accumulation, wear and scratch caused by poor treatment;
Solution: Maintain equipment regularly according to plan, check and replace vulnerable parts.
12, insufficient air pressure, vacuum leakage caused by insufficient air pressure can not afford to take material or pick up after falling on the way to paste;
Solution: Maintain equipment regularly according to plan, check and replace vulnerable parts.
13, the feeder gland deformation, spring tension is not enough to cause the material belt is not stuck on the spine gear of the feeder, no roll belt throwing material;
Solution: All bad feeders must be clearly marked and sent to the FEEDER maintenance station for maintenance, correction, inspection and replacement of vulnerable parts.
14, the camera loose, aging caused by poor identification of throwing material;
Solution: Maintain equipment regularly according to plan, check and replace vulnerable parts.
15, the feeder spine gear, driving claw, positioning claw wear, electrical poor, poor feeding motor caused by the feeder feed is not free to take material or poor throwing;
Solution: All bad feeders must be clearly marked and sent to the FEEDER maintenance station for maintenance, correction, inspection and replacement of vulnerable parts.
16, the machine feeding platform wear caused by the installation of the FEEDER loose and poor feeding;
Solution: Maintain equipment regularly according to plan, check and replace vulnerable parts.
Iii. Material reasons
1. Components dirty, damaged, irregular incoming materials, pin oxidation and other unqualified products cause poor identification.
Solution: Feedback IQC and communicate with supplier to replace materials.
2, component magnetization, component packaging is too tight, material frame on the component friction force is too large to suck up.
Solution: Feedback IQC and communicate with supplier to replace materials.
3. Component size or package size, spacing and direction are inconsistent, resulting in poor material taking and poor identification.
Solution: Feedback IQC and communicate with the supplier to replace the material. When receiving the material, it must check the packaging and body shape of the same P/N material.
4, component magnetization, material tape viscosity is too strong, coil tape material adhesion to the material belt.
Solution: Feedback IQC and communicate with supplier to replace materials.
5. The suction surface of the component is too small to cause bad material taking.
Solution: Feedback IQC and communicate with the supplier to replace the material and reduce the machine running speed.
6. The material aperture of the holding component is too large, and the component size does not match the packaging size, resulting in the side stand, turn over, the position is not right and the material is not good.
Solution: Feedback IQC and communicate with supplier to replace materials.
7. The error between the feeding hole and the feeding hole of the material belt is large, and the absorbing position changes after refueling
Solution: Feedback IQC and communicate with supplier to replace materials.
8, winding material belt tension, too soft easy to elongate the tape; Too brittle easy to break to get material.
Solution: Feedback IQC and communicate with supplier to replace materials.
9. The packaging of incoming materials is not standard, and the bulk cannot be mounted by machine.
Solution: Feedback IQC and communicate with supplier to replace materials.
Four, operation method
1. Using wrong packing FEEDER, notches for paper tape and flat grooves for tape, resulting in no materials to be obtained;
Solution: Train operators to identify material packaging and FEEDER selection.
2. Wrong FEEDER of different sizes, 0802FEEDRE for 0603 material, 0804FEEDER for 0402 material, Ø1.3MM cover for 0603 material, Ø1.0MM cover for 0402 material and Ø1.0MM cover for 0805 material, and incorrect FEEDERPITCH resulted in no material being obtained;
Solution: Train operator to identify material size, shape and FEEDER cover selection.
3. Personnel do not operate according to the operating instructions.
Solution: Strict requirements according to the operation instruction standard operation, regular assessment of operating skills, management, supervision and evaluation.
4, poor feeding, material belt bending, winding belt tension is too tight, material belt hole on the gear caused by poor fetching;
Solution: Strict requirements according to the operation instruction standard operation, training assessment skills, management supervision evaluation.
5, the winding belt tension is not enough, not according to the standard installation of the winding belt caused by no winding;
Solution: Strict requirements according to the operation instruction standard operation, training assessment skills, management supervision evaluation.
6. Empty space after material installation leads to unavailability of materials;
Solution: Strict requirements according to the operation instruction standard operation, training assessment skills, management supervision evaluation.
5. Production environment
1, workshop temperature is high, humidity is not enough to cause the material dry dust, static electricity.
Solution: real-time monitoring workshop temperature and humidity, add air conditioning and humidifier.
2, workshop, warehouse humidity is high, materials absorb the water in the air resulting in poor material taking
Solution: real-time monitoring workshop, warehouse temperature and humidity, increase air conditioning and ventilation equipment.
3, workshop sealing is not good, poor dust facilities, too much dust caused by the machine is easy to dirty, vacuum blocking.
Solution: It is strictly prohibited to use air gun to blow machine electrical facilities, materials, workshop door to increase carpet dust removal.
4. The charging platform and FEEDER car are not enough, resulting in non-standard charging and FEEDER damage and deformation.
Solution: Add charging table and FEEDER car, and operate strictly according to WI requirements.
The above is the introduction of common causes and solutions of material loss in SMT patch processing. I hope it will be helpful to you. If you need to do PCBA OEM for electronic products, please contact kingford testing engineer!