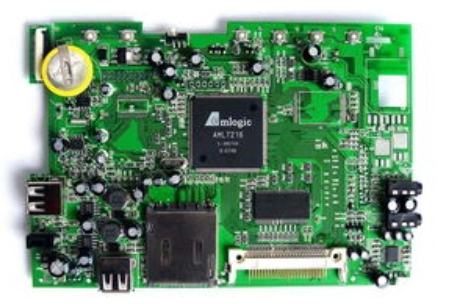
It is well known that the basic properties of printed circuit boards (PCBS) depend on the properties of their substrate materials. Therefore, to improve the performance of the circuit board, the performance of the substrate material must be optimized first. To date, many new types of materials are being developed and put into use in order to meet the requirements of adapting to new technologies and market trends.
The market for printed circuit boards has shifted in recent years from traditional hardware products such as desktop computers to wireless communications such as servers and mobile terminals. Mobile communication devices represented by smart phones promote the development of PCB to the direction of high density, lightweight and multifunctional. Without the substrate material, whose technical requirements are closely related to the performance of the PCB, it is impossible to realize the printed circuit technology. Therefore, the selection of substrate materials plays a crucial role in improving the quality and reliability of PCB and its final products.
How to determine the PCB substrate material?
Meet the requirements of high density and thin wire
- Requirements for copper foil
All PCB boards are moving towards higher density and thinner wires, especially HDI PCBS (High density Interconnected PCBS). Ten years ago, HDI PCBS were defined by IPC as PCBS with line width (L) and line spacing (S) of 0.1mm or smaller. At present, however, the standard values of L and S in the current electronics industry can be as small as 60μm, and in advanced cases, they can be as low as 40μm.
Traditional circuit pattern formation methods lie in imaging and etching processes, resulting in a minimum L and S of 30μm with thin copper foil substrates (in the 9μm to 12μm thickness range).
Because of the high cost, high stacking, and high defect characteristics of thin copper-covered copper sheets (CCLS), many PCB manufacturers prefer to use etching and reducing copper foil instead of copper foil thickness of 18μm. This approach is not actually recommended because it involves too many processes, and the thickness is difficult to control, resulting in higher costs. As a result, thinner copper foil is better. In addition, standard copper foil does not work when the plate's L and S values are less than 20μm. Finally, the use of ultra-thin copper foil is recommended, as the copper thickness should be controlled in the range of 3μm to 5μm.
In addition to the thickness of copper foil, current fine circuits also require a low roughness copper foil surface. In order to improve the bonding ability between copper foil and base material and ensure the peeling strength of conductor, the copper foil plane is roughened. The roughness of ordinary copper foil is greater than 5μm.
The copper foil is embedded with a bump into the substrate material to improve its peeling strength. However, in order to control lead accuracy away from excessive etching during circuit etching, it tends to cause hump contamination, which may lead to short circuits or reduced insulation between the lines, especially affecting fine circuits. Therefore, copper foil with low roughness (less than 3μm or even 1.5μm) is required.
Although the roughness of the copper foil is reduced, it is still necessary to maintain the peeling strength of the conductor. This causes special surface molding on the surface of the copper foil and the base material, which will help to ensure the peeling strength of the conductor.
- Requirements for insulating dielectric laminates
One of the main technical features of HDI PCBS is the build process. Lamination of commonly used RCC (resin-coated copper) or prepreg epoxy glass cloths and copper foils rarely results in fine circuits. The current preference is to use SAP and MSPA, which means laminating an insulating dielectric film with electroless copper plating to produce a copper conducting plane. Because of the thin copper plane, fine circuits can be produced.
One of the key points of SAP is a layer of piezoelectric dielectric material. In order to meet the requirements of high density fine circuits, a number of requirements must be made for laminate materials, including dielectric properties, insulation, heat resistance capacity and adhesion, as well as technical adaptability compatible with HDI PCBS.
In semiconductor packaging worldwide, IC packaging substrates have been converted from ceramic substrates to organic substrates. The pitch of the FC packaging substrate is becoming smaller, so the current typical value of L and S is 15μm and will be smaller.
The performance of multilayer substrate should emphasize low dielectric properties, low thermal expansion coefficient (CTE) and high heat resistance, which refers to the low cost substrate that meets the performance objectives. Today, through the mass production of fine circuits, MSPA technology is applied to combine layers of insulating dielectric with thin copper foils. SAP is used to manufacture circuit patterns with both L and S values less than 10μm.
The high density and thinness of PCBS cause HDI PCBS to change from laminating with core to any layer without core. For HDI PCBS with the same function, PCB with interconnect function at any layer has 25% less area and thickness than PCB with core layer. Both HDI PCBS must use a thinner dielectric layer with better electrical properties.
From high frequency and high speed demand
Electronic communication technology has developed from wired to wireless, from low frequency and low speed to high frequency and high speed. Smartphone performance has been upgraded from 4G to 5G, requiring faster transmission speeds and larger volumes.
The advent of the global cloud computing era leads to the doubling of data traffic, and the trend of high frequency and high speed communication equipment is obvious. In order to meet the requirements of high frequency and high speed transmission, high performance materials are the most important elements, in addition to reducing signal interference and consumption, signal integrity and manufacture compatible with the design requirements of PCB design.
The engineer's main job is to rely on the properties of electrical signal loss to improve PCB speed and deal with signal integrity issues. Based on over ten years of PCB manufacturer manufacturing services, as a key factor influencing substrate material selection, it is considered an intermediate Dk/Df laminate when the dielectric constant (Dk) is less than 4 and the dielectric loss (Df) is less than 0.010, and a low Dk/Df laminate when the Dk is less than 3.7 and the Df is less than 0.005. Currently, there are many types of substrate materials available on the market.
So far, the commonly used HF circuit board substrate materials mainly include the following three kinds: fluorine resin, PPO or PPE resin and modified epoxy resin. Fluorine series dielectric substrates with the lowest dielectric properties (e.g. PTFE) are usually used for products with frequencies of 5GHz or higher. Modified epoxy FR-4 or PPO substrates are suitable for products in the frequency range of 1GHz to 10GHz.
Compared with these three types of high-frequency substrate materials, the price of epoxy resin is the lowest, and the price of fluorine series resin is the highest. In terms of dielectric constant, dielectric loss, water absorption and frequency characteristics, fluorine resin showed the best performance, while epoxy resin showed poor performance. When the product applied frequency is higher than 10GHz, only the fluorine series resin works. The disadvantages of PTFE include high cost, poor rigidity and high coefficient of thermal expansion.
For PTFE, bulk inorganic material (e.g. Silica) can be used as a filling material or glass cloth to enhance the rigidity of the substrate and reduce the coefficient of thermal expansion. In addition, it is necessary to achieve special surface forming compatible with copper foil because the inert nature of the polyfluoroethylene molecule makes it difficult for the polyfluoroethylene molecule to bond with copper foil. The treatment involves chemically etching the surface of polyethylene to increase surface roughness, or adding a bonding film to increase adhesion. With the application of this method, the dielectric properties may be affected, and the whole fluorine series high-frequency circuit must be further developed.
A unique insulating resin consisting of modified epoxy resin or PPE combined with glass cloth TMA, MDI and BMI has been used more frequently. Similar to the FR-4 CCL, it also has excellent heat resistance and dielectric properties, mechanical strength, and the manufacturability of PCBS, all of which make it more popular than PTFE-type substrates.
In addition to the requirements on the performance of insulating materials such as the above resin, the surface roughness of copper as a conductor is also an important factor affecting the signal transmission loss, which is the result of skin effect. In short, the skin effect is that the electromagnetic induction and inductance generated by the wire in high-frequency signal transmission become so concentrated in the center of the wire cross-sectional area that the driving current or signal is concentrated on the surface of the wire. The surface roughness of conductor plays a key role in the loss of transmission signal, and the loss caused by low roughness is very small.
High surface roughness of copper results in high signal loss at the same frequency. Therefore, the roughness of the surface copper must be controlled in the actual manufacturing, and it should be made as low as possible without affecting the adhesion. Special attention must be paid to signals in the frequency range of 10 GHz or higher. The roughness of copper foil should be less than 1μm, and it is better to use ultrapurface copper foil with a roughness of 0.04μm. The surface roughness of copper foil must be combined with proper oxidation treatment and bonding resin system. In the near future, there may be a copper foil shape that is not coated with resin, and that has higher peel strength and does not affect dielectric loss.
High heat and heat dissipation requirements
With the development trend of miniaturization and high function, electronic equipment tends to generate a lot of heat, so the thermal management requirements of electronic equipment are increasingly high. One of the ways to solve this problem is the research and development of thermal conductive PCB. The main conditions for the good heat resistance and heat dissipation of PCB are the heat resistance and heat dissipation of the substrate. Current improvements in PCB thermal conductivity have been made through the addition of resins and fillers, but only in limited categories. Typical methods are IMS or metal core PCBS that act as heating components. Compared with traditional radiators and fans, this method has the advantages of small size and low cost.
Aluminum is a very attractive material with abundant resources, low cost, excellent thermal conductivity and strength. In addition, it is very environmentally friendly and can be used on most metal substrates or cores. Due to its economic, reliable electrical connection, thermal conductivity and high strength, solder - and lead-free advantages, aluminum based circuit boards have been used in consumer products, automotive, military products and aerospace products. There is no doubt that the heat resistance and heat dissipation of the metal substrate is the key, the key lies in the adhesion between the metal plate and the circuit board.
How to determine the PCB substrate material?
In the modern electronic age, the miniaturization and thinness of electronic equipment lead to the necessity of rigid PCB and flexible/rigid PCB. So what type of base material is suitable for them?
The increasing applications of rigid PCB and flexible/rigid PCB put forward new requirements in terms of quantity and performance. For example, polyimide membranes can be divided into a number of categories, including transparent, white, black and yellow with high heat resistance and low thermal expansion coefficient, in order to be applied in different situations. Similarly, highly cost-effective polyester film substrates have been accepted by the market for their high elasticity, dimensional stability, film surface quality, photoelectric coupling and environmental resistance to meet the variable needs of users.
Similar to rigid HDI PCB, flexible PCB must adapt to high speed and high frequency signal transmission requirements, the dielectric constant and dielectric loss of flexible substrate materials must also be paid attention to. Flexible circuits may be composed of teflon and advanced polyimide substrates. Inorganic dust and carbon fiber can be added to the polyimide resin to produce three layers of flexible thermal conductivity substrate. Inorganic filling materials can be aluminum nitride, alumina or hexagonal boron nitride. This type of substrate material has thermal conductivity of 1.51W/mK and is resistant to a voltage of 2.5kV and a curvature of 180 degrees.
Flexible PCBS are mainly used in smart phones, wearable devices, medical devices and robotics, which puts forward new requirements for flexible PCB structures. So far, some new products containing flexible PCBS have been developed, such as ultra-thin flexible multilayer PCBS, whose thickness is reduced from 0.4mm to 0.2mm. By using polyimide substrate materials with low Dk and Df, transmission speeds of 5Gbps can be achieved with high speed transfer flexible PCBS. High power flexible PCB adopts conductor with thickness greater than 100μm to meet the requirements of high power and high current circuit. All of these special flexible PCBS naturally lead to unconventional substrate materials.
PCB board/circuit board manufacturer
kingford is a circuit board manufacturer specializing in the manufacture of printed circuit boards, specializing in the production of single, double-sided and multi-layer circuit boards. We can provide PCB proofing and mass production services such as FR4 hard board, FPC soft board, HDI board and metal substrate.