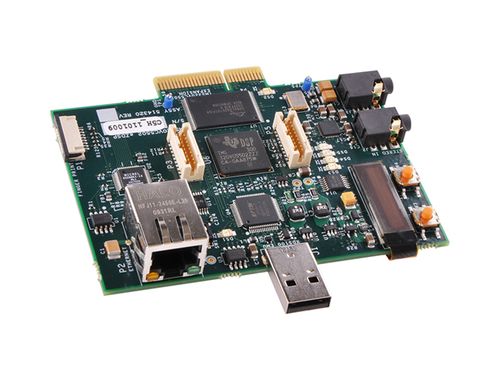
There are many procedures to be paid attention to in SMT patch processing, especially solder paste printing. But there are a lot of issues that are important but not being noticed. However, the purpose of substrate positioning is to make the solder paste press can automatically identify the corresponding position of the template and PCB pad, so that the position of the printing window of the template is corresponding to the graphic position of the PCB pad, and finally make the solder paste can be accurately printed on the PCB board. Substrate positioning methods include hole positioning, side positioning, and straight - space positioning.
First, the process analysis of PCB substrate positioning
When SMT double-sided PCB adopts hole positioning, it is necessary to pay attention to all kinds of thimbles when printing the second side, which should avoid the components that have been pieced and processed, and do not top on the components to prevent the components from damage.
Good substrate positioning should meet the following basic requirements: easy to place and remove, no raised printing surface objects, maintain the stability of the substrate throughout the printing process, maintain or assist to improve the flatness of the substrate printing, does not affect the template to solder paste release action.
After the positioning of the substrate, the pattern alignment should be carried out, that is, through fine adjustment of x, y, θ of the printing work platform or template, so that the PCB solder pad pattern and the template hole pattern completely coincide. Whether to adjust the table or the template, depending on the construction of the press. Most of the printing presses are fixed, this way of printing precision is relatively high.
Note that the direction of the PCB circuit board is consistent with the pattern of leaky holes on the template, and the contact height between the PCB and the template should be set. Ensure that the pattern of the PCB solder pad coincides with the pattern of leaky holes on the template. When aligning the pattern, it is generally adjusted first, so that the PCB solder pad pattern is parallel to the template leaky pattern, and then adjusted x and y, and then repeated the fine adjustment until the PCB solder pad pattern and the template leaky pattern completely coincide.
Two, the reliability of the hole in circuit board processing
The influence of SMT holes on reliability is more complex, especially the location, size and quantity of holes under tin and lead solder have different effects on the reliability of solder joints of different structures. The industry has not yet reached a clear conclusion. There is only one acceptance criterion for voidage in BGA solder joints in IPC standard. Therefore, the acceptability of voidage in BGA solder joints in smt process is mainly discussed here.
Reliability studies of BGA solder joints indicate that a small size cavity may also be beneficial to solder joint reliability by preventing crack expansion. However, voillage at least reduces the thermal conductivity and flow capacity of the PCB substrate. In this regard, voillage adversely affects the reliability of the BGA and directly leads to the reduction of the through-through rate in the PCBA one-stop process.
1. Before discussing the acceptable conditions of voids for BGA solder joints, we should first understand the types of voids in BGA solder joints.
Macrovoid: This is the most common void phenomenon in SMT patch processing, caused by the flux trapped in the solder volatilization. Such voids generally have no effect on reliability unless they are distributed near the interface.
2. Planar Microvoid: a series of small cavities are located between the solder and PCB pad interface. These cavities are caused by the Cu holes under the surface of lm-Ag. They do not affect the early reliability of solder joints, but will affect the reliability of long-term PCBA processing. Im-Ag coating, although it is a precious metal, but also prone to cavity, which is related to the coating contains organic matter. Typically, Im-Ag coatings may contain up to 30% organic impurities. When the coating is as thin as 0.2um(0.8mil), the silver will dissolve into the solder within a few tenths of a second, and there is basically no organic residue in the solder joints during patch processing. However, if the coating is relatively thick, it will not completely dissolve the solder, and the organic impurities remaining in the silver coating during reflow welding will decompose and discharge the gas, forming a dense interfacial cavity phenomenon, that is, champagne cavity.
3. The influence of PCB surfacelayer on voids is mainly related to wettability. The better wettability is, the less voids are. In general, the general tendency of the coating to produce holes is OSP(maximum) > non-precious metals > precious metals (minimum). SMT factories are usually more effective at reducing voids by improving wettability than by increasing the soldering capacity of flux.
4. PCB welding resistance is typically defined by the void phenomenon caused by the blind hole of the welding pad and the seal. Closed air or volatilization of residual organic impurities may lead to the void.
5, solder joint area, the larger the pin width, the higher the hole.