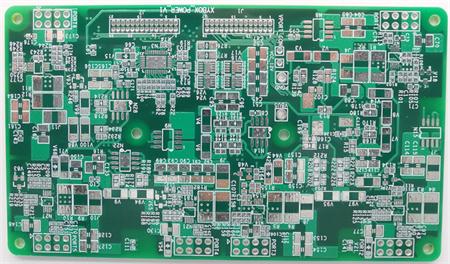
PCB is one of the most common electronic components at present, and almost all electronic products will use PCB.
PCB is widely used in electronics, computers, electrical appliances, mechanical equipment and other industries. It is the support of components and is mainly used to connect components to provide electrical. Among them, the most common and widely used are 4-layer and 6-layer PCB. Different levels of PCB layers can be selected according to industry applications.
Printed circuit board (PCB): also known as printed circuit board, printed circuit board (PCB for short), or printed circuit board (PWB for short). With insulating board as the base material, it is cut into a certain size, at least one conductive pattern is attached to it, and holes (such as element holes, fastening holes, metallization holes, etc.) are arranged on it, which is used to replace the chassis of electronic components of previous devices, and realize the interconnection between electronic components. Because this kind of board is made by electronic printing, it is called "printed" circuit board. It is not accurate to call "printed circuit board" as "printed circuit", because there is no "printed component" on the printed circuit board but only wiring.
PCB is an important electronic component and the support of electronic components. The automatic soldering machine provides technical support for the soldering of PCB, making the development of electronic components progress. However, the problem that the PBC circuit board is corroded has been puzzling the automatic soldering merchants.
PCB corrosion method:
One time corrosion solution can generally corrode multiple circuit boards at one time. The corrosion solution is generally prepared by adding ferric chloride and water. The ferric chloride is a yellowish yellow solid, which is also easy to absorb water in the air, so it should be sealed for storage.
PCB corrosion steps:
After the corrosion solution is configured, the PCB shall be corroded from the edge. When the copper foil without carbon powder is corroded, the circuit board shall be taken out in time to prevent the carbon powder from falling off and corroding the useful circuit.
After taking out the corroded circuit board, wash it with clean water, and polish the carbon powder with fine sandpaper. Then it was wiped dry, and the shiny copper foil was exposed, completing the production of the circuit board.
Finally, in order to better preserve the PCB, the polished PCB is usually coated with rosin solution, which can not only facilitate welding, but also prevent oxidation.
What is the corrosion process of PCB:
Corrosion solution is usually prepared with ferric chloride and water. Ferric chloride is a yellowish solid, which is also easy to absorb water in the air, so it should be sealed for preservation. When preparing ferric chloride solution, generally 40% ferric chloride and 60% water are used. Of course, more ferric chloride is used, or warm water (not hot water, to prevent paint from falling off) can make the reaction faster. Note that ferric chloride has a certain corrosivity. Try not to touch skin and clothing. The reaction container should be a cheap plastic basin, which can fit the circuit board.
The PCB is corroded from the edge. When the copper foil without paint is corroded, the PCB should be taken out in time to prevent the useful circuit from being corroded after the paint falls off. At this time, wash with clean water, and scrape off the paint with bamboo chips (the paint comes out of the liquid, which is easier to remove). If it is not easy to scratch, just rinse it with hot water. Then it is wiped dry and polished with sandpaper to reveal shiny copper foil. A printed circuit board is ready. In order to preserve the achievements, the polished PCB is usually coated with rosin solution, which can not only facilitate soldering, but also prevent oxidation.