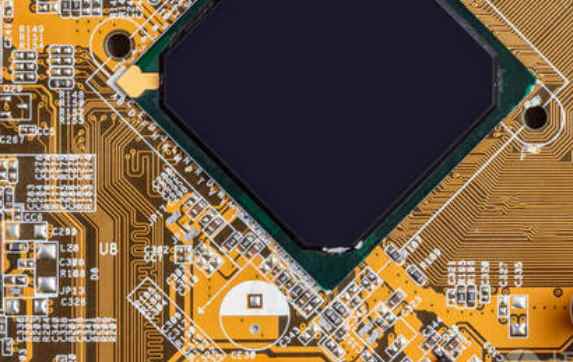
Systems operating at high currents or voltages face a unique set of challenges that are not seen in smaller digital systems. Operators may be exposed to unsafe conditions, and designs may fail due to heat or electrostatic discharge. However, proper PCB design decisions can help reduce the risks involved in interacting with power electronics. In this guide, we will cover some basic design points to consider in high current board design. In some cases, the layout and safety considerations involved in high-current board design are similar to those in high-voltage design, especially when we consider safety.
High current circuit board layout basics
There are some good examples of high current PCB designs that do not necessarily operate at high voltages. Moreover, the concept of "high voltage" versus "high current" is somewhat arbitrary. A better metric that distinguishes these types of designs may be security. If the DC current poses a risk of shock or overheating, you may need to apply some of these design principles to ensure safety and reliability.
Component selection
High-current designs and power systems typically derive most of their reliability from components. Although it sounds obvious, be sure to consider the component's safety margin during selection. In general, it is recommended to look at two specifications first:
Current rating, especially MOSFETs and inductors
Thermal resistance value (if any)
You can use the estimated or designed operating current to determine the power consumption, or use the first specification above to get the value for the worse case. Both help with thermal management, which requires the use of thermal resistance values to estimate temperature. For some components, you can determine if a radiator is needed to ensure reliability.
Other components that are important for high-current circuit boards (such as connectors) may have very high ratings and be very useful in power systems. Two examples of mechanical screw terminal connectors that can handle very high currents are shown below.
Choose the right weight of copper
The resistance of the copper used in the wiring causes some DC power loss, which is lost as heat. This becomes important for very high current designs, especially when the component density is high. The way to prevent DC losses in high-current PCBS is to use copper with a larger cross-sectional area. This means that either heavier copper or wider wiring is needed to keep joule heat and power losses low enough. Use a PCB wireline width and ammeter to determine the copper weight and/or wireline width required to prevent excessive temperature rise.
Get bigger: Use planes instead of tracks
If you must feed very high current into the power system and the wiring is too wide to meet your needs, use the power layer instead of the wiring. For example, in the Eurocard format backplane we did in the past, we used multiple power layers to supply 100 A of current from two dedicated low-voltage (24 V) power supplies. You can use the same strategy in other systems when you need to support extreme currents.
Copper-covered heat sink
In a board housing with stagnant air, it is difficult to transfer heat away from the device if you rely solely on conduction or natural convection. Hot through-holes can be placed on boards with copper on the surface layer to provide additional heat transfer away from certain components by providing a direct connection to the flat layer (GND). This can be used in circuits close to the thermal element or in wiring to provide additional heat conduction away from the surface layer, but should not be used in situations where isolation is required, such as between the primary and secondary turns of a power transformer.
While heat sink holes are good for targeting specific components, a better strategy is to consider how to use large heat sinks or direct conduction paths to the housing to provide high heat dissipation. An example of a set of parallel MosFeTs is shown below.
Watch the ground
High current systems may require the same type of fail-safe measures. A certain degree of safety and EMI can be achieved through proper grounding strategies. Typically, you should not split ground, but power systems involving high currents and/or high voltages are an exception. Grounding needs to be separated between input AC, unregulated DC, and regulated DC parts.
A good starting point is the grounding policy in an AC system or isolated power supply. Typically, for a high-current power supply system, you will have a 3-wire DC arrangement (PWR, COM, GND) where the GND connection is actually a ground connection. Your board may use an isolation policy where the output side is disconnected from GND and the input side is grounded to ensure safety in the event of a failure.
Use thicker circuit boards