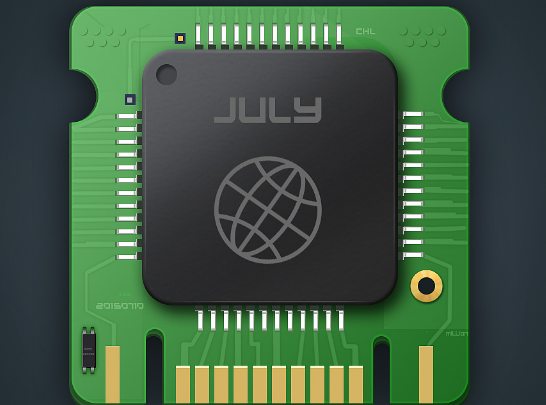
Important points:
● What are the different types of test points used on printed circuit boards?
● Why are PCB test sites important for successful PCB manufacturing?
Just mention the word "test" and most people will feel their hearts racing. From the first day of primary school, there seems to be a fear of exams. But, as we all know, testing is a very important part of life. You don't want to fly in an airplane with a pilot who has failed a flight check, and the idea of a surgeon brandishing a scalpel without passing his basic anatomy course scares everyone.
The circuit board we designed also had to pass some tests. In their case, the test will determine their manufacturing quality. In order to perform this test, the board must be prepared with specific elements that the test probe can access. These elements are called test points and it is important that they are included in the PCB design. Let's take a few minutes here to discuss the PCB test point and why it is so important to the success of the completed board.
Different types of PCB test points
There are two main types of test points used on printed circuit boards. The first is a point easily accessible to technicians using handheld test equipment. To solve this problem, a terminal is usually welded to these points to clamp the test lead. These test points will be marked with a reference mark, usually with a screen name in silkscreen printing for easy reference, such as "GND".
Another type of test point is mainly used for automated test equipment. Automatic test points on the circuit board are through-hole pins, through-holes or small metal pads designed to hold the probes of the automated test system. There are three main test systems that will use these test points on the board:
● Bare board test: This is a test conducted after the board is manufactured to ensure that all the networks on the board have electrical connectivity.
● Online test: run ICT after assembling the circuit board. The board is located on an ICT fixture that contains probes for each individual network. These fixtures usually test the bottom of the board, but they can also work together to test the top or sides of the board if needed.
● Fly Pin: As with ICT, this test is performed on each net on the board after assembly by accessing the test points. The difference, however, is that the flying needle device uses two to six probes that can be moved to each test point, rather than a fixed probe in a fixed device as is the case with ICT.
These are the different test points that will be included in the PCB design and their purpose. Next, we'll see why this test is so important for board manufacturing.
Why are test points important for PCB manufacturing
Automated testing is essential to validate the manufacture of printed circuit boards. The bare board test will check that the wood-based board has good connectivity, while the ICT and fly pin tests will verify the board assembly and welded connections.
Operational applications of ICT and flight probe testing:
Online testing (ICT)
ICT is a system that uses a test fixture specifically prepared for a particular board design and accompanying software that will run on the test system. The fixture and software are created using test point locations and other design data generated from the CAD database, and a probe will be used for each network in the design. The main purpose of ICT is to verify the assembly of the board by testing the good connection of each network to the pins of its associated parts, but it can also be used to test the functionality of the board.
ICT testing equipment and software development is costly and time consuming. Test fixtures are complex, containing thousands of probes, and expensive to change for board revisions. However, once the development is complete, online testing will test a large number of boards very quickly. For mass production, the advantages of speed and functional testing quickly offset the development time and cost of ICTs.
Flying needle test
The system is also designed to verify the integrity of the assembled circuit board, but this is completely different from ICT. Instead of test fixtures, only two to six probes can fly around to visit each test spot on the board. Flying probe systems can be installed quickly and inexpensively without the need to build expensive test fixtures. In addition, any board changes that require changes to the test system can be easily reprogrammed.
The downside of flying needles is that they are very slow. The ICT can test almost all points on the board in real time, while the flight probe system must maneuver its probes to each individual test point. On a large board, this can take a long time and eliminates the ability to do functional testing. However, for prototype or small batch production, testing with flying needles can be very beneficial.