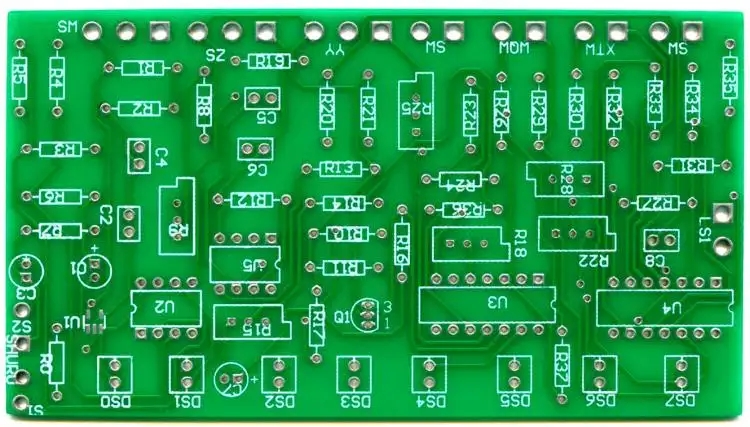
Welding peak temperature and solder paste melting point
In the daily patch processing, because of the particularity of the customer's products or the different characteristics of the solder, the whole process of PCBA manufacturing is not a standard thing.
In the daily patch processing, because of the particularity of the customer's products or the different characteristics of the solder, the whole process of PCBA manufacturing is not a standard thing. In brief, in the process of reflow soldering, the reflow soldering temperature needs to be accurately adjusted because of different PCB substrates, different high and low temperature solders, and different product functional indicators. More often, the furnace temperature tester is also needed. Now let's learn about the time between the peak welding temperature and the melting point of the solder paste.
Requirements on peak welding temperature and melting point time of solder paste
Welding peak temperature
Because the packaging structure and size of each component on the PCB are different, the temperature curve obtained by the test is not a curve, but a group of temperature curves. Therefore, the peak temperature of welding has the highest peak temperature and the lowest peak temperature. The design of welding peak temperature must first determine the process category, such as:
(1) Mixed loading process - BGA with lead solder welding SAC305 solder ball.
(2) Low temperature solder process - BGA of low temperature solder (such as Sn57 Bilag) welding SAC305 solder ball
(3) Conventional lead-free process - welding SAC305 with SAC305 solder.
(4) Low silver solder process -- low silver solder welding lead-free BGA
Secondly, the basic SMT chip processing and welding process requirements shall be met, that is, the peak temperature shall not be higher than the maximum thermal temperature of the components, nor lower than the minimum welding temperature.
Finally, it is suggested that the welding of BGA has its particularity, i.e., the phenomenon of once and twice collapse. Only after two collapses of BGA welding, can the standard drum shape solder joint morphology be formed and self centering be realized. The test shows that the peak welding temperature of BGA solder joint must be 11~12 ℃ higher than the melting point of solder paste and last for enough time to realize the secondary collapse. In actual production, the uneven interval between Kazhong and PCBA and the fluctuation of furnace temperature are often required to be higher than 15 ℃, which is to ensure that all BGAs meet this requirement. Otherwise, there may be solder joints where the solder ball is not completely fused with the solder, which is also the standard feature of mixed loading process using low temperature welding peak temperature and low temperature solder welding. If it is really necessary to weld at low temperature due to the heat resistance of components and parts, it is necessary to ensure that the BGA patch is centered, because automatic centering cannot be achieved when the solder ball and solder cannot be fused. This situation is also prone to special bridging due to alignment problems.