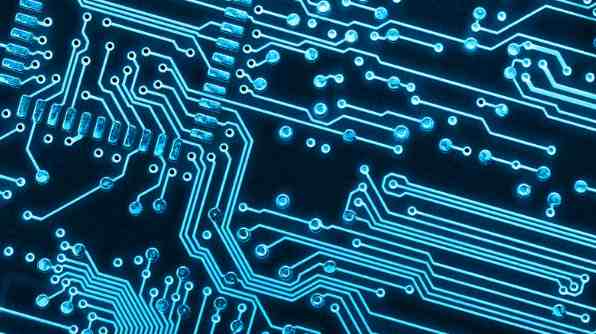
Computer aided manufacturing (CAM) systems can then use the design information finalized and validated to manage and control the automated manufacturing process. PCB manufacturing, component placement, machine parts manufacturing and assembly. The integrated PLM solution automatically links the design process to the manufacturing facility, eliminating the risk of errors in transferring design data to the production process.
Manufacturing industry
We have seen PLM solutions facilitate the automatic transfer of design data sets to manufacturing facilities to manage the engineering aspects of the production process. PLM solutions will also support management functions to control production. The marketing process will meet the requirements of the productivity and delivery plan to meet the forecast demand. The design process will generate bills of materials, combined with productivity data, into supply chain management and procurement processes to ensure that procurement components are available when required by the manufacturing process. The supply chain management process will also drive the distribution process, manage transportation and inventory of finished products.
The benefit of integrating PLM solutions is managing exceptions. The component's unavailability is communicated immediately to all stakeholders, highlighting any impact on the production schedule. This forward-looking ability allows the procurement of replacement components that are not available in the long term or the adjustment of production plans in response to short-term supply problems.
Taking this to an extreme, where a critical component is unavailable for a long period of time without a suitable replacement, has traditionally led to production stops and a premature end to the product lifecycle. PLM solutions allow changes to be made to circuit designs to find alternative solutions that are seamlessly introduced as controlled changes that move through the engineering process and update the manufacturing data set. Such changes can be designed, validated, and integrated into the manufacturing process in days rather than months.
The integration solution informs the engineering process and provides important information to support functions. Changes to the bill of materials go through the procurement process to assess cost and lead time. The cost of the modified components is then fed into the business operations to assess the financial viability of product pricing and changes. The revised lead time is integrated into project management processes as well as production and supply chain processes. This flow of information allows the impact of change to be assessed and enables informed decisions across business processes.
allocation
The integrated PLM solution will enable the marketing team to understand what products were produced and where. In addition, the integration of supply chain distribution and sales processes can optimize marketing efforts. For example, they can guide where promotions can make an impact and highlight potential out-of-stock issues that can be addressed before they affect the business.
Since the marketing process must progress through the engineering process, the marketing strategy will be developed well in advance. Management of product production setbacks due to delays in the design process may occur before the design team realizes that delays will have an impact. This joint approach to product information dissemination simplifies the process and provides stakeholders with a longer planning scope using more accurate predictive data.
support
Once the product is in production and marketed, the engineering process goes into continuous support. For example, consumer feedback and trouble reports can be fed into the PLM process for collation and analysis to determine if any design issues need to be addressed in the current product or lessons learned can be incorporated into the development of subsequent products. Integrated processes ensure that this valuable information is available to the right people for continuous improvement.
PLM solutions also facilitate in-service product support and maintenance processes by ensuring access to the information needed to manage immediate requests and perform trend analysis to prepare for predicted support requirements. It can identify and troubleshoot problems before they occur, leading to significant life-cycle cost savings. Introducing product improvements into the manufacturing process is much cheaper than recalling and replacing products with inherent design flaws.
The end of life
All products end their lives when a new, better model replaces it or when market demand falls to uneconomic levels. While recycling and reusing old products has gained momentum in all industries, electronic devices have led to recycling regulations and sustainability programs. Integrated BLM solutions provide valuable support in identifying parts and materials that can be recycled, reused, or reused, and in managing disposal processes for waste that cannot be reprocessed. This capability has the potential to reduce lifetime costs, where disposal without recycling can be an expensive option.
conclusion
Integrated product lifecycle management solutions can bring significant benefits to the electronics manufacturing industry. The integration of support engineering processes with other support business processes provides an end-to-end system that manages all aspects of the product development process from cradle to grave. The key benefit is the ability to seamlessly and painlessly manage any type of change, ensuring that the impact is effectively managed and controlled to reduce disruptions and increase greater results.