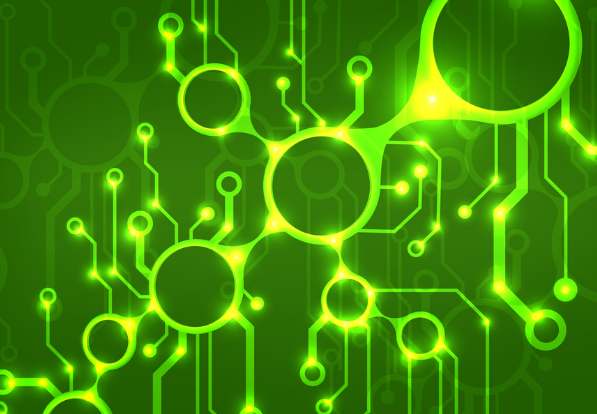
24 tips to reduce noise and electromagnetic interference in PCB design:
1. Can use low-speed chips do not need high-speed, high-speed chips are used in key places.
2. Can be used to string a resistor method to reduce the control circuit up and down jump rate.
3. Try to provide some form of damping for relays, etc.
4. Use the lowest frequency clock that meets system requirements.
5. The clock generator is as close as possible to the device using the clock. The quartz crystal oscillator housing should be grounded.
6. Circle the clock area with the ground line, and the clock line is as short as possible.
7. I/O drive circuit as close as possible to the edge of the printed board, so that it leaves the printed board as soon as possible. The signal entering the printed board should be filtered, the signal from the high noise area. Filter should also be added, and the method of string terminal resistance should be used to reduce the signal reflection.
8. The useless end of the MCD should be connected to the high, or grounded, or defined as the output end, and the end of the power supply on the integrated circuit should be connected, and do not hang.
9. The idle gate circuit input end should not be suspended, the idle operation amplifier positive input end is grounded, and the negative input end is connected to the output end.
10. As far as possible, the printed board uses 45 polylines instead of 90 polylines to reduce the external transmission and coupling of high-frequency signals.
11. The printed board is partitioned according to the frequency and current switching characteristics, and the noise element is further away from the non-noise element.
12. Single-panel and dual-panel single-point power supply and single-point grounding, power cord, ground wire as thick as possible, if the economy is able to withstand multi-layer board to reduce the power supply,
The Inductance Of The Ground
13. The clock, bus, chip selection signal should be away from the I/O line and connector.
14. The analog voltage input line and the reference voltage end should be as far away from the digital circuit signal line as possible, especially the clock.
15. For class A/D devices, the digital part and the analog part would rather be unified than crossed.
16. The clock line perpendicular to the I/O line has less interference than the parallel I/O line, and the clock element pin is far away from the I/O cable.
17. The element pin should be as short as possible, and the decoupling capacitor pin should be as short as possible.
18. The key lines should be as thick as possible, and protective places should be added on both sides. High-speed lines should be short and straight.
19. The line that is sensitive to noise should not be parallel to the high-current, high-speed switching line.
20. Do not walk under quartz crystals and noise-sensitive devices.
21. Weak signal circuit, low frequency circuit do not form a current loop around.
22. The signal should not form a loop, if inevitable, let the loop area as small as possible.
23. One decoupling capacitor per integrated circuit. A small high-frequency bypass capacitor is added to the side of each electrolytic capacitor.
24. Use high-capacity tantalum capacitors or polycool capacitors instead of electrolytic capacitors as circuit charge and discharge energy storage capacitors. When using tubular capacitors, the housing should be grounded.
Factors That Determine The Flexural Performance Of Flexible PCB Boards
In PCB design, the flexural performance of FPC is very important, and the factors that affect it can be viewed from two aspects:
First of all, from the FPC material itself, the following points have an important impact on the flexural performance of FPC.
First, the molecular structure and direction of copper foil (i.e. the type of copper foil)
The bending resistance of calendered copper is obviously better than that of electrolytic copper foil.
Second, the thickness of copper foil
For the same variety, the thinner the thickness of the copper foil, the better the folding resistance.
Third, the type of glue used in the substrate
Generally speaking, the softness of epoxy resins is better than that of acrylic adhesives. Therefore, when the choice of highly flexible materials is required, the epoxy system is mainly used. And the adhesive with higher tensile modulus (tensilemodulvs) can improve the flexural property.
Fourth, the thickness of the glue used
The thinner the thickness of the glue, the better the softness of the material. The flexure of FPC can be improved.
Fifth, insulation substrate
The thinner the thickness of the insulating substrate PI, the better the softness of the material, improving the flexural property of FPC, tensile modolos PI is better for the flexural property of FPC.
Summarize
The main influence factors of material on flexure are two main aspects: the type of material selected; Thickness of material
The influence of flexural property of FPC is analyzed from the process aspect.
First, the symmetry of FPC combination
The better the symmetry of the two sides of the copper foil can improve its flexural property after the substrate is bonded with the covering film. Because the stress they experience when they bend is the same.
The PI thickness on both sides of the PCB board tends to be consistent, and the thickness of the glue on both sides of the PCB board tends to be consistent
Second, the control of pressing process
When coverlay is pressed, the glue should be completely filled into the middle of the line, and there should be no delamination (slice observation). If there is a stratification phenomenon in the bending equivalent to bare copper in the bending will reduce the number of bending.