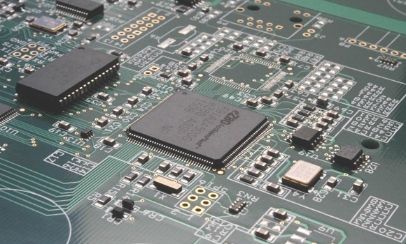
PCB design should consider many factors, such as external connection layout, layout design, optimization layout of internal electronic components, etc. The function of PCB design is to standardize the design operation, improve the production efficiency and improve the quality of electronic products.
Information required for PCB design:
1. Schematic diagram: Complete electronic document format that can generate the correct netlist, and provide the layout and function required by the PCB;
2. Mechanical size: Provide PCB with multi-clock physical information, such as the specific position and direction of electronic equipment;
3. Equipment packaging: provide equipment packaging library, packaging methods and electronic material specifications of PCB circuit boards;
4. Wiring guide: Provide specific requirements for special signals and impedance design for PCB.
PCB circuit board design principles:
1. Choose the right set of grids and always use a grid spacing that matches most components. Although the practicality of multiple grids may seem important, if engineers had thought more during the early stages of PCB layout design, they could have avoided the difficulties of spacing setup and maximised the board's application. Since many devices use multiple package sizes, engineers should use the product most conducive to their own design. In addition, polygons are very important for copper plating on circuit boards. Polygon filling deviation usually occurs when polygon plating copper on multi-grid circuit boards. While it does not have a standard based on a single grid, it can provide service beyond the required life of the boards.
2. Keep the path shortest and most direct. This sounds simple and common, but it should be kept in mind at every stage, even if it means changing the board layout to optimize the wiring length. This applies especially to analog and high-speed digital circuits, where system performance is always limited in part by impedance and parasitic effects.
3. Use the power layer to manage the distribution of power cables and ground cables as much as possible. Copper coating on the power layer is a faster and easier option for most PCB design software. By sharing a large number of conductors, it ensures that the most efficient current with the least impedance or voltage drop is provided, and that adequate ground loops are provided. If possible, multiple power lines can also be operated in the same area of the board to verify that the grounding layer covers most of the PCB layer. This facilitates interaction between operating lines on adjacent layers.
4. Assemble the relevant parts with the required test points. For example, the discrete components needed for OPAMP operational amplifiers are placed close to the device so that the bypass capacitors and resistors can fit in with them, helping to optimize the wiring length mentioned in Rule 2 and making testing and fault detection easier.
5. Duplicate the required circuit board several times on another larger circuit board for PCB assembly. Choosing the size that best fits the equipment used by the manufacturer helps reduce prototyping and manufacturing costs. First, lay out the boards on the panels, contact the board manufacturer to get the preferred size specifications for each panel, then modify the design specifications and try to repeat the design several times within those panel sizes.
6. Integrate component values. As a designer, you choose discrete components that have high or low component values but are equally efficient. By integrating within a small range of standard values, bills of materials can be simplified and costs reduced. If you have a range of PCB product on preferred equipment values, you are more likely to make the right inventory management decisions over the long term.
7. Perform as many design rule checks (DRC) as possible. Although it only takes a short time to run DRC functionality on PCB software, in more complex design environments, it is a good habit to keep up by saving a lot of time simply by performing checks throughout the design process. Every routing decision is critical, and doing DRC can prompt you to choose the most important route at any time.
8, flexible use of screen printing. Screen printing can be used to mark a variety of useful information for future use by circuit board manufacturers, service or test engineers, installers, or equipment debuggers. Not only should the function and test point labels be clearly marked, but the orientation of the components and connectors should be marked as much as possible, even if these notes are printed on the lower surface of the components used on the board. The full application of screen printing technology on the upper and lower surfaces of the circuit board can reduce repetitive work and simplify the production process.
9. Decoupling capacitors are required. Do not try to optimize the design by avoiding power cord decoupling and based on limitations in the component data sheet. Capacitors are cheap and durable. Take as much time as you need to assemble the capacitor. Also, follow Rule 6 and use standard value ranges to keep inventory clean.
10. Generate PCB manufacturing parameters and verify them before submitting to production. While most board manufacturers are happy to download and verify it directly for you, it's best to export the Gerber files first and use the free reader to check that they are as expected to avoid misunderstandings. Through personal verification, you may even find careless errors to avoid the cost of completing production with the wrong parameters.
PCB circuit board special components refer to the key components of the high frequency part, the core components in the circuit, vulnerable to interference components, high voltage components, high calorific value components and some components of the opposite sex. The positions of special parts should be arranged in accordance with the following principles:
1. Shorten the connection between high-frequency components as far as possible to reduce their distribution parameters and mutual electromagnetic interference. Susceptible components should not be too close together, and inputs and outputs should be as far apart as possible.
2. Some components or wires may have a high potential difference, so the distance between them should be increased to avoid accidental short circuit caused by discharge. High voltage components should be placed as far as possible out of hand reach.
3. Parts weighing more than 15g can be fixed with brackets and then welded. These heavy and hot components should not be placed on the circuit board, but should be placed on the bottom plate of the main box, and should consider heat dissipation. The hot component should be far away from the heating component.
4. For the layout of adjustable parts such as potentiometer, adjustable inductor coil, variable capacitor and micro switch, the structural requirements of the whole wrench should be considered. If the structure permits, some commonly used switches should be placed in a position easily accessible to the hand. The layout of the components should be balanced, dense, and not heavier than the top