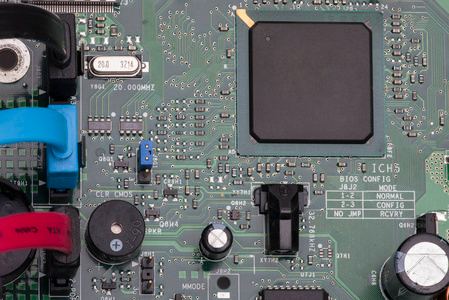
Metal-core PCB are not very common in consumer products, but they abound in industrial, aerospace, lighting systems, power electronics, and other areas that require high reliability. High power systems generate a lot of heat and need to be removed quickly to prevent component failure. Similarly, low-power systems may be exposed to high heat and need to be removed quickly to prevent damage to the circuit board and components.
Metal core PCB designs (including DFM) follow many of the same basic design rules as typical PCBS on FR4. If you want to design a new product in any of these areas, you may need to use metal core panels to control the temperature. In this article, the structure of a metal-core PCB is briefly described and some important design points to consider before planning to use a metal-core PCB design. These boards carry special manufacturing requirements, but the right design company can help with these requirements and ensure that PCBS can be mass-produced.
Application of metal core PCB design
Metal-core PCBS can find their place in almost any application where the device generates a lot of heat while operating. These plates are not ideal replacements for ceramics because they are a lower cost option and they provide higher thermal conductivity, which removes heat from important components. They are often a starting point when looking for circuit boards for systems with high cooling capacity. Some applications of metal core PCBS include:
LED lighting unit: A board with a high power LED is usually manufactured on a metal core PCB. These panels provide a sturdy base for high power leds (SMDS and through-holes) while dissipating high heat into the metal core panels.
Power conversion and management: Hybrid electric vehicles, industrial equipment, telecommunications equipment and municipal distribution systems all operate at high power levels. In these areas, metal core PCB are common.
Solar equipment: Solar equipment needs to be particularly strong and operate at high temperatures and high DC voltage and current. Similar PCB designs can be implemented in geothermal facilities.
Military: Metal-core PCBS quickly dissipate heat, keeping electronics away from devices that may be located near high heat sources such as engines or exhaust systems.
High reliability and structural stiffness are also critical in many other areas, making metal core panels an excellent choice. Once you start looking at the stacking and layout requirements of these boards, it becomes less obvious how to actually design them. Can you make multiple metal core plates? Can it be double-sided? How are holes treated in the manufacturing process? These are all important issues related to DFM of metal core PCB circuit boards.
DFM for metal core PCB
As with other PCBS, specific DFM guidelines need to be followed if successful manufacturing runs are to be ensured. The process employed for metal core boards is different from the typical PCB lamination process involving glass braided laminates, so they tend to adopt different DFM rules.
Note that the lamination can be technically adapted to be a multilayer, in which a metal core has multiple dielectrics on each side. Alternatively, you can make the circuit board single-sided, leaving the back of the metal core exposed. In the design of metal core PCB, the following are the manufacturing points to pay attention to:
Metal core ground
The metal backing on the PCB circuit boards can work like a large ground layer or a large heat sink. If the board requires the use of high speed, high frequency circuit blocks, using the back metal plate as a larger grounding layer can provide some shielding. It can also provide some flat capacitance if the power plane is used on the board.
In addition, metal cores can be used as large radiators, especially if exposed. The latter aspect is useful when the board needs to be installed near high heat sources. In this case, it is advisable not to ground the back of the top side when connecting it to a standard power supply. This prevents grounding loops. This will also dissipate heat directly into very large radiators, which helps to lower surface temperatures.
Holes in a single panel
Holes can be placed on metal core PCBS, either as mounting holes or as standard through-holes on dual panels. If the holes are to be used only to install through-hole components on a single panel, they should not be electroplated to prevent short circuits. This is done by drilling holes in the mounting holes and filling the holes with a non-conductive epoxy resin or gel. The holes are then plugged so that installation can be performed on the upper level.
Double panel holes
In a double-sided metal core PCB, certain components may be installed on both sides and electroplated holes may be placed between the signal layers. Electroplating through hole is formed by pre-drilling → insulation filler → redrilling → electroplating process, so there will be some difficulties in manufacturing. This process takes additional time and incurs additional costs, but it is designed to prevent through-hole short-circuiting. In a PCB layout, it is best to use a solder pad to indicate the area around the through-hole that needs to be filled with insulating filler material. Ensure that the hole pads are sized to comply with IPC-2221 standards.
DFM is otherwise indistinguishable from standard PCBS in metal-core PCB design, although CAD tools are not used to design these circuit boards. Power electronics front ends are subject to a number of minor rules, notably IPC-2221 (creepage and release rules), as well as other defense and aerospace standards.