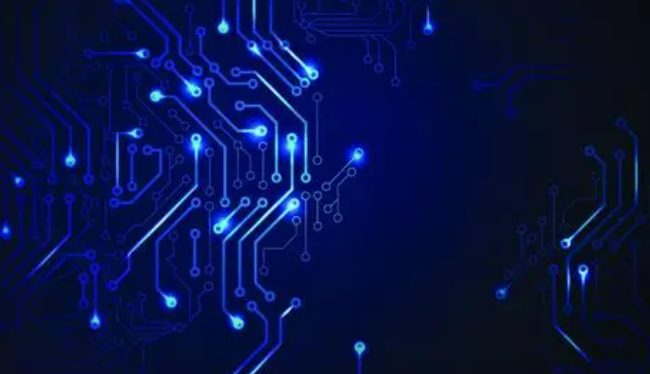
If layer 2 is allocated as "ground" and layer 4 is allocated as the processor's power supply, the through hole distance from the top layer where the processor and decoupling capacitors are placed should be as short as possible. The remaining portion of the overpass extending to the bottom of the plate does not contain any significant current, and the distance is too short to act as an antenna.
The 20-H rule and the 3-W rule
In the electromagnetic compatibility design of multilayer PCB board, there are two basic principles to determine the distance between the multilayer power layer and the edge and to solve the distance between the printed strip: 20-H rule and 3-W rule.
20-H principle: RF current usually exists at the edge of the power plane due to the connection between the magnetic flux. This interlayer coupling is called edge effect. When high speed digital logic and clock signals are used, RF current is coupled between the power planes. To reduce this effect, the physical size of the power plane should be at least 20H smaller than the physical size closest to the ground plane (H is the distance between the power plane and the ground plane). The edge effect of the power supply usually occurs around 10H, and about 10% of the magnetic flux is blocked in 20H. If 98% of the magnetic flux is blocked, the boundary value needs to be 100%. The 20-H rule determines the physical distance between the power plane and the nearest ground plane. This distance includes copper thickness, prefill, and insulation separation layers. Using 20-H can improve the resonant frequency of PCB itself.
PCB RF edge effect 3-W rule: when the two printed line spacing is small, electromagnetic crosstalk will occur between the two lines, which will make the circuit function is abnormal, in order to avoid this interference, should keep any line spacing is not less than 3 times the width of the printed line, that is, not less than 3W (W is the width of the printed line). Printed line width depends on the line impedance requirements, too wide will affect the wiring density, too narrow will affect the integrity and strength of the signal transmitted to the terminal. Clock circuit, difference pair, I/O port wiring are the basic application objects of 3-W principle. The 3-W principle only indicates the boundary of electromagnetic flux line with 70% crosstalk energy attenuation. If the requirement is higher, 10W interval must be adopted to guarantee the boundary line of electromagnetic flux with 98% crosstalk energy attenuation.
Ground arrangement
First, to establish the concept of distributed parameters, above a certain frequency, any metal wire should be regarded as a resistance, inductance component. So the ground lead has a certain impedance and constitutes an electrical circuit, whether it is single point ground or multi-point ground, must form a low impedance circuit into the real ground or frame. A typical printed line of 25mm in length will show about 15 ~ 20nH inductance, and the presence of distributed capacitance will form a resonant circuit between the ground floor and the equipment frame. Secondly, when the ground current flows through the ground wire, there will be transmission line effect and antenna effect. When the line is 1/4 wavelength long, exhibiting high impedance, the ground wire is actually open, and the ground wire instead becomes an antenna radiating outward. Finally, the ground floor is filled with vortices caused by high-frequency current and disturbance, so that a number of loops are formed between the ground points. The diameter of these loops (or ground spacing) should be less than 1/20 of the highest frequency wavelength. The selection of appropriate devices is an important factor for successful design, especially in the selection of logic devices, try to choose the rise time longer than 5ns, never choose a logic device faster than the timing required by the circuit.
Arrangement of power lines
For multilayer panels, the power supply layer to layer structure is used. The characteristic impedance of this structure is much smaller than that of rail pairs, and can be less than 1Ω. This structure has a certain capacitance, it is unnecessary to add a high-frequency decoupling capacitor beside each integrated chip. Even if the layer capacitance is not enough and an additional decoupling capacitance is needed, do not add it to the side of the integrated chip. It can be added anywhere on the printed board. The power pins and footing of the integrated chip can be directly connected to the power layer and ground through the metallized through holes, so the power supply loop is always minimal. Due to the principle of "the current always goes through the path of minimum impedance", the high frequency backflow in the formation is always close to the track line, unless there is a barrier between the formation, so the signal loop is always minimal. It can be seen that the layer-ground structure of power supply has the advantages of simple and flexible layout and good electromagnetic compatibility compared with the rail pair power supply.
Concluding remarks
In short, in multilayer PCB design, components should be placed in groups to prevent inter-group interference; The location of high-speed circuits should be arranged properly so as not to interfere with other circuits through electric or magnetic coupling; The ground wire is set respectively according to the situation to prevent impedance coupling interference of common ground wire; The area of the power supply loop should be reduced to a minimum, and the power supply loop of different power sources should not overlap to avoid magnetic field coupling. Incompatible signal lines should be isolated from each other to avoid coupling interference; The signal loop area should also be reduced to reduce loop radiation and common-mode radiation.