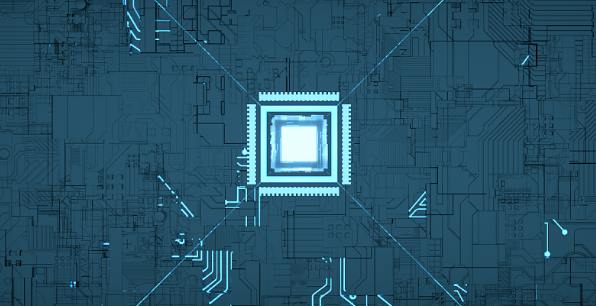
For most companies, manual inspection is the first line of defense. Inspectors use a variety of magnifying tools to take a closer look at the components and welds. IPC-A-610 establishes some basic amplification guidelines based on pad widths of the inspected components. The main reason for these guidelines is to avoid excessive scrutiny due to excessive amplification. For example, if the pad width is 0.25 to 0.50 mm, then the desired magnification is 10X. If necessary, 20X can be used as a reference.
Every inspector has a favorite inspection tool; A folding pocket magnifying glass with three lenses used by mechanics is preferable. It is portable and has a maximum magnification of 12X, which is just right for close-spaced welds. Perhaps the most common inspection tool is the microscope, which magnifies 10 to 40X. However, continuous use of the microscope causes fatigue and usually leads to overexamination, as magnifications usually exceed the guidelines for IPC-A-610. Of course, this is useful when you need to scrutinize possible defects.
For general inspection, a video system with a zoomable lens (4-30X) and a high definition color monitor is preferred. These systems are easy to use and, more importantly, less prone to fatigue than microscopes. High-quality video systems cost less than $2,000, and good microscopes are in that range. The added benefit of a video system is that more than one person can see the object, which can be helpful in training or when an inspector needs a second opinion. Edmund Scientific (edmundscientific.com) has a wealth of magnification tools, from handheld magnifying glasses to microscopes to video systems.
In summary, establishing a balanced monitoring strategy between 0-100% inspections is a challenge. From this point, the key checkpoint, we will discuss checking the device... .
Automation is wonderful; In many cases, more accurate, faster, and more efficient than the inspector. But it can be quite expensive, depending on how complicated it is. Automated inspection devices may dilute awareness and give a false sense of security.
Solder paste check. Solder paste printing is a complex process, and it is easy to deviate from the desired result. A clearly defined and properly implemented process monitoring strategy is required to keep the process under control. At the very least, manually check the coverage area and measure the thickness, but it is better to use automated coverage, thickness, and volume measurements. Use the range control chart (X-bar R chart) to record the results.
Solder paste inspection equipment ranges from simple 3X magnifying glasses to expensive automatic on-line machines. Primary tools use optics or lasers to measure thickness, while secondary tools use lasers to measure coverage, thickness, and volume. Both tools are used offline. Tertiary tools also measure coverage, thickness, and volume, but are installed online. The speed, accuracy, and repeatability of these systems vary, depending on price. More expensive tools provide better performance. (SMT SMT processing technical data)
For most assembly lines, especially high-mix production, medium level performance is preferred, which is an off-line, table-mounted tool that measures coverage, thickness, and volume. These tools are flexible, cost less than $50,000, and generally provide the desired amount of feedback. Obviously, automated tools are much more expensive ($75,000 - $200,000). However, they are faster and more convenient because they are installed online. Best suited for high volume, low mix assembly lines.
Inspection of glue. Glue distribution is another complex process that can easily deviate from the desired result. As with solder paste printing, a clearly defined and properly implemented process monitoring strategy is required to keep this process under control. Manual inspection of glue point diameter is recommended. Use the range control chart (X-bar R chart) to record the results.
Before and after a drip cycle, it is a good idea to drop at least two isolated glue points on the board to represent the diameter of each point. This allows the operator to compare the glue point quality during the rubber cycle. These points can also be used to measure the glue point diameter. Glue point inspection tools are relatively inexpensive, basically a portable or bench measuring microscope. It is not known that there is no automatic equipment specially designed for glue point inspection. Some AOI (automated optical inspection) machines can be adapted for this task, but may be overqualified.
Confirmation of initial product (first-article). The company usually makes a detailed inspection of the first board that comes off the assembly line to verify the setup of the machine. This approach is slow, passive, and inaccurate. It is common to see a complex board containing at least 1000 components, many of which are unmarked (values, part numbers, etc.). This makes inspection difficult. Verification of machine Settings (components, machine parameters, etc.) is a positive approach. AOI can be used effectively for the inspection of the first board. Some hardware and software vendors also provide feeder Settings confirmation software.