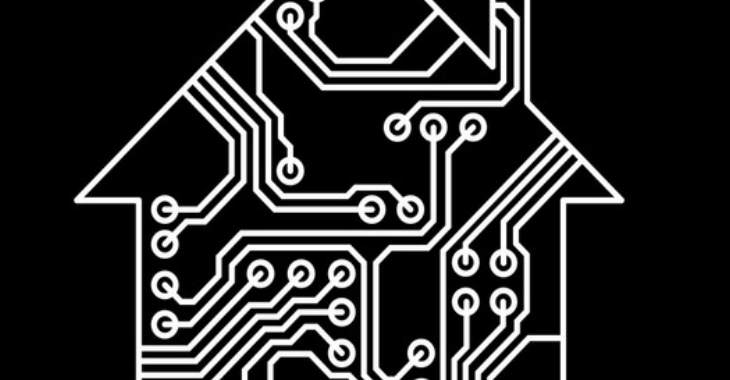
If there is no air knife or the air knife cannot work properly, install, adjust and repair the air knife in time. The production of the wind knife is not complicated, can be about 50cm long, the inner diameter of 1-1.5cm stainless steel tube, one end of the plug, the other end of the air pump tube, in the middle of the stainless steel pipe with a fine drill evenly punched out about 0.3mm holes, and then fixed in the nozzle or welding groove with a clamp; Adjust the blowing Angle according to the method described in the diagram above.
Second, in the over-preheating zone, PCB flux in the furnace steam concentration is too large, resulting in deflagging. There are three main reasons for the excessive steam concentration of PCB flux:
1. PCB flux coating is too much, or there is no effect of wind knife, and too much steam is volatilized in the preheating section. If it is caused by this situation, according to the method described above, the wind knife installed or adjusted to the normal working state can reduce the concentration of the auxiliary agent steam in the furnace;
2. The pump (exhaust) air device of the wave crest welder cannot work normally, or the exhaust effect is poor, resulting in high PCB flux concentration in the furnace. It can strengthen the air pumping (exhaust) device on the wave welding machine. It is recommended to use a powerful and powerful air pumping and exhaust device to ensure that the PCB flux concentration in the furnace (especially in the preheating section) is not too high;
3. If the pump (exhaust) air device of the wave soldering machine itself has poor effect, and there is a protective cover above the preheating section of wave soldering (refer to Figure 3), in this case, it is likely to cause the concentration of PCB flux is too high. If all kinds of improvements are not effective, it is recommended to remove the protective cover, so as to reduce the steam concentration of the timing agent in the furnace and reduce the possibility of PCB flux deexplosion.
Cause analysis and countermeasure of PCB flux ignition during over wave soldering
To sum up, the main reasons for PCB flux fire during over-wave soldering are as follows:
1. PCB flux itself does not add flame retardant, or the amount of flame retardant is too small or the type is not correct; (This is a more complex and difficult to determine the problem, because we have mentioned above, even with the addition of flame retardants, PCB flux itself is still flammable and explosive, but the PCB flux without flame retardants may have a relatively lower degree of dedetonation. At the end of this article, I sincerely say that the effect of this behavior is not obvious, and it does not change the inflammable and explosive characteristics of PCB flux itself.
2. Process problems in wave soldering of PCB flux. In addition to the poor flame retardant of PCB itself, the rest of the aspects, such as too fast or too slow board speed, preheating temperature is too high, basically can be effectively improved by the process parameters.
3. The working condition of the machine itself. In fact, the process problem and the working condition of the machine and equipment are closely related and inseparable two factors influencing each other. As we have analyzed above, common PCB flux itself is inflammable and explosive (except water-based PCB flux or special PCB flux), so more often, we hope that the manufacturer can improve the problem of PCB flux easy to fire by adjusting the process and equipment condition.
The ultimate purpose of this paper is to hope that all PCB flux users can completely solve or avoid the "PCB flux fire in wave soldering" situation; It is also expected that all PCB flux manufacturers can take the safety of PCB flux use process into more comprehensive consideration, as far as possible to reduce the degree of detachable PCB flux. In view of the situation of PCB flux fire, flux manufacturer can not completely shift the responsibility to the manufacturer, PCB flux manufacturer, can not completely blame the PCB flux manufacturer, such a situation, or hope that the production and use of both sides, can calmly, more objective from many aspects to find the cause of the problem, And finally find out the countermeasures, so that the problem can be completely solved.