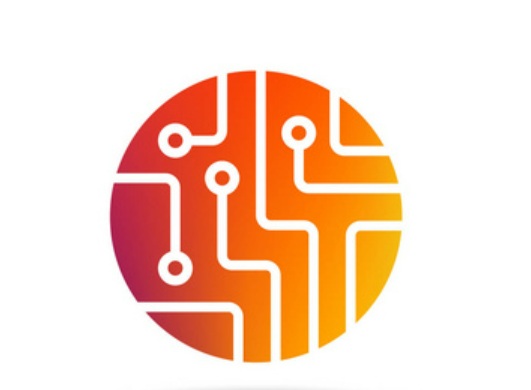
In the actual production of pcb circuit board, the width and thickness of wire, dielectric constant of insulating material and thickness of insulating medium will cause the change of characteristic impedance value. In addition, the characteristic impedance value may be related to other production factors.
1. Surface microstrip line and characteristic impedance
The surface microstrip line has a high characteristic impedance value and is widely used in practice. Its outer layer is a signal line surface that controls the impedance, and it is separated from its adjacent datum surface by insulating materials.
The characteristic impedance of the calculation formula is: Z0 = 87 / SQRT (epsilon r + 1.41) x ln [(5.98 h)/(0.8 w + t)]
Z0, characteristic impedance of printed conductor;
εr: dielectric constant of insulating material;
h: Thickness of the medium between the printed wire and the datum surface;
w: width of printed wire;
t: Thickness of printed wire.
It can be seen from the calculation formula of the characteristic impedance that the main factors affecting the characteristic impedance are: (1) dielectric constant εr; (2) medium thickness h; (3) wire width w; (4) Wire thickness t, etc. Therefore, the characteristic impedance is closely related to the substrate material (copper-clad sheet), so the selection of substrate material is very important in PCB design.
2. Dielectric constant of materials and its influence
The dielectric constant of the material is measured by the material manufacturer at the frequency of 1 MHz. The same material produced by different pcb manufacturers varies due to its resin content. The dielectric constant decreases with the increase of frequency, so in practical application, the dielectric constant of materials should be determined according to the working frequency, and the average value can meet the requirements.
3, the influence of wire width and thickness
Wire width is one of the main parameters that affect characteristic impedance variation. The width of wire is determined by the designer according to a variety of design requirements, which should not only meet the requirements of carrying capacity and temperature rise of wire, but also obtain the expected impedance value. This requires the producer to ensure that the line width meets the design requirements in production, and make it change within the tolerance range, in order to adapt to the impedance requirements.
The thickness of the conductor is also determined by the required carrying capacity of the conductor and the allowable temperature rise. In order to meet the requirements of use in production, the coating thickness is generally an average of 25um. Wire thickness is equal to copper foil thickness plus coating thickness.
How to reflow solder PCB patch with one side solder paste and one side red SMT glue
There are two processes for double-sided patch reflux welding furnace
One is double-sided solder paste, one side solder paste, one side red glue
Both processes are almost always welding one side after pasting, and then welding the other side. Because the melting temperature of both solder paste and red glue after curing is higher than the temperature of reflow welding, there will be no loss of parts due to temperature.
But the solder paste surface can not be wave soldering, but the red rubber surface can be wave soldering.
Incoming material detection -> PCB side A screen printing solder paste (spot patch glue) -> Patch --> Drying (curing) --> A-side reflow welding --> Cleaning --> Turn over the board --> PCB side B screen printing solder paste (spot patch glue) -> Patch --> Drying --> Reflow welding (preferably only for side B --> Cleaning --> Detection --> Repair)
This process is suitable for PCB with PLCC and other large SMDS on both sides.
Cause analysis and countermeasure of PCB flux ignition during over wave soldering
When PCB flux passes wave soldering, some guests find that PCB flux will catch fire, especially in summer when the temperature is higher and the air is dry, the incidence of this situation is relatively high. PCB flux fire not only brings a certain economic loss, but also easily leads to the fire to the working equipment or personal injury. Based on years of research and development of PCB flux technology and welding process experience, we analyzed the causes of PCB flux fire as follows, and put forward corresponding countermeasures.
Generally speaking, the reasons for this situation can be roughly summarized from three aspects. On the one hand, it is the PCB flux itself, on the other hand, it is the process, and the last one is the working condition of the equipment.
In addition to water-based PCB flux or some special PCB flux, the solvent part of commonly used PCB flux is mostly alcohols, mainly methanol, ethanol and isopropyl alcohol. Because of the toxicity of methanol and its relative instability in PCB flux, methanol is rarely used as a single solvent. So the use of ethanol, isopropyl alcohol or isopropyl alcohol and methanol mixed solvent manufacturers more. Alcohols themselves are inflammable and explosive. Refer to the following comparison table of the performance parameters of the three alcohols (Table 1), the flash points of the three alcohols are all similar, at 11-12℃, and their steam pressure is different: Methanol is 13.33kPa/21.2℃, ethanol is 5.33kPa/19℃ and isopropyl alcohol is 4.40kPa/20℃. It can be seen that under the same operating environment, methanol has the strongest combustible (or exploitable) performance, followed by ethanol and isopropyl alcohol is the weakest. In the ratio of PCB flux, through the addition of different substances (especially flame retardant), the flash point of PCB flux itself can be improved. Generally, the flash point of PCB flux can rise to about 20.8℃, which is why the flash point of PCB flux is not equal to the solvent flash point. Therefore, it is understandable that PCB fluxes with flame retardants added are less likely to be flammable (or explosive) than products without flame retardants added.