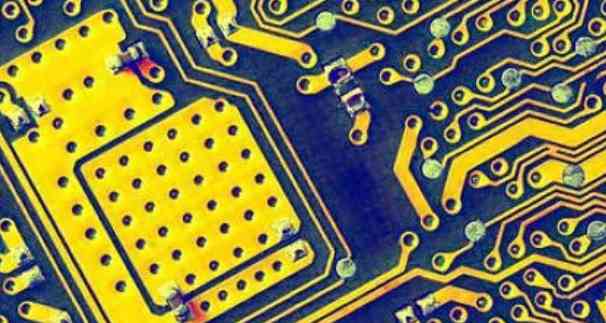
This process uses a CNC drilling machine to drill out the aluminum sheet to plug holes, made of screen plate, installed on the screen printing machine to plug holes, stop for no more than 30 minutes after the completion of the plug hole, with 36T screen directly screen face welding, the process is: pre-treatment - plug hole - screen printing - pre-drying - exposure - development - curing.
This process can ensure that the oil cover through the hole is good, the plug hole is smooth, the wet film color is consistent, the hot air leveling can ensure that the through hole is not tin, no tin beads in the hole, but it is easy to cause the ink pad in the hole after curing, resulting in poor weldability; After hot air leveling, oil bubbles off the edge of the through hole. It is difficult to use this process to control the production, so process engineers must adopt special flow and parameters to ensure the quality of the plug hole.
2.3 Aluminum sheet plug hole, development, precuring, grinding plate after the plate face welding
With CNC drilling machine, drill out the requirements of the plug hole aluminum sheet, made of screen plate, installed in the shift screen printing machine for plugging holes, plug holes must be full, both sides prominent is better, after curing, grinding plate surface treatment, its process is: pre-treatment - plug hole a pre-drying - development - pre-curing - plate surface welding
Because this process uses plug curing to ensure that HAL through the hole without oil, oil explosion, but HAL, through the hole hidden tin beads and through the hole tin is difficult to completely solve, so many customers do not accept.
2.4 Plate welding and plug holes shall be completed at the same time
This method adopts 36T (43T) silk screen, mounted on the screen printing machine, using a plate or nail bed, while completing the board surface, all the pilot holes are plugged, the process is as follows: pre-treatment - screen printing - pre-drying - exposure - development - curing.
This process time is short, the equipment utilization rate is high, can ensure that the hot air leveling through the hole does not drop oil, the through hole does not tin, but because of the use of silk screen to plug holes, there is a lot of air in the through hole, during curing, air expansion, break through the welding resistance film, resulting in holes, uneven, hot air leveling will have a small amount of tin through the hole.
At present, our company through a large number of experiments, choose different types of ink and viscosity, adjust the pressure of screen printing, basically solve the hole hole and uneven, has adopted this process for mass production.
6) Shielding the influence of RF signal on other simulation parts
As mentioned above, RF signals can cause interference to other sensitive analog circuit modules such as ADC when they are sent. Most problems occur at lower operating bands (e.g. 27MHz) and high power output levels. It is a good design practice to decouple sensitive points with an RF decoupling capacitor (100pF) connected to the ground.
(7) Special consideration in plate ring antenna
The antenna can be built as a whole on the PCB. Compared with the traditional whip antenna, it not only saves space and production cost, but also makes the mechanism more stable and reliable. By convention, a loopantenna is designed to apply to a relatively narrow band. This helps to suppress unwanted strong signals so as not to interfere with the receiver. It should be noted that annular antennas (like all other antennas) may receive noise capacitatively coupled by nearby noise signal lines. It interferes with the receiver and may affect the modulation of the transmitter. Therefore, the digital signal line must not be distributed near the antenna, and it is recommended to maintain free space around the antenna. Any object close to the antenna will form part of the tuned network, and cause the antenna tuning to deviate from the expected frequency point, so that the transmitting and receiving radiation range (distance) is reduced. With all types of antennas you must be aware of the fact that the circuit board's shell (peripheral packaging) may also affect antenna tuning. At the same time, remove the ground plane at the antenna area; otherwise, the antenna cannot work effectively.
(8) circuit board connection
If using cables to connect the RF circuit board to an external digital circuit, use twisted-pair cables. Each signal cable must be twisted together with the GND cable (DIN/GND, DOUT/GND, CS/GND, PWR_UP/GND). Remember to connect the RF circuit board and the digital application circuit board with the GND cable of the twisted-pair cable. The length of the cable should be as short as possible. The wiring that powers the RF circuit board must also be twisted-GND (VDD/GND).