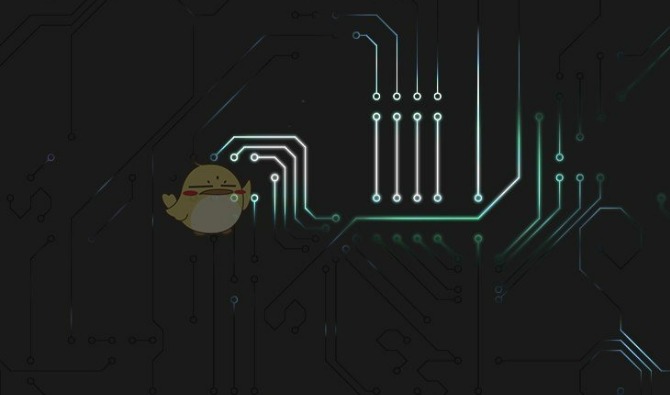
The purpose of PCB galvanizing is to prevent steel objects from being corroded, improve the corrosion resistance and service life of steel, but also make the product increase the decorative appearance, steel with the growth of time will be weathering, water or soil corrosion. Domestic annual corrosion of steel almost accounts for one tenth of the total amount of steel, so in order to protect the service life of steel or its parts, generally using PCB galvanizing to iron and steel processing.
Because zinc is not easy to change in dry air, and in the humid environment * can produce a basic zinc carbonate film, this film can protect the internal parts and not be damaged by corrosion, even if the zinc layer is damaged by some factors, zinc and steel after a period of time will form a microbattery, and the steel matrix as the cathode and protected.
Zinc is a metal with a bluish-white sheen. Atomic number 30, relative atomic mass 65.4, brittle and hard, melting point 419.4 ℃, boiling point 907℃, valence +2, relative density 7.1. Zinc is stable in dry air. Zinc is an amphoteric metal, acid, alkali will react to release hydrogen. It also reacts with hydrogen sulfide. A basic zinc carbonate film is formed in water or moist air to protect the underlying layer from corrosion.
Galvanized on iron, because of its negative potential, is anodic coating, has good electrochemical protection. Therefore, galvanizing (plus passivation with chromate after plating) is widely used to prevent the corrosion of ferrous metals. It is widely used in electroplating electrical parts, mechanical hardware, building hardware and industry.
Zinc is mainly used in industry for electroplating, hot dip plating, battery industry and manufacturing alloys (such as brass).
Summary PCB electrogalvanizing has the following characteristics:
1, good corrosion resistance, combined with fine uniform, not easy to be corrosive gas or liquid into the interior.
2, because the new layer is relatively pure, whether in acid or alkali environment is not easy to be corroded. Protect the steel body effectively for a long time.
3. After chromic acid passivation, various colors can be used, which can be selected according to customers' favorite. Galvanized is beautiful and generous and decorative.
4, zinc coating has good ductility, in a variety of bending, handling impact will not easily fall.
1, the input end and the output end of the line should avoid parallel adjacent, so as to avoid interference. Grounding should be added when necessary, two adjacent layers of wiring should be vertical to each other, parallel easy to produce parasitic coupling.
2. Add decoupling capacitance between power supply and ground wire. It is better that the ground cable is wider than the power cable. The relationship between them is ground cable > power cable > signal cable. Usually, the width of signal cable is 0.2 ~ 0.3mm, and the width can reach 0.05 ~ 0.07mm
3, digital circuit and analog circuit common ground processing, digital circuit frequency is high, analog circuit sensitivity is strong, for the signal line, high frequency signal line as far as possible away from the sensitive analog circuit devices, for the ground wire, rectifier PCB to the outside only one node, so ** in the PCB internal processing number, mode common ground problem, And inside the board the digital and analog ground is actually separate and they are not connected to each other, only in the PCB and the external connection interface (such as plugs, etc.). There is a little bit of short circuiting between digital and analog, but note that there is only one connection point. There are also differences on the PCB, which is determined by the system design.
4. Shorten the connection between high-frequency components as far as possible, and try to reduce their distribution parameters and electromagnetic interference between each other. Easily disturbed components should not be too close to each other, input and output components should be as far away as possible. There may be a high potential difference between some components or wires. The distance between them should be increased to avoid accidental short circuit caused by discharge. Components with high voltage should be arranged as far as possible in places that are not easily touched by the hand during debugging.
5. For circuits working at high frequency, the distribution parameters between components should be considered. General circuits should be arranged as parallel as possible. In this way, not only beautiful. It is easy to assemble and weld. Easy to mass produce.
6. Input and output wires should be avoided as far as possible. It is better to add ground wire between lines to avoid feedback coupling.
7, printed wire bend generally take circular arc, and right Angle or included Angle in high frequency circuit will affect the electrical performance. If you must take a right Angle, generally use two 135 degrees to replace the right Angle.
8. Power cord design
According to the size of the printed circuit board current, try to rent the width of the power line, reduce the loop resistance. At the same time, the direction of the power cord and ground wire is consistent with the direction of data transmission, which helps to enhance the anti-noise capability.
9. Ground wire design
The principles of ground design are:
(1) digital and analog separation. If the circuit board contains both logical and linear circuits, keep them as separate as possible. Low frequency circuit should be as far as possible to use a single point of parallel grounding, the actual wiring difficulties can be partially connected after the parallel grounding. The high frequency circuit should be grounded in series at multiple points, the ground should be short and rented, and the high frequency element should be surrounded by a large area of grid foil as far as possible.
(2) The ground wire should be as thick as possible. If the grounding wire is very flexible line, the grounding potential changes with the change of current, so that the noise resistance performance is reduced. The ground wire should therefore be thickened so that it can pass through three times the allowable current on the printed board. If possible, the ground cable should be at least 2 mm to 3mm.
(3) The ground wire constitutes a closed-loop road. For printed boards composed only of digital circuits, the ground circuit is arranged into a group loop, which can improve the noise resistance.
10, lotus root capacitor configuration
One of the common practices of PCB design is to configure appropriate decommissioning capacitors in each key part of the printed board.
The general configuration principle of decommissioning capacitance is:
(1) The power input terminal is connected to an electrolytic capacitor of 10 ~100uf. If possible, use * above 100uF.
(2) In principle, each IC chip should be arranged with a 0.01pF ceramic capacitor. If the gap of the printed board is not enough, a 1-10pf capacitor can be arranged every 4-8 chips.
(3) For devices with weak anti-noise ability and large power supply changes when the device is turned off, such as RAM and ROM memory devices, the de-coupling capacitor should be directly connected between the power line and the ground wire of the chip.
(4) The capacitor lead should not be too long, especially the high-frequency bypass capacitor should not have a lead.
11. In addition, the following two points should be noted:
(1) When there are contactors, relays, buttons and other components in the printed board. Large spark discharges will be generated when operating them. ** The RC circuit shown in the attached figure is used to absorb the discharge current. Generally, R ranges from 1 to 2K and C ranges from 2.2 to 47UF.
(2)CMOS has a high input impedance and is susceptible to induction, so the unused end should be grounded or connected to a positive power supply when in use