Building 6, Zone 3, Yuekang Road,Bao'an District, Shenzhen, China
+86-13923401642Mon.-Sat.08:00-20:00
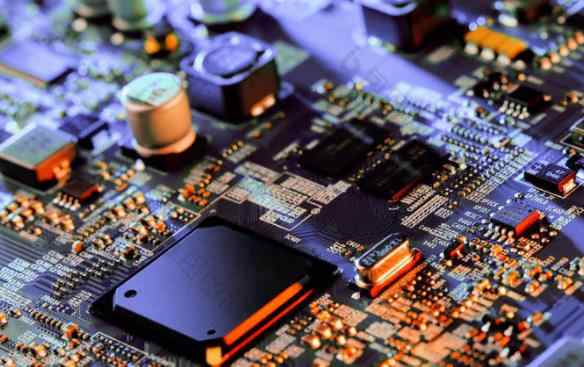
SMT welding assembly and PCBA solder joint failure
Precautions When Soldering Components
In SMT wafer processing, there are many types of components, among which the chip component is the key to SMT assembly and welding technology, affecting product quality and reliability. Chip components are micro electronic components, which have many types, different shapes and physical characteristics. Attention shall be paid to the following items during installation and welding:
1. Before welding, it is necessary to know whether there are special requirements for components, such as welding temperature conditions, assembly methods, etc. Some parts cannot be immersed in tin and can only be welded with electric soldering iron, such as chip potentiometer and aluminum electrolytic capacitor, so you need to choose the correct welding method according to the situation.
2. For parts requiring immersion soldering, it is better to dip only once. Repeated tin dipping will lead to bending of printed boards and cracking of components.
3 SMT repair welding is in progress. In order to prevent static electricity from damaging parts, the electric soldering iron and soldering furnace used should have good grounding devices
5. For rectangular chip capacitors, use capacitors with large appearance, such as 1206, which are easy to weld, but cracks and other thermal damage may occur due to uneven welding temperature; Use capacitors with small appearance, such as 0805, although welding is more difficult, the possibility of cracks and thermal damage is small and the reliability is high.
6. If the PCB board needs to be repaired, the number of disassembly and assembly of components should be reduced as much as possible, because multiple disassembly and assembly will lead to the complete scrapping of the PCB board. In addition, for the hybrid printed circuit board, if the inserted component hinders the disassembly and assembly of the wafer component, it can be removed first.
The welding of SMT wafer components is very complicated. Operators shall learn welding skills, clearly understand precautions, and operate carefully to avoid errors and affect welding quality.
Cause Analysis and Avoidance of PCBA Solder Joint Failure
With the development of science and technology, electronic products are developing towards miniaturization and precision. The PCBA processing and assembly density used by SMT wafer processing plants is getting higher and higher, and the solder joints in circuit boards are getting smaller and smaller. The mechanical, electrical and thermodynamic loads are becoming heavier and heavier, and the requirements for reliability are also increasing. However, PCBA solder joint failures may also be encountered in the actual processing process. It is necessary to analyze and find out the causes to avoid solder joint failures again. A solder joint failure can cause a series of problems. In severe cases, PCB board may be damaged or unknown problems may be caused to the product.
The main reasons for PCBA's failure to process solder joints:
1. Poor component pins: electroplating, pollution, oxidation, coplanar;
2. Bad PCB pads: electroplating, pollution, oxidation, warping;
3. Solder quality defects: components, impurities, oxidation;
4. Quality defects of welding flux: low weldability, high corrosivity and low SIR;
5. Process parameter control defects: design, control, equipment;
6. Defects of other auxiliary materials: adhesives and cleaning agents.
How to improve the reliability of PCBA solder joints:
It is used for PCBA solder joint reliability experiment, including reliability experiment and analysis. Its purpose is to evaluate the reliability level of PCBA integrated circuit devices on the one hand, and provide parameters for the reliability design of the whole machine; On the other hand, this is to improve the reliability of solder joints during PCBA processing This requires necessary analysis of the faulty product to find out the failure mode and analyze the cause of the failure The purpose is to correct and improve the design process, structural parameters, welding process and improve the PCBA processing yield It is very important to predict the cycle life of PCBA solder joints based on the failure mode of PCBA
Precautions When Soldering Components
In SMT wafer processing, there are many types of components, among which the chip component is the key to SMT assembly and welding technology, affecting product quality and reliability. Chip components are micro electronic components, which have many types, different shapes and physical characteristics. Attention shall be paid to the following items during installation and welding:
1. Before welding, it is necessary to know whether there are special requirements for components, such as welding temperature conditions, assembly methods, etc. Some parts cannot be immersed in tin and can only be welded with electric soldering iron, such as chip potentiometer and aluminum electrolytic capacitor, so you need to choose the correct welding method according to the situation.
2. For parts requiring immersion soldering, it is better to dip only once. Repeated tin dipping will lead to bending of printed boards and cracking of components.
3 SMT repair welding is in progress. In order to prevent static electricity from damaging parts, the electric soldering iron and soldering furnace used should have good grounding devices
5. For rectangular chip capacitors, use capacitors with large appearance, such as 1206, which are easy to weld, but cracks and other thermal damage may occur due to uneven welding temperature; Use capacitors with small appearance, such as 0805, although welding is more difficult, the possibility of cracks and thermal damage is small and the reliability is high.
6. If the PCB board needs to be repaired, the number of disassembly and assembly of components should be reduced as much as possible, because multiple disassembly and assembly will lead to the complete scrapping of the PCB board. In addition, for the hybrid printed circuit board, if the inserted component hinders the disassembly and assembly of the wafer component, it can be removed first.
The welding of SMT wafer components is very complicated. Operators shall learn welding skills, clearly understand precautions, and operate carefully to avoid errors and affect welding quality.
Cause Analysis and Avoidance of PCBA Solder Joint Failure
With the development of science and technology, electronic products are developing towards miniaturization and precision. The PCBA processing and assembly density used by SMT wafer processing plants is getting higher and higher, and the solder joints in circuit boards are getting smaller and smaller. The mechanical, electrical and thermodynamic loads are becoming heavier and heavier, and the requirements for reliability are also increasing. However, PCBA solder joint failures may also be encountered in the actual processing process. It is necessary to analyze and find out the causes to avoid solder joint failures again. A solder joint failure can cause a series of problems. In severe cases, PCB board may be damaged or unknown problems may be caused to the product.
The main reasons for PCBA's failure to process solder joints:
1. Poor component pins: electroplating, pollution, oxidation, coplanar;
2. Bad PCB pads: electroplating, pollution, oxidation, warping;
3. Solder quality defects: components, impurities, oxidation;
4. Quality defects of welding flux: low weldability, high corrosivity and low SIR;
5. Process parameter control defects: design, control, equipment;
6. Defects of other auxiliary materials: adhesives and cleaning agents.
How to improve the reliability of PCBA solder joints:
It is used for PCBA solder joint reliability experiment, including reliability experiment and analysis. Its purpose is to evaluate the reliability level of PCBA integrated circuit devices on the one hand, and provide parameters for the reliability design of the whole machine; On the other hand, this is to improve the reliability of solder joints during PCBA processing This requires necessary analysis of the faulty product to find out the failure mode and analyze the cause of the failure The purpose is to correct and improve the design process, structural parameters, welding process and improve the PCBA processing yield It is very important to predict the cycle life of PCBA solder joints based on the failure mode of PCBA
Just upload Gerber files, BOM files and design files, and the KINGFORD team will provide a complete quotation within 24h.