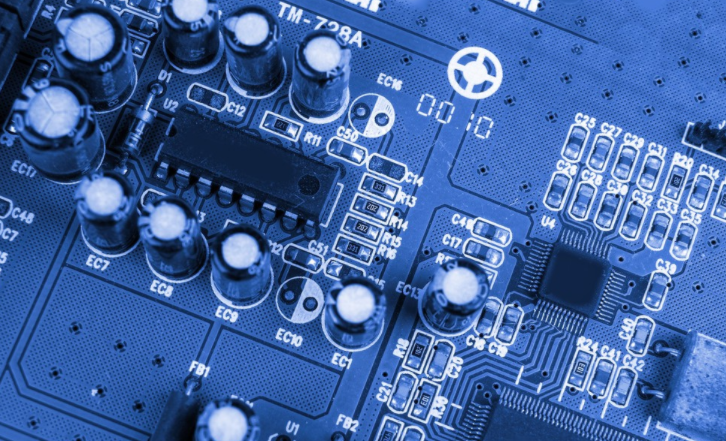
Chip mounter refueling and OI test equipment
On the SMT production line, when a disk of data is almost used up, or when switching production lines, refueling is required Therefore, referring must be operated in accordance with the prescribed referring process Let me share the following cheers with you Process
1. When the equipment data is insufficient, the machine will give an alarm. The production line operator needs to check the reason and then check the website that needs to receive the data.
2. The operator takes down the corresponding materials from the material rack according to the corresponding material number, and then checks whether the material specifications and models are consistent with the station table to avoid errors.
3. The operator compares the new material tray with the old material tray and reconfirms whether the material specifications and models of the material tray are the same.
Circuit board
4. Cut the strips of new and old pallets flat, and connect the strips of new and old pallets (at present, there are automatic splicers, but many companies still rarely use them)
5. Install the feeder back to the spreader trolley, and record the record on the refueling platform, so as to complete a production process of receiving and refueling
OI test equipment processes plants in SMT
AOI's full English name is Automatic Optical Inspection, and its Chinese translation is Automatic Optical Inspection. It is based on optical principle to detect common defects encountered in welding production.
Why use AOI?
--In order to control product quality, the SMT production line shall be effectively inspected to improve production efficiency.
How does AOI detect?
The main purpose of AOI is to detect common defects encountered in welding production. It is a device based on optical principles. AOI is a new detection technology emerging in recent years. At present, there are many AOI brand manufacturers at home and abroad.
When the PCBA board flows into the AOI inspection machine, the PCBA automatically scans through the camera, and the images have been collected. The detected solder joints are compared with the qualified parameters in the database. After image processing, the defects on the PCBA are checked and displayed/marked by the display For maintenance personnel to repair
Where is the AOI on the production line
1. Before reflow soldering
Check whether the electronic components are placed on the PCB board. Before reflow soldering, most defects of solder paste printing and placement machines can be found, especially for products with mask covers. In this way, the quality of solder paste printing and placement components of masked electronic devices can be detected in advance. If the mask covers reflow, if quality problems are found, on the one hand, it is difficult to repair them. AOI cannot detect the quality of welding below the mask covers.
2. After reflow soldering
Check at the end of the SMT process. This is the location where most factories place AOI, because this location can find as many welding defects as possible.
Which companies should establish AOI testing?
1. Customers do not have high quality requirements, but they do not;
2. PCB assembly sizes above 0603 are optional; Generally, manual detection below 0402 is very difficult and requires AOI test equipment to improve efficiency;
3. Low efficiency requirements, but no; On the contrary, if one person replaces three people to improve enterprise efficiency, AOI equipment will be the best choice;
4. Small development scale, optional, small quantity and few products to be tested. Buying AOI equipment is a bit excessive;
In any case, AOI inspection is necessary for SMT processing plants, although it cannot completely replace manual labor.