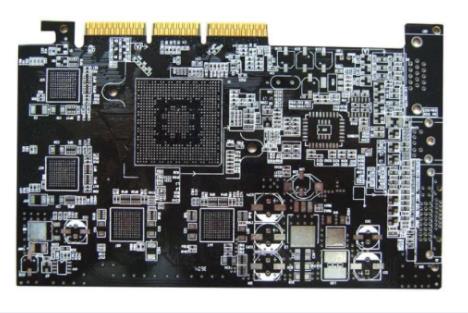
Specification for component insertion and mounting
What should SMT chipprocessing plants pay attention to when producing SMT circuit board chip assembly? Let's take a look at the relevant precautions:
1. Before the smt processing company inserts and pastes, each operator should do a good job of 5S at his own station and around. The main work is: if there are bulk materials or other bulk materials left by the machine type at this station, the material list and operation instructions, etc; The operator shall collect the materials and hand them over to the relevant materialman, foreman or production leader on duty. The materialman, foreman or production leader on duty shall classify, sort out and mark the above items submitted and separate them from online materials.
2. When SMT processing patch row pulling, operators at each station shall conduct self inspection on the operation instructions and material conditions of the station. The specific work is:
1) Whether the operation instructions have been reviewed and officially issued by the document controller, and whether they are ambiguous.
2) Whether the material name/specification on the operation instruction book is consistent with the physical object, whether the point mark on the operation instruction book is consistent with the point to be mounted (inserted), and whether the smt chip DIP material forming meets the point requirements and process standards. In case of any abnormality, it shall be reported in time, and the person in charge of production shall properly handle it together with the Quality Department, Material Department and Engineering Department.
3) All kinds of materials and operation instructions shall be placed in order according to the designated position and clearly marked. There shall be good isolation measures between all kinds of materials. Only after the first piece of DIP materials is inserted (pasted) and confirmed by IPQC or elongating, and the first piece is confirmed as OK by IPQC, can the operators conduct batch insertion (pasted) production.
4) When adding materials, the added materials must be checked by two people (usually the operator himself and the material clerk) before production.
5) If the operator finds any abnormality during smt surface mounting production [such as the point to be inserted (pasted) is occupied by other materials, abnormal pcba, turnover plate, cleaning plate, etc.], he/she shall immediately report it to the shift leader or production director. The leader or production director shall designate a special person to handle it and check the handling results, and then submit it to IPQC for key confirmation.
6) Horizontal components are generally required to be inserted by sticking plates and arranged neatly, with the width consistent with the span of the welding hole, and the error ≤± 0.5mm; The component body of the vertical component shall be vertical to the PCB and pasted. The height of the top bending parts of resistors, diodes, etc. shall be about 1.5-2 mm, and the bending parts shall be neat, continuous and smooth; Pay special attention to the correct direction of directional elements; Prevent flying feet and kneeling feet.