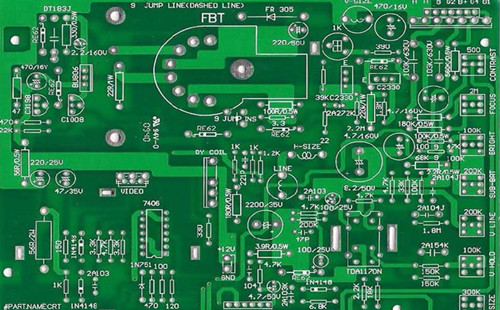
Why does the first part not fall off during SMT secondary reflow soldering?
Why won't the electronic parts that have been punched on the first side of the second reflow melt tin again because of the same high temperature of the second reflow? How much will the melting tin temperature of SAC305 solder paste increase during the second reflow soldering? Why do the electronic parts hit on the first side of the circuit board SMT not fall down when the second side of the circuit board is hit on the second side and passes through the reflow furnace for the second time? Generally, the temperature of the circuit board passing through the second reflow soldering furnace is almost the same, and most of the reflow soldering furnace temperature settings are also up and down
Why won't the electronic parts that have been punched on the first side of the second reflow melt tin again because of the same high temperature of the second reflow? How much will the melting tin temperature of SAC305 solder paste increase during the second reflow soldering?
Why do the electronic parts hit on the first side of the circuit board SMT not fall down when the second side of the circuit board is hit on the second side and passes through the reflow furnace for the second time? Generally, the temperature of the circuit board passing through the second reflow soldering furnace is almost the same, and most reflow soldering furnaces are set at the same temperature as the upper and lower furnaces. So why does the solder paste on the second side of the board melt tin, while the solder paste that has been melted once on the second side does not melt tin again? Is the temperature of molten tin increased during the second reflow soldering of solder paste?
Reflow soldering process for circuit board
I believe many friends who have touched SMT (Surface Mount Technology) have such questions? Or have you ever been asked similar questions? Maybe you vaguely know the answer, but do you really understand why the parts hit on the second side will not fall down in the secondary reflow furnace? Maybe someone told you that the solder paste that has been melted once should be melted again during the second reflow, and its temperature will be about 10 ° C higher than that of the fresh solder paste. But why is the temperature of the solder paste that has been melted once higher when it needs to be melted again?
After a reflow, the melting point of SAC305 may form IMC due to some solder elements (mainly tin and copper, while "silver" will not participate in other reactions after forming Ag3Sn) and the material of the pad or part foot. In addition, some elements of the welding pad or part foot will also be melted into the solder joint, so the composition of solder in a single solder joint will change, no longer the original SAC305 ratio.
As for the range of melting point change, it is difficult to estimate, because the conditions of each part are different. Even on the same PCB, different solder joints may also be different. In addition, the same solder joint may also have different element distribution at different locations (for example, the composition distribution under the QFN part foot and outside the part foot may be different) due to different element diffusion conditions. However, it can be confirmed by comparison that SAC305 is a near eutectic material. Therefore, with a small amount of change in alloy composition, the melting point will still start to melt (eutectic point) from around 217 ° C, and the temperature of complete melting will increase. It is speculated that the average complete melting temperature of the overall solder joint may rise to around 225~230 ° C.
In addition, in general, during the second reflow, there will be oxides on the surface of the first reflow solder joint, and the solder joint lacks the role of flux (the ability of the flux to remove the oxide film is insufficient). Even if the temperature rises to the reflow temperature, the surface oxide tension of the first reflow solder joint will support the shape of the solder joint, so that the appearance of the solder joint will not appear melting collapse because the temperature reaches the solder melting point.
The circuit board manufacturer, circuit board designer and PCBA manufacturer explain why the first part will not fall when SMT reflow soldering for the second time.