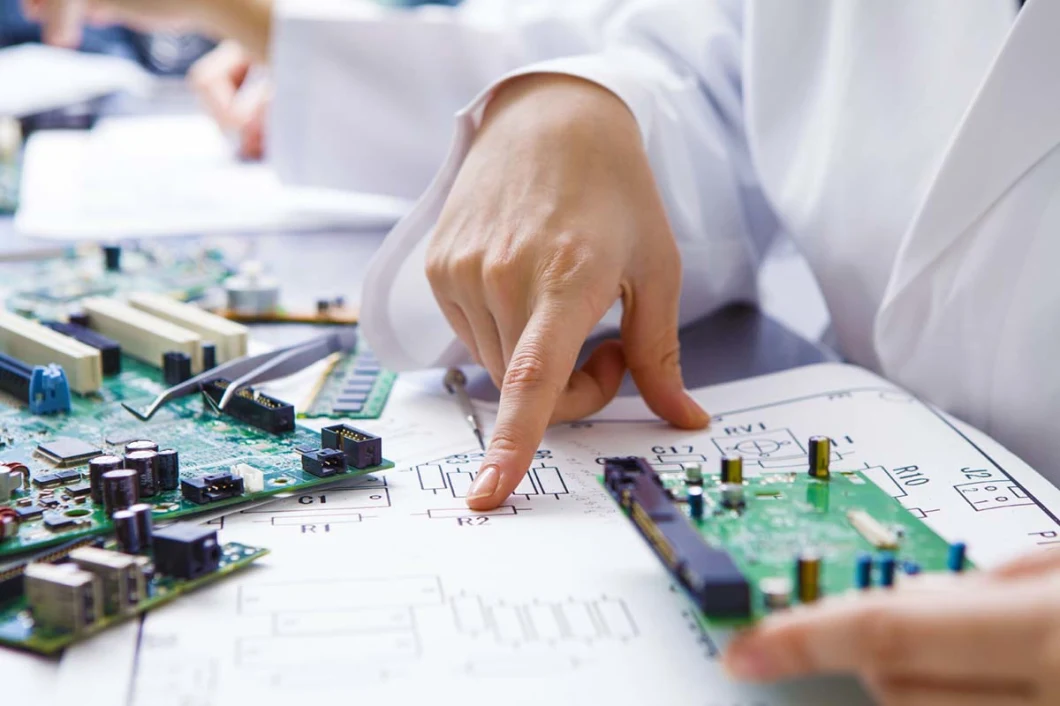
In the welding process of SMT patch processing, the substance that can purify the welding metal and welding surface and help welding is called flux, referred to as flux. Flux is an indispensable process material in the process of soft brazing. Liquid flux is used in wave soldering and manual welding processes. Flux and solder are used separately. In reflow soldering process, flux is used as an important component of solder
paste.
The quality of SMT patch processing welding is also bad, in addition to the quality of solder alloys, components, pcb, welding process, but also with the performance of the flux, the choice of flux has a very important relationship. Next, we will introduce the requirements of SMT patch processing for flux.
1.The appearance of the flux should be uniform, transparent, no precipitation or stratification, no foreign matter. Flux should not emit toxic, harmful or strong pungent odor gases and dense smoke, in order to help protect the environment. During the effective storage period, its color should not change.
2. Smaller viscosity and density than molten solder, easy to be replaced. The flux density can be diluted with a solvent and should be 0.80-0.95g/cm3 at 23 degrees. The no-clean flux should be in the range of (100±1.5) % of its nominal density.
3. The surface tension is smaller than the solder, the wetting expansion speed is faster than the molten solder, and the expansion rate is > 85%.
4. The melting point is lower than the solder, and the flux can give full play to the role of welding aid before the solder melts.
5. the content of non-volatile matter should not be more than 15%, welding does not produce welding bead splash, does not produce poison gas and strong irritating odor.
6. The surface of the residue after welding should be non-sticky, non-touching, and the chalk powder on the surface should be easily removed.
7. No-clean type flux requires solid content <2.0%, no halide, less residue after welding, no moisture absorption, no corrosion, good insulation performance, insulation resistance > 1*10 square ohms.
8. Water cleaning, semi-water cleaning and solvent cleaning types of flux require easy cleaning after welding.
9. Stable storage at room temperature.