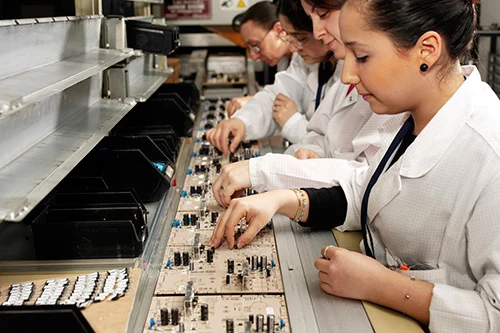
PCB stiffeners play an important role in providing mechanical support for the PCB. They play an important role in PCBA machining of flexible circuit boards when stiffness is required in some places.
PCB stiffeners are particularly required when components are placed in flexible areas, and the weight of these components can put pressure on the flexible material. They can also be used to create rigid printed circuit board surfaces to place parts and welds in SMT machining.In addition, connectors that require multiple inserts require PCB stiffeners to reduce stress on PCB pads. Let's look at the use of PCB stiffeners in more detail.
The various uses of PCB reinforcement?
Simply put, PCB stiffeners are used where an area of the circuit needs to be hardened. Some common reasons for the use of reinforcement in PCBA processing:
1.Board support area with SMT or patch component PTH component.
2. Maintain the reasonable thickness of the flexible circuit.
3. Support PCB connectors.
4. Make sure the board is handled better.
5. Ensure that the circuit board area is stable.
6. Help route and reserve arrays. Helps to eliminate stress and effectively dissipate heat.
In a broad sense, flexible PCB (FPC) reinforcement requirements belong to the following use categories:
1.Rigid component/connector area
2. ZIF(zero insertion force) thickness requirements
3. Local bending constraints
4. Component/connector reinforcement
They essentially create a rigid area connected to that area. They also protect the solder joints to ensure that the flexibility of the component area is not bent. Fourth, ZIF reinforcement.
They ensure increased thickness at the contact points to meet specific requirements of the ZIF connector specifications. 5. Local bending constraint.
They limit the bending area to a specific location in the flexible design.