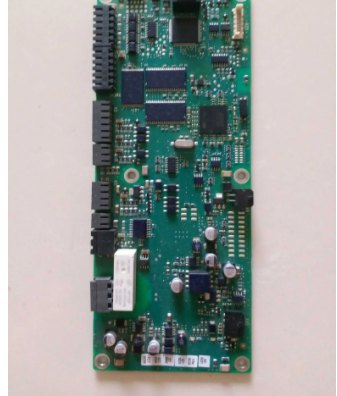
In the SMT processing process, the circuit board reflow welding occurs warping, which will cause poor component welding, stellage, etc., and the next PCBA processing manufacturer kinhford Electronics will introduce it to you PCBA machining method to avoid the warping of PCB board
1. Reduce the influence of temperature on the stress of the boardSince temperature is the main source of stress on the board, as long as the temperature of the backwelding furnace is reduced or the speed of heating and cooling of the board in the backwelding furnace is slowed down, the warping of the PCB board can be greatly reduced. However, other side effects may occur, such as a short circuit in solder.
2. The plate with high Tg is the glass conversion temperature, that is, the temperature at which the material changes from the glass state to the rubber state. The lower the Tg value of the material, the faster the board will start to soften after entering the backwelding furnace, and the longer it will take to become soft and rubber, the more serious the deformation of the board will be. The use of higher Tg sheet can increase its ability to withstand stress and deformation, but the relative price of the material is also relatively high.
3. Increase the thickness of the board
Many electronic products in order to achieve the purpose of thinner, the thickness of the board has been left 1.0mm, 0.8mm, and even 0.6mm thickness, such a thickness to keep the board in the back welding furnace without deformation, really a little difficult, it is recommended that if there is no light and thin requirements, the board can best use 1.6mm thickness, Can greatly reduce the risk of PCB warping and deformation.
4. Reduce the size of the circuit board and reduce the number of panels
Since most of the backwelding furnaces use chains to drive the circuit board forward, the larger the size of the circuit board will sag and deform in the backwelding furnace because of its own weight, so try to put the long side of the circuit board as the board edge on the chain of the backwelding furnace, you can reduce the sag and deform caused by the weight of the circuit board itself, and reduce the number of panels is also based on this reason. That is to say, when the furnace, try to use the narrow side of the vertical direction of the furnace, you can achieve the lowest depression deformation.
5. Used stove tray fixtures
If the above methods are difficult to do, the last is to use the furnace tray (reflow carrier/template) to reduce the deformation of the circuit board, the principle of looking for components on the stock of the furnace tray fixture can reduce the warpage of the PCB board because the fixture material is generally selected aluminum alloy or synthetic stone with high temperature resistance. Therefore, the tray can stabilize the circuit board after the high-temperature thermal expansion of the backwelding furnace and the cold contraction after cooling. When the temperature of the circuit board is lower than the Tg value and begins to recover and harden, it can still maintain the original size.
If the single-layer tray fixture can not reduce the deformation of the circuit board, it is necessary to add a layer of cover, and the circuit board is clamped up with two layers of trays, so that the circuit board can greatly reduce the deformation of the welding furnace. But these trays are expensive, and you have to add people to place and retrieve them. 6. Use the Router instead of the V-Cut
Since V-Cut will destroy the structural strength of the board, try not to use V-Cut boards, or reduce the depth of V-Cut.