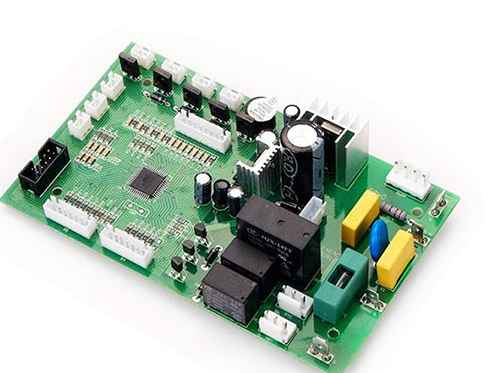
DIP plug-in processing necessary welding process
In the production link of SMT proofing processing, there is a process of DIP plug-in processing, which requires welding, and welding can be divided into soft brazing and hard brazing according to the melting point of the solder. Generally speaking, brazing is a welding with a melting point below 450 degrees Celsius, and the solder used in the DIP plug-in processing of brazing is naturally called soft brazing. At present, various welding methods commonly used in electronic processing plants are generally soft brazing.
①The melting point of brazing filler metal is lower than the melting point of the solder.
② Heat until the filler metal melts and wets the welds.
③ Welding process welding parts do not melt.
④ In order to remove the oxide layer on the metal surface, the welding process needs to add flux.
⑤ The welding process is reversible, can be diswelded, can be repaired.
Whether it is manual welding, dip welding, wave soldering or reflow welding, the welding process must go through several stages of surface cleaning, heating, wetting, diffusion and dissolution, cooling and solidification of the interface of the welded part.
Surface cleaning
Brazing welding can only be done on clean metal surfaces.
The function of this stage is to clean the welded interface of the weldment, and clean the oxide film and attached dirt on the interface. The surface cleaning is completed after the solder is activated by the flux to react with the oxide film on the surface of the solder during heating and before melting.
Heating
Only at a certain temperature can metal molecules have kinetic energy, which can complete wetting, diffusion, dissolution, and formation of binding layers in a very short time. Therefore, heating is a necessary condition for brazing welding.
For most alloys, the ideal brazing temperature is heated to 15.5 to 71 ° C above the liquidus of the filler metal.
Wetting only when the molten liquid filler metal is diffused on the metal surface, can the metal atoms be freely close to each other, so the molten filler metal wetting the weldment surface is the primary condition for diffusion, dissolution, and formation of the bonding layer.
Capillary action, diffusion and dissolution, metallurgical bonding to form the bonding layer after the solder is wetted on the surface of the solder, under the capillary phenomenon, diffusion and dissolution, the bonding layer (weld) is formed after a certain temperature and time, and the tensile strength of the solder joint is related to the structure and thickness of the intermetallic bonding layer.
Cooling, welding completed
Cooling to the solid phase temperature below, after solidification to form a certain tensile strength of the solder joint.
Shenzhen Kingford Technology Co., Ltd. specializes in providing integrated PCBA processing and electronic manufacturing services, including upstream electronic component procurement to PCB production and processing, SMT patches, DIP plug-ins, PCBA testing, finished product assembly and other one-stop services.
The company gives full play to its competitive advantages in scale procurement and quality control, and has signed long-term cooperation agreements with many electronic component manufacturers at home and abroad and around the world to ensure the quality and stable supply of raw materials, and transfer the benefits to customers.