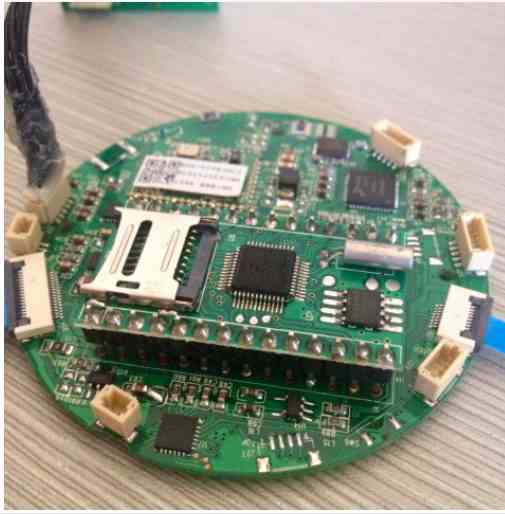
From PCB design to the completion of all components welding, becoming a high-quality circuit board requires the control of PCB engineers, welding processes, welding workers and many other links.
Circuit designers rarely weld circuit boards, can not get rich welding experience, and welding factory workers do not understand the drawing board, just complete the production task, no mind, no ability to analyze the causes of poor welding.
These two aspects of talent each perform their own duties, it is difficult to organically combine. So today, I will share four suggestions for PCB design from the perspective of the drawing board.
Four suggestions for PCB design
1, about positioning holes
The four corners of the PCB board should be left with four holes (minimum aperture 2.5mm) for positioning the circuit board when printing solder paste. The center of the X-axis or Y-axis is required to be on the same axis.
2,About MARK Point
Mark points should be marked on the PCB board for placement machine positioning.
Specific location: On the diagonal of the plate, it can be a round or square pad, and do not mix with the pad of other devices. If there are devices on both sides, both sides should be marked.
3, about 5mm edge
When drawing the PCB, leave no less than 3mm of the edge in the long side direction for the placement machine to transport the circuit board, and the placement machine cannot mount the device in this range. Do not place the patch device within this range.
For the circuit board of the double-sided decoration, consider the problems such as the device rubbing off and the pad rubbing off during the secondary reflow welding.
It is recommended that on the less side of the chip, the long side is within 5mm from the side, do not place the patch device, if it is indeed due to the limited area of the circuit board, you can add the process edge on the long side.
4, do not directly in the pad through the hole
Solder paste will flow into the hole during reflow welding, resulting in solder shortage and virtual welding.
Maximum signal design rate: 10Gbps CML differential signal; Maximum PCB design layer: 40 layers; Minimum line width: 2.4mil; Minimum line spacing: 2.4mil;
Minimum mechanical hole diameter: 6mil; Minimum laser drilling diameter: 4mil; Maximum number of pins:; 63000+ Maximum number of components: 3600; Maximum number of BGA: 48+.
PCB design process
1. Customers provide schematics to consult PCB design;
2. Evaluate quotation according to schematic diagram and customer design requirements;
3. The customer confirms the quotation, signs the contract, and prepays the project deposit;
4. Received advance payment and arranged engineer design;
5. After the design is completed, provide the screenshot of the document to the customer for confirmation;
6. The customer confirmed OK, settled the balance, and provided PCB design information.
Quality control
Quality control of electronic processing is an important step to ensure product quality and production efficiency in electronic processing plants. Taking the reflow process as an example, although the temperature in the furnace can be controlled by the furnace temperature control system and temperature sensor in the reflow furnace, the actual temperature of the solder joint on the PCBA is not necessarily equal to the preset temperature of reflow welding. The SMT patch proofing reflow welding machine works normally, and the temperature control is also within the precision range of the equipment temperature control. pcb board quality. Due to the assembly density and other uncontrollable factors, the furnace temperature curve will fluctuate accordingly. Therefore, the temperature of the reflow welder must be continuously monitored to ensure quality control.
1. Technical requirements for quality control
SMT machining quality control requires technicians to have good measurement knowledge, statistical knowledge, causal analysis ability and in-depth understanding of equipment performance. There are variables on the production line. The aging of equipment, the adjustment of personnel, and the quality of materials will affect and contain each other, making the quality of chip processing products fluctuate.
2. Methods of quality control
At present, in PCBA processing, the introduction of advanced testing equipment for quality control of the production process. In the process of reflow welding, AOI testing equipment is generally used for quality control.
Can provide the smallest package 0201 components SMT processing services. The SMT plant is equipped with 3 Fuji high-speed SMT lines, 2 DIP plug-in production lines, equipped with AOI optical detector, automatic solder paste printing machine, semi-automatic solder paste printing machine, lead-free wave soldering, lead wave soldering, upper and lower 8 temperature zone reflow welding, PCBA functional test frame, aging, board loading machine, cleaning tools, etc., at the same time, a professional research and development laboratory is set up. Five professional engineers cooperate with customers to perform general functional testing, test point testing, as well as channel, noise, waveform, drop and temperature testing.