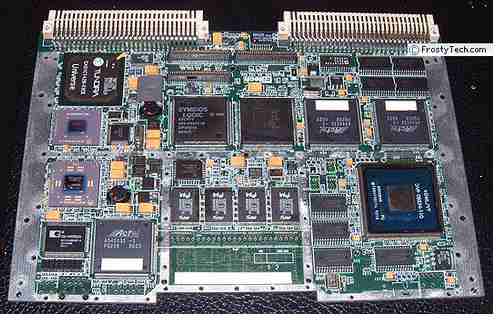
What are the advantages and disadvantages of SMT in printed circuit manufacturing?
Surface Mount technology (SMT) is the process of building electronic circuits in which components are welded directly to the surface of a printed circuit board (PCB). In the technical range, surface mounting has replaced through hole technology. Method used in the process of mounting a component with cable into a hole in the PCB board from the other side of the board through the board.
SMD technology is different in that connections are made through contacts on the underside of the board - metal terminals around the board. Both technologies can be used on the same PCB for non-SMD components, such as transformers and high-power semiconductors in heat sinks.https://www.kingfordpcb.com/yuan.php
An SMT component or SMD (surface mount device) is usually smaller than through-hole technology because it has smaller cables or no cables at all. It can contain electronic pins or wires of different shapes, flat contacts, a tin ball array (BGA-ball grid array Aray connection) or metal terminals at the edge of the circuit. It is obvious that it is difficult to assemble parts by hand using SMD technology, which is why it needs to be automated, for example in large-scale production lines. Making SMD designs work well even in environments with high rates of electromagnetic interference is a very delicate technique.
Surface mount has many benefits. First, the components are small, for example in 2012, the smallest component was 0.4 x 0.2 mm. There is also a better component density, that is, there are more components on each board area (each component also includes more cables). With SMT technology, mechanical properties under vibration conditions can be improved. Lower initial cost, cost and production time - and many surface mount parts cost less than the same parts in through-hole assemblies.
More benefits related to assembly. In the PCB manufacturing process, you don't need to drill as much. Automated assembly is faster and easier; Because some machines are able to install a large number of components in a short time (130,000 components per hour). Similarly, if there are any errors in part placement, they are automatically corrected due to the stress in the melt weld pulling on the part and realigning the part with the welding electrode. Another advantage is that components can be installed on either side of the printed circuit. The low resistance and inductance of the connection results in less excess RF (radio frequency spectrum) effects, as well as better, more predictable high frequency performance.
On the other hand, there are some obstacles to SMT: for example, due to the reduced size and location of many SMDS, prototype assembly or component-level repair is more difficult, requiring more individual skills and expensive tools. In addition, Surface Mount devices do not work with breadboards (prototyping tools), they require PCBS tailored to each prototype, or the device is mounted on a carrier pin with a lead. For prototypes on specific SMD components, a "splitter" board can be used. In addition, slatted prototype boards can be used, some of which include electrodes for standard-sized SMD components. For the manufacture of prototypes, a manufacturing method called "dead bug" can be used)
The welded connections of surface-mount devices may be damaged by thermal cycling of potting compounds. As he develops hyperfine manufacturing techniques, the solder size of SMT joints is rapidly shrinking. Solder joint reliability is becoming more and more consistent, with less solder allowed per joint. When we reflow paste in SMT applications, voids are a problem related to solder joints. The presence of these "zeros" will reduce the strength of the bond and eventually lead to the failure of the bond.
SMT is not suitable and is not suitable for large parts, high power or high voltage - such as where there is a high power circuit. SMT and through-hole technologies are often combined with radiators, large capacitors, firearms, high-power transformers in connectors, and semiconductors. Finally, SMT technology is not suitable for connecting components that are subjected to mechanical stress, such as connectors used to connect to external devices that are frequently connected and disconnected.